Flint & Walling Commander Pro 100 User Manual
Page 3
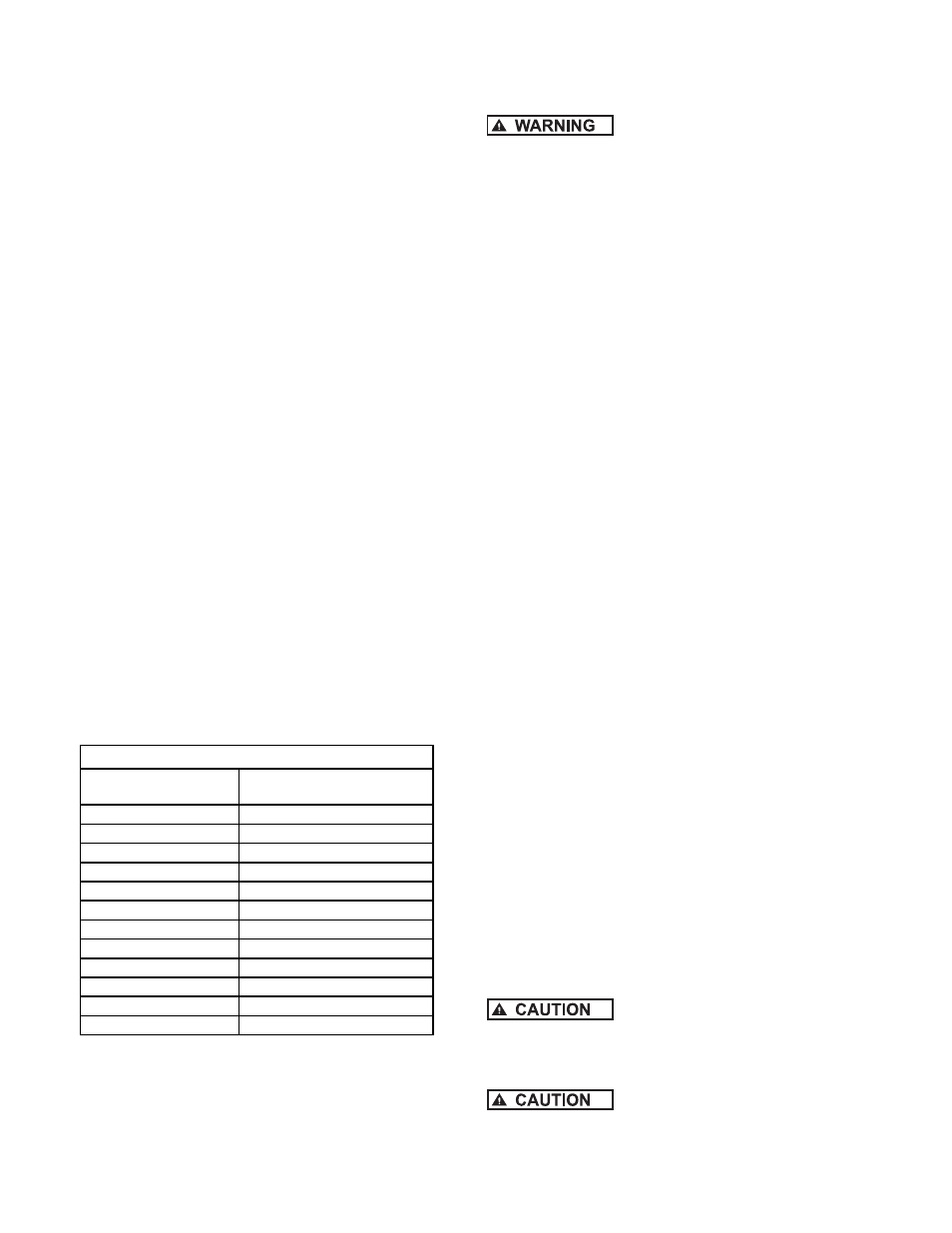
Flint & Walling, Inc. • 95 North Oak Street • Kendallville, IN 46755 • www.flintandwalling.com
© Copyright 2008 Flint & Walling, Inc. All rights reserved.
