Carbolite PTC 12/20/150 User Manual
Page 10
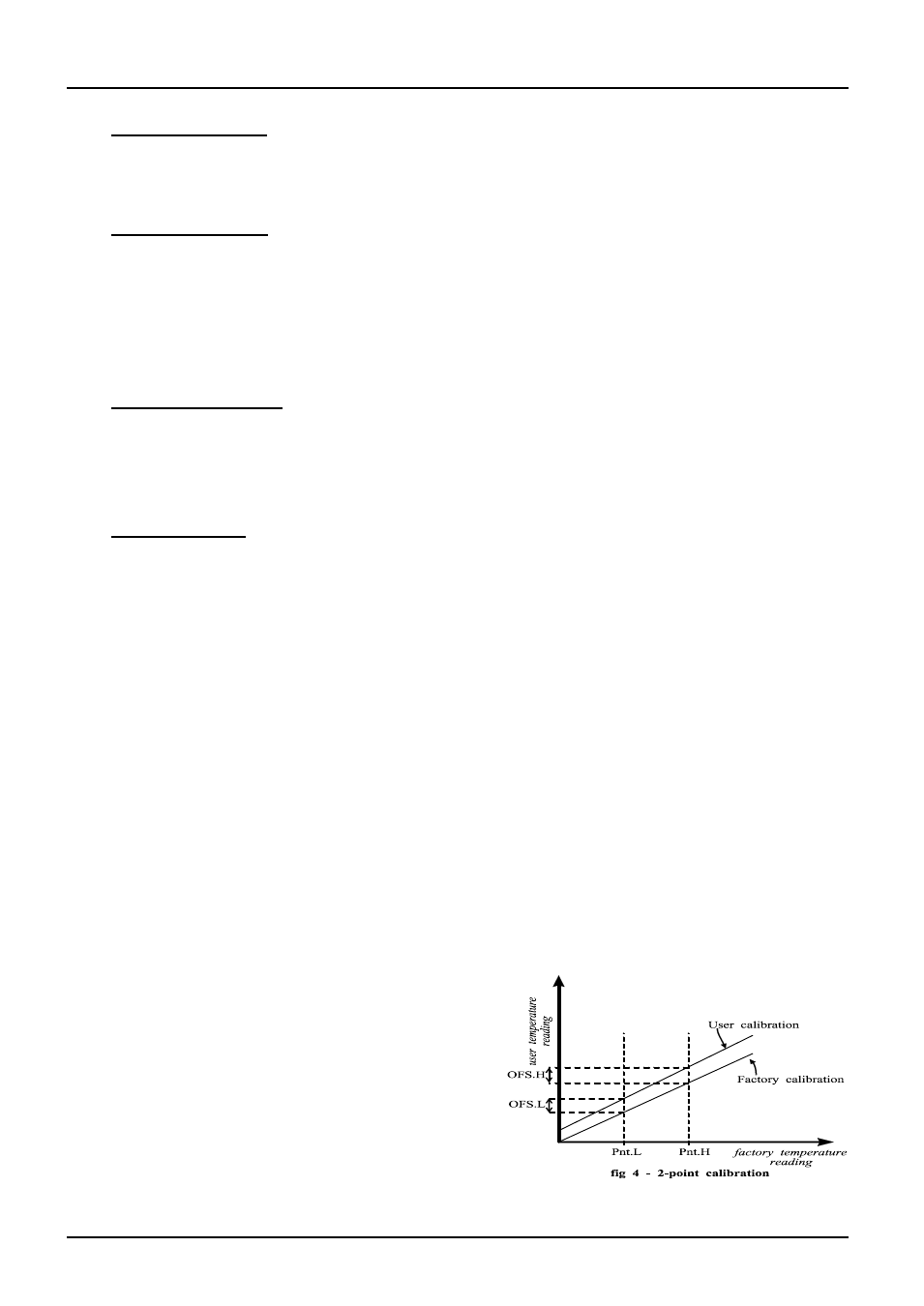
PTC
10
MF11 – 3.08
4.11 Stopping the Timer
To stop the timer at any time while it is running, change the
StAt
parameter to
OFF
. This is the
same as reducing
tmr
to zero. The controller then acts as though at has reached the end of the time
period.
4.12 End of Time Period
Modes 1 and 3: heating stops at the end of timing; the
m-A
parameter changes to
mAn
.
Modes 2 and 4: heating continues at the end of timing; the
m-A
parameter remains at
Auto
.
Mode 5: heating starts at the end of the timing period; the
m-A
parameter remains at
Auto
.
In modes 1 to 4 the alarm message
EnD
flashes on the display at the end of timing; the
StAt
parameter remains at run.
In mode 5 there is no
End
message; the
StAt
parameter changes to
OFF
at the end of timing.
4.13 Cancelling the Alarm
To acknowledge (cancel) the
EnD
alarm, press Page and Scroll together; the
StAt
parameter
changes to
OFF
.
Alternatively the alarm may be cancelled by directly changing the
StAt
parameter from
run
to
OFF
.
4.14 User Calibration
The controller is calibrated for life at manufacture against known reference sources, but there may
be sensor errors or other system errors. User calibration allows compensation for such errors, and
the 2132 allows for a user 2-point calibration. This setting is password protected to avoid
accidental alteration.
Page to
iP
, scroll to
CAL.P
, and use Up to alter the password. The password is
3
. If the correct
password is entered, the display shows
PASS
. Scroll to
CAL
and use or to observe the setting
FACt
(factory values, as manufactured) or
USEr
(user values). Change to
USEr
.
NOTE: before checking the calibration of the controller, or of the complete system, remember to
reset the 2132 to factory calibration values by setting the
CAL.P
parameter to
FACt
.
To enter a user calibration, scroll to each or the following parameters in turn and set the desired
values.
Pnt.L
low temperature for which an offset is to be entered
OFS.L
offset value for the low temperature
Pnt.H
high temperature for which an offset is to be entered
OFS.H
offset value for the high temperature
Example: the controller reads 3°C low at 400°C, and 5°C low at 1000°C. The parameter values
should be
Pnt.L=400
,
OFS.L=3
,
Pnt.H=1000
,
OFS.H=5
.
Negative or positive values can be entered: if the
controller is reading high, negative offsets
would be appropriate.
Fig 4 gives a graphical representation of the 2-
point calibration.