V-belts – Aerovent IM-977 User Manual
Page 4
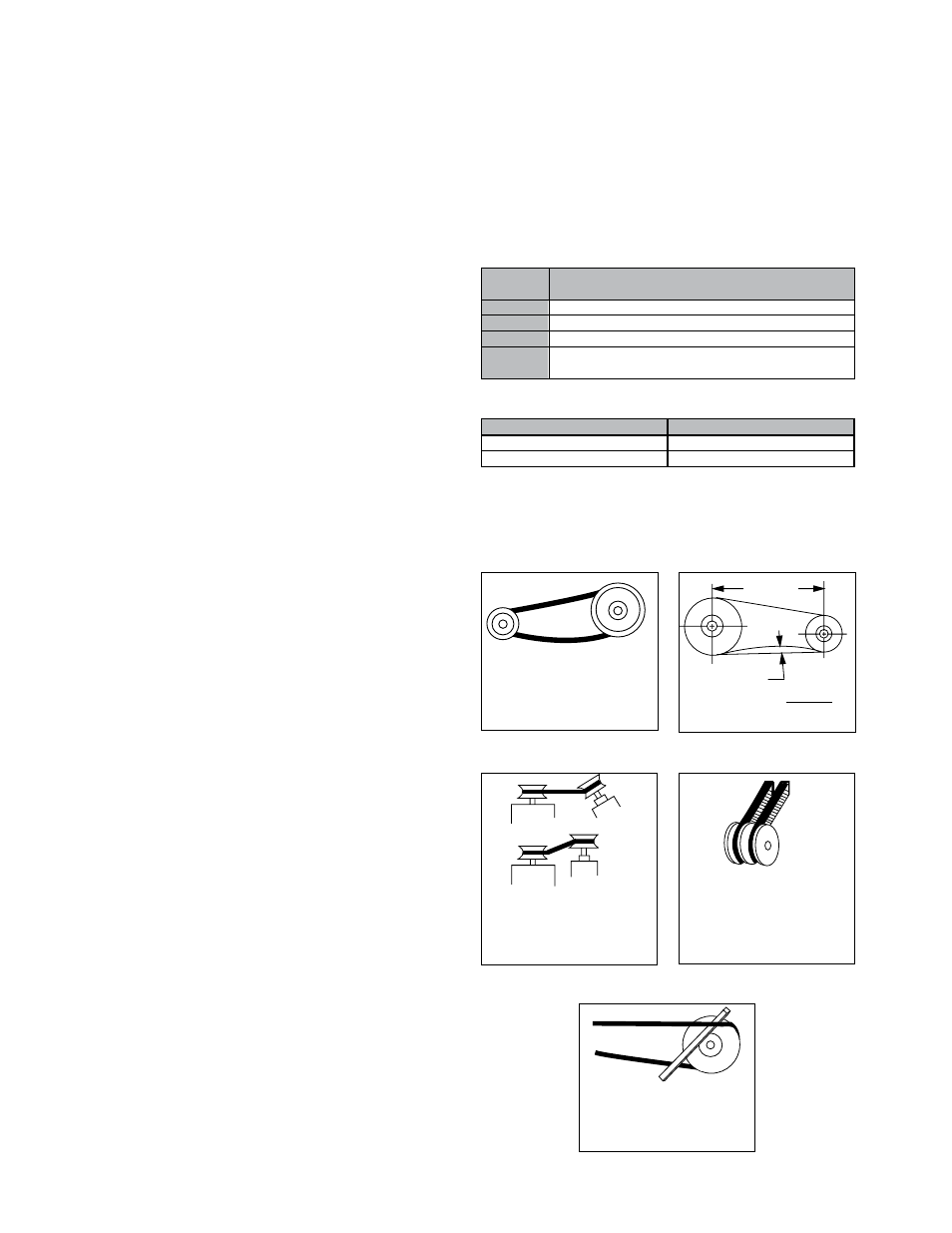
4
Aerovent IM-977
INTERVAL
TYPE OF SERVICE
(MONTHS)
12 to 18
Infrequent operation or light duty in clean atmosphere.