3
Section 1
System Components
Please be sure that you have all major system
components necessary to properly install the
Commander® Pro 100 Submersible pump system. Other
components may also be necessary depending on the
application requirements.
1. Submersible Pump End
2.
Submersible
Motor
3. CP Water Controller - SubDrive 100
4. Pressure Switch (packaged with controller)
5. Pressure Relief Valve (purchased separately)
6. Pressure Gauge (purchased separately)
Section 2
Piping
General Information
The Commander® Pro 100 system is capable of flows up
to 40 GPM. Discharge piping is recommended to be 1.25”
for installations in which flows will exceed 12 GPM. The
use of smaller pipe will increase friction losses and can
severely limit the maximum capacity of the system.
This pump may be capable of pressures exceeding 325
PSI under maximum conditions, select pipe accordingly.
Consult your pipe supplier to determine the best pipe
material for the installation
Pump Inspection
Prior to installation check the pump, motor, controller and
tank for shipment damage.
Pressure Tank
Use a minimum 4.5 gallon tank to ensure optimum
pressure regulation. An existing, or larger tank can be
used with this system, if desired.
Pressure Setting Guide
System Pressure
(at Pressure Sensor)
Pressure Tank Setting (PSI)
(+/- 2 psi)
25
18
30
21
35
25
40
28
45
32
50 (factory set)
35
55
39
60
42
65
46
70
49
75
53
80
56
Pressure Relief Valve
The pressure relief valve and the discharge outlet need
a flow rating which exceeds the flow capacity of the
installation at the relief pressure. When located in an area
where a water leak or relief valve blow-off may damage
property connect an adequate drain line to the pressure
relief valve. Run the line to a suitable drain or to an area
where the water will not damage property.
Not providing an adequate relief
valve can cause extreme overpressure which could
result in personal and/or property damage. It is
recommended that you manually activate the valve
monthly to keep it in good working order.
Discharge Pipe
When discharge piping requires an adapter it is
recommended that a stainless steel adapter be used.
Galvanized fittings or pipe should not be connected
directly to the stainless steel discharge head of the
Commander Pro pump as galvanic corrosion may occur.
Barb type connectors should always be double clamped.
Torque arrestors are not required on this installation due
to the soft starting characteristics of the Commander® Pro
100 motor and controller
Check Valve
A check valve is factory installed in the discharge head
of the Commander® Pro 100 submersible pump. This
maintains water within the pipe when the pump is not
operating. For well depths exceeding 125 feet, an
additional check valve should be installed every 125 feet.
Safety Rope
A safety rope eyelet is provided at the discharge of the
pump. It is recommended to attach a nylon safety rope.
This will assist in the removal of the pump and also
prevent loss of the unit in the bottom of the well due to a
loose fitting or pipe deterioration.
Section 3
Pump Installation
1.
The following installation instructions as shown
use 160 PSI plastic pipe. Schedule 80 PVC pipe or
galvanized pipe may also be used. If either of these
two types are used, a foot clamp will be required to
hold the PVC or galvanized pipe while connecting the
next length of pipe.
2.
Lay the pump a foot or two from the well, pointing
outward (pump discharge away from the well).
3.
Lay out plastic pipe, safety rope, hose clamps, piping,
tape, submersible cable, etc.
4.
Assembly of all components that go into the well
should be made horizontally on the ground, and then
lowered into the well.
5.
Install a stainless steel pipe adapter in the pump
discharge tapping, using teflon tape.
Do not use pipe wrench on any part
of pump except the cast discharge of the pump.
6.
Unroll plastic pipe in a straight line away from the
pump.
Be sure working surface is smooth
to avoid damage to the plastic pipe and electric cable.
Cut off sealed end of plastic pipe with a hacksaw.