2 pneumatic installation, Connections for the compressed air supply, 3 installing circuitry – Festo DAPS..R..-F..-MW.. User Manual
Page 3: 8 commissioning, 1 adjustment of the end positions
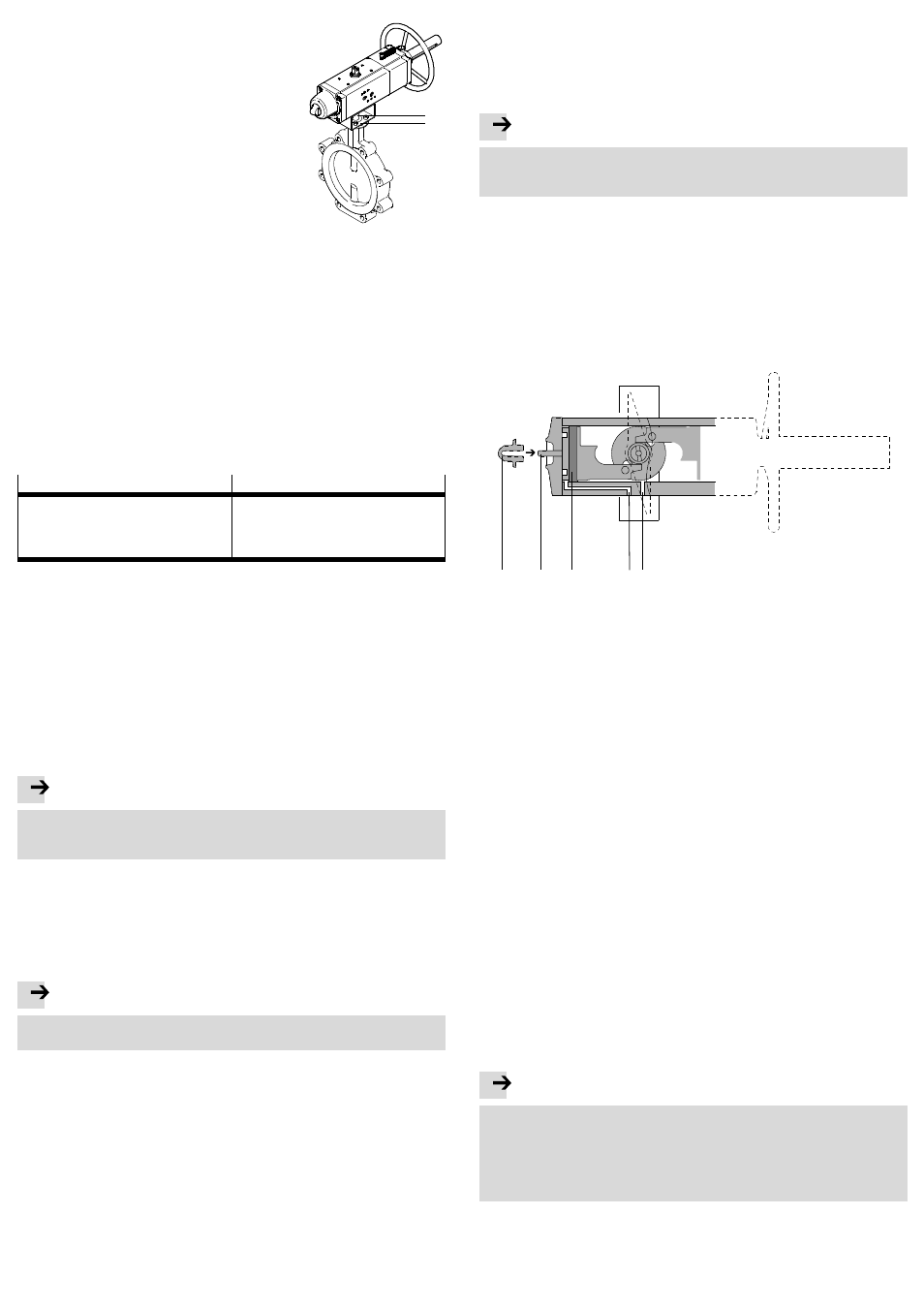
To mount the semi-rotary drive with an adapter
bridge, you need:
Fig. 10
1
2
– an adapter bridge (
Fig. 10,
1 ),
– a shaft extension (
Fig. 10,
2 ).
1. Align the adapter bridge so that its supports are
oriented in the direction of the longitudinal axis of
the semi-rotary drive and, if necessary, the open
side of the adapter bridge towards the process
valve.
2. Fasten the adapter bridge to the semi-rotary drive.
Do not yet tighten the screws.
3. Guide the shaft extension through the adapter
bridge into the star-shaped coupling on the bot-
tom of the semi-rotary drive. Make sure that the
shaft extension sits in the coupling without being
tilted.
4. Fasten the semi-rotary drive with adapter bridge and shaft extension to the
connection flange of the process valve. Make sure here that the square of the
processing valve sits in the shaft extension without being tilted.
