Enerpac ASC-Series User Manual
Page 2
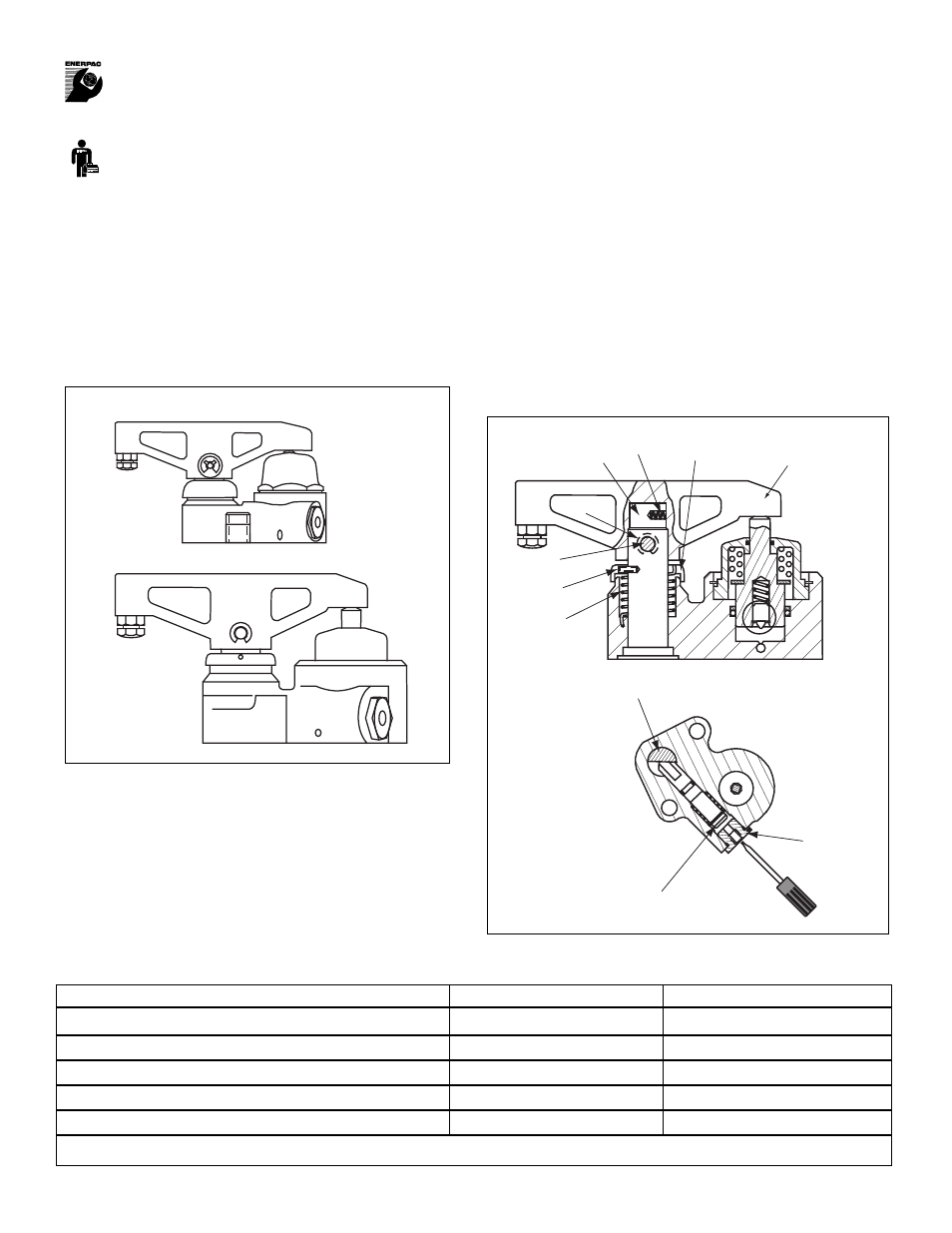
2
IMPORTANT: Hydraulic equipment must only be
serviced by a qualified hydraulic technician. For repair
service, contact the Authorized ENERPAC Service Center
in your area. To protect your warranty, use only ENERPAC oil.
WARNING: Immediately replace worn or damaged parts by
genuine ENERPAC parts. Standard grade parts will break
causing personal injury and property damage. ENERPAC
parts are designed to fit properly and withstand high loads.
3.0 DESCRIPTION
Enerpac ASC Swing Clamps have a clamping arm that swings in
a clockwise (R.H.) rotation 97° to position itself over the
workpiece. Then, a vertical plunger exerts an upward thrust on the
back end of the swing arm providing a powerful downward
pressure to clamp the workpiece. Swing clamp arm direction can
be changed to counter-clockwise (L.H.) rotation. See section 4.1.
Figure 1
4.0 INSTALLATION
4.1 Changing Rotation Direction
All Enerpac ASC Swing Clamps are assembled to swing
clockwise (R.H.). Follow instructions below to change rotation to
counter-clockwise (L.H.) and refer to Figure 2.
1.
Remove retaining ring (1) and fulcrum pin (2) and lift off
clamping arm (3).
2.
Remove arm spring (4). Mark the position of the spring on the
fulcrum (5).
3.
Unscrew set screw (6) and remove cover (7).
4.
Remove R.H. torsion spring (8) and replace with L.H. torsion
spring (supplied with cylinder).
5.
Replace cover (7) making sure the top tongue of the torsion
spring (8) locates in the hole in the cover.
6.
Turn cover (7) counter-clockwise 90° to load spring (8).
7.
Tighten set screw (6) making sure the point engages the hole
in the swivel fulcrum (5).
8.
Loosen inlet plug three turns (9). Insert a screwdriver through
the inlet bushing (9) and rotate the plunger (10) 180°.
9.
Retighten inlet plug (9).
10. Use screwdriver to push plunger (10) to bottom to rotate the
swivel fulcrum (5) and check for proper rotation direction.
11. Replace arm spring (4) in clamping hole at 90° from original
position.
12. Place clamping arm (3) in opposite "at rest" position.
13. Insert fulcrum pin (2) and replace retaining ring (1).
Figure 2
2
6
8
7
4
Top View
9
10
5
3
5
1
ASC-30
ASC-100
Specifications
ASC-30
ASC-100
Rated capacity (lbs.)
1,375
4,375
Rated operating pressure (psi)
1,200 to 2,500 max.
1,200 to 2,500 max.
Hydraulic port
0.125-27 NPT
0.125-27 NPT
Hydraulic Plunger Stroke (in)
0.25
0.43
Clamping volt length (in)
0.75 min.*
0.73 min.*
* Clamping bolt length can be changed to accommodate lower clamping height.