5 emergency handwheel operation, 9 maintenance and care, 10 disassembly – Festo DAPS..R..-F..-MW.. User Manual
Page 4: 11 troubleshooting
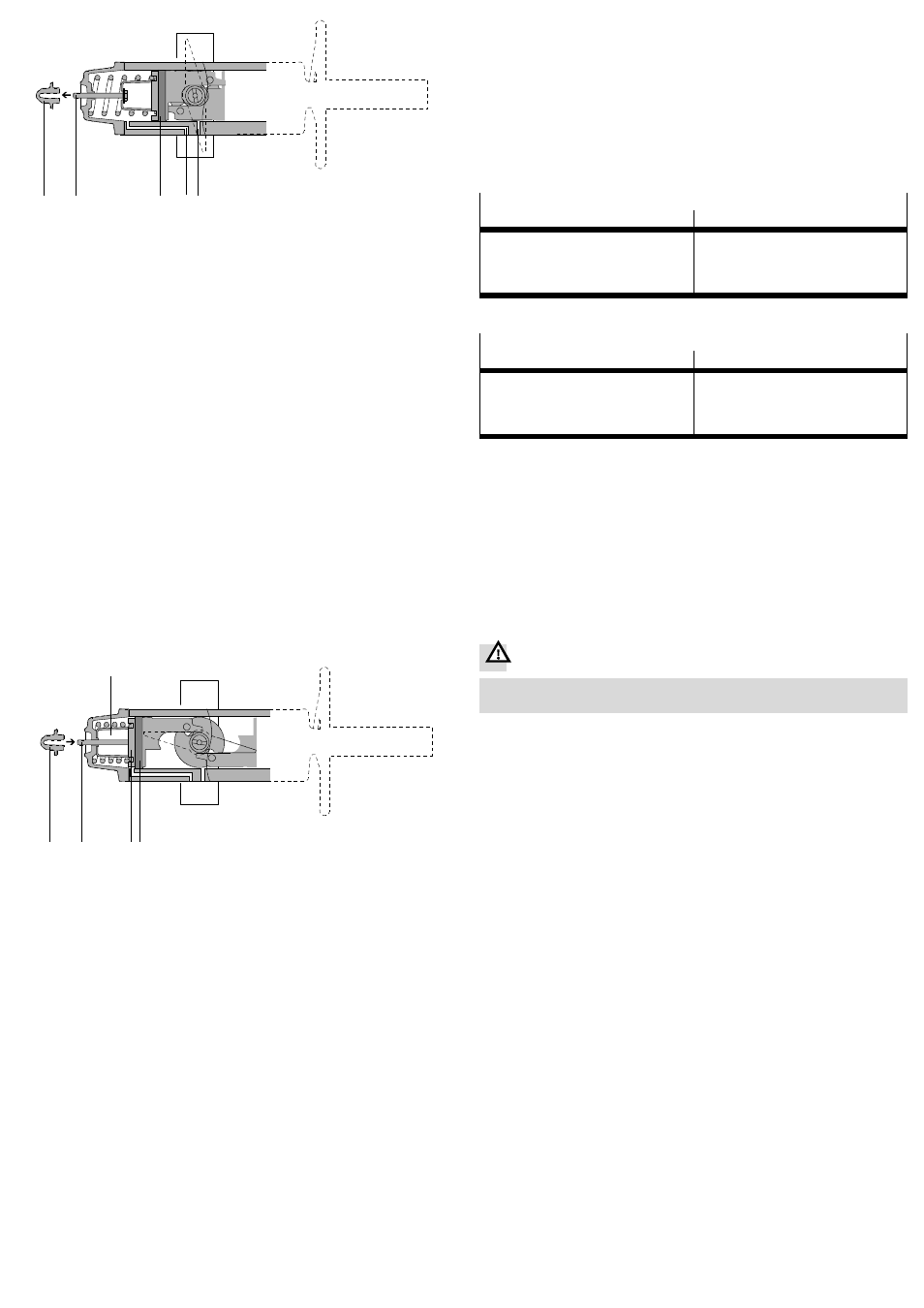
1
2
3 4
5
1 Lock nut with sealing ring
2 Threaded rod
3 Piston
4 Port 2 (A)
5 Port 4 (B)
Fig. 12
1. Vent the DAPS and close the process valve. The pistons run to the inside end
position, as a result of spring return, until the spring disc is held, if necessary, by
the threaded rod. This fixes the threaded rod – dependent on the current set-
ting. Loosening of the lock nut will then not accidentally change the current
setting.