5. Tighten all the screws in diagonally opposite sequence.
Tightening torque
Fig. 8.
After fitting the semi-rotary drive:
6. Check that the semi-rotary drive turns in the required direction of rotation and
whether the processing valve assumes the required position.
7. If the semi-rotary drive does not turn in the required direction of rotation:
Carry out the following modification:
DAPS..R-… (double-acting)
DAPS..RS-… (single-acting)
1. Remove the pneumatic solenoid valve.
2. Turn the solenoid valve 180°.
3. Note the position of the threaded pin for
orientation of a NAMUR valve.
4. Fasten the solenoid valve again.
1. Remove the screws on the drive side.
2. Turn the drive 90° while it is still connected
through the shaft extension or directly to the
processing valve.
3. Tighten the mounting screws.
7.2 Pneumatic installation
Connections for the compressed air supply
• DAPS semi-rotary drive, double-acting – standard design
– Air supply at port 2 (A) – see Fig. 1
2
Rotation of the switching shaft in an anti-clockwise direction.
– Air supply at port 4 (B) – see Fig. 1
4
Rotation of the switching shaft in a clockwise direction.
• DAPS semi-rotary drive, single-acting with spring return – standard design
– Air supply at port 4 (B): rotational movement anti-clockwise.
– Spring return: rotation clockwise.
Note
For DAPS..RS-… (single-acting):
• Fasten a filter element to the exhaust port 2 (A) to prevent ingress of dirt
particles.
7.3 Installing circuitry
Using the pneumatic switching valves:
• Please note the instructions and explanations in the relevant operating instruc-
tions for the pneumatic valves.
8
Commissioning
Note
• Make sure that the operating conditions
section 12 lie within the permissi-
ble ranges.
The product is ready for operation as soon as it is installed and connected.
• Make sure that a process valve attached to the semi-rotary drive can be
switched without hindrance.
• When the supply pressure is switched off, set the handwheel to the neutral
position (
Fig. 5) so that the drive can be operated pneumatically.
• Slowly pressurize the semi-rotary drive.
8.1 Adjustment of the end positions
Some product variants offer the possibility to adjust one or even both end posi-
tions of the DAPS within narrow limits in order to influence the closing or opening
angle of the mounted process valve. During adjustment of the end positions, ob-
serve the permissible adjustment range of the DAPS used (
section 12, end
position adjustment range).
Note
Product variants without specification of an adjustment range have
no possibility
for setting end positions, e.g. all product variants made of stainless steel
(DAPS-...-CR).
The now following description for end position setting refers to the following sizes
in the designs “Standard” and “Low temperature” (-T6):
– DAPS-…-R-…(double-acting); size 0015 up to 1920 (
section 8.2)
– DAPS-…-RS.. (single-acting); size 0015 up to 0960 (
section 8.3)
Information on adjustment of the end position for other sizes can be found, if ap-
plicable, in the appendix to the operating instructions supplied with the product
(
www.festo.com).
8.2 Adjustment for the DAPS-…-R-… (double-acting) – size 0015 … 1920
For these product variants, the end position that the drive takes during venting
through port 4 (B) can be adjusted (turn to the right - close process valve).
1
2
3
5
4
1 Lock nut with sealing ring
2 Threaded rod
3 Piston
4 Port 2 (A)
5 Port 4 (B)
Fig. 11
1. Supply compressed air and close the process valve. The pistons move to the
outer end position. This fixes the threaded rod – dependent on the current set-
ting. Loosening of the lock nut will then not accidentally change the current
setting.
2. Screw down the lock nut with sealing ring. If the threaded rod has loosened,
retighten it by hand until a light resistance is felt.
3. Supply compressed air and open the process valve. The pistons move to the
inner end position.
4. Adjust the end position:
Observe that a complete turn of the threaded rod can change the swivel angle
approx. 1.5° to 3.5° – dependent on the product design.
– Turning the threaded rod clockwise reduces the swivel angle.
– Turning the threaded rod anti-clockwise increases the swivel angle.
5. Supply compressed air and close the process valve. The pistons run against the
threaded rod into the outer end position.
6. Check the position of the process valve. To change the swivel angle, repeat
step 3 and 4.
7. Retighten the lock nut on the threaded rod – tightening torque 5 Nm.
8. Check the mode of operation of the semi-rotary drive (
section 8.4)
8.3 Adjustment with the DAPS-…-RS.. (single-acting) – size 0015 to 0960
For these product variants, one of the two end positions of the DAPS can be adjus-
ted – either the end position for right turning or the end position for left turning.
End position for right turning – closing process valve
Note
For the single-acting DAPS, the end position setting for right turning (closing
process valve) does not have a mechanical stop, since the spring disc is not
mechanically connected to the piston. The threaded rod therefore limits only the
path of the return spring so that the piston comes to rest without spring force.
But the piston movement or turning of the shaft is not mechanically limited and
can be continued through external forces.