2. Screw down the lock nut with sealing ring. If the threaded rod has loosened,
retighten it by hand until a light resistance is felt.
3. Supply compressed air and open the process valve. The pistons move to the
outer end position.
4. Adjust the end position:
Observe that a complete turn of the threaded rod can change the swivel angle
approx. 1.5° to 3.5° – dependent on the product design.
– Turning the threaded rod clockwise increases the spring travel.
– Turning the threaded rod anti-clockwise reduces the spring travel.
5. Vent the DAPS and close the process valve. The pistons are moved to the inside
end position, as a result of spring force, until the threaded rod and the spring
disc delimit the spring travel.
6. Check the position of the process valve. To change the swivel angle, repeat
steps 3 to 6
7. Retighten the lock nut on the threaded rod – tightening torque 5 Nm.
8. Check the mode of operation of the semi-rotary drive (
section 8.4)
End position for left turning – opening process valve
1
2
3
4
5
1 Lock nut with sealing ring
2 Threaded rod
3 Spring disc
4 Piston
5 Adjustment range of the outer end
position (see technical data)
Fig. 13
1. Supply compressed air and open the process valve. The pistons move to the
outer end position. This fixes the threaded rod – dependent on the current set-
ting. Loosening of the lock nut will then not accidentally change the current
setting.
2. Screw down the lock nut with sealing ring. If the threaded rod has loosened,
retighten it by hand until a light resistance is felt.
3. Vent the DAPS and close the process valve. The pistons move to the inner end
position.
4. Adjust the end position:
Observe that a complete turn of the threaded rod can change the swivel angle
approx. 1.5° to 3.5° – dependent on the product design.
– Turning the threaded rod clockwise reduces the swivel angle.
– Turning the threaded rod anti-clockwise increases the swivel angle.
5. Supply compressed air and open the process valve. The pistons run against the
threaded rods into the outer end position.
6. Check the position of the process valve. To change the swivel angle, repeat
steps 3 to 6.
7. Retighten the lock nut on the threaded rod – tightening torque 5 Nm.
8. Check the mode of operation of the semi-rotary drive (
section 8.4)
8.4 Check the mode of operation of the semi-rotary drive
• Check in cyclical tests, through alternating pressurisation and, if necessary,
venting, whether the semi-rotary drive takes the required positions.
• If necessary, adjust the end positions to the extent the semi-rotary drive offers
this possibility (
section 8.1).
8.5 Emergency handwheel operation
Before operating the handwheel:
1. Make sure the drive is free of pressure.
2. Unhook the locking spring.
3. For the DAPS..R..-F..-MW-T6 “low temperature” version: Remove the protective
cover from the display.
Opening the process valve with the handwheel
DAPS..R-… (double-acting)
DAPS..RS-… (single-acting)
• Turn the handwheel
anti-clockwise
until the indicator moves
inwards
(
Fig. 6).
• Turn the handwheel
anti-clockwise
until the indicator moves
outwards
(
Fig. 7).
Fig. 14
Closing the process valve with the handwheel
DAPS..R-… (double-acting)
DAPS..RS-… (single-acting)
• Turn the handwheel
clockwise until
the indicator moves
outwards
(
Fig. 6).
• Turn the handwheel
clockwise until
the indicator moves
inwards
(
Fig. 6).
Fig. 15
Before pneumatically actuating the drive again:
4. Turn back the handwheel until the indicator is located centrally once again
(neutral position,
Fig. 5).
5. Hook in the locking spring again.
6. For the DAPS..R..-F..-MW-T6 “low temperature” version: Replace the protective
cover on the display.
9
Maintenance and care
If used as intended in the operating instructions, the device will be maintenance-
free.
10
Disassembly
Warning
Danger of injury due to uncontrolled movements.
• Switch the tubing system pressureless before dismantling.
1. If necessary, remove any existing limit switches.
2. Remove the pneumatic switching valve.
3. Loosen the screws on the flange of the process valve.
4. Remove the semi-rotary drive (if necessary including mounting adapter and
coupling extension) from the process valve.
11
Troubleshooting
• Please contact Festo.