6 to 12
8 to 16 hrs./day in clean, relatively dry atmosphere.
3 to 6
12 to 24 hrs./day, heavy duty, or if moisutre is present.
1 to 3
Heavy duty in dirty, dusty locations; high ambient temps;
moisture laden atmosphere; vibration.
MANUFACTURER
GREASE (NLGI #2)
Shell
Gadus S2 V100 2
Exxon/Mobil
Ronex MP
Figure 1. Eliminate Slack
Figure 2. Belt Deflection
Figure 3. Alignment
Figure 4. Two-GrooveSheaves
Figure 5. Belts
Deflection
Deflection = Belt Span
64
Belt Span
NOT THI
S
Slack belts wear excessively,
cause slippage and deliver less
power. For longest belt life,
always provide proper tension.
Mount belts straight. Shafts
must be parallel and sheaves in
alignment to prevent unneces-
sary belt wear.
Two-groove variable pitch
sheaves must be opened the
same number of turns on both
sides; otherwise, slippage
occurs, wearing belts rapidly.
Don’t force belt. Forcing the
belt will break the cords and
cause belt failure.
V-Belts
V-belts on these belt driven fans are oil, heat, and static
resistant type and oversized for continuous duty. With
proper installation and maintenance, years of operating
efficiency can be added to the lifespan of the V-belt
drive.
The condition of the V-belts and the amount of belt ten-
sion should be checked prior to startup (see Figure 1).
When it becomes necessary to adjust belt tension, do not
over-tension as bearing damage will occur. Recommended
belt tension should permit
1
⁄
64
" deflection per inch of the
span of the belt at the center of the belt span. To find
this point, measure halfway between the pulley centerlines
as shown in Figure 2. Extreme care must be exercised
when adjusting V-belts as not to misalign the pulleys. Any
misalignment will cause a sharp reduction in belt life and
will also produce squeaky, annoying noises (see Figure
3). On units equipped with 2 or 3 groove pulleys, adjust-
ments must be made so that there is equal tension on
all belts (see Figure 4).
1. Where tensioning rods are not provided, adjustment is
more easily obtained by loosening and adjusting one
side of the motor bracket at a time.
2. Always loosen tension adjustment enough to place
belts on sheaves without running belts over the edge
of either sheave. A new belt may be seriously dam-
aged internally by careless handling (see Figure 5).
WARNING: When removing or installing belts, never force
belts over pulleys without loosening the motor first to
relieve belt tension. The fan has been checked for
mechanical noises at the factory prior to shipment. If
mechanical noise should develop, some suggestions are
offered here as a guide toward remedying the cause.
1. Check rotating members for adequate clearance.
2. Check proper belt tension and pulley alignment.
3. Check installation and anchoring.
4. Check fan bearings.
9. Check sheave setscrews to ensure tightness. Proper
keys must be in keyways.
10. Do not readjust fan RPM. If sheaves are replaced,
use only sheaves of identical size and type.
11. If the unit is to be left idle for an extended period,
it is recommended that the belts be removed and
stored in a cool, dry place to avoid premature belt
failure.
12. The standard pillow block bearings on belt driven
ventilators are factory lubricated and are provided
with external grease fittings. Relubrication annually
or more frequently is recommended. See Table 3.
Do not over-grease. Use only 1 or 2 shots of
recommended lubricant with a hand gun in most
cases. See Table 4. The maximum hand gun rating
is 40 P.S.I. Rotate bearings during lubrication where
good safety practice permits.
CAUTION: Greases of different soap bases (lithi-
um, sodium etc.) may not be compatible when
mixed. Prevent such intermixing by completely purg-
ing the bearing of old greases.
The most frequent causes of bearing failure are
not greasing often enough, using an excessive
quantity of grease, or using incompatible greases.
Excessive vibration, especially if the bearing is not
rotating, will also cause bearings to fail. Bearings
must also be protected from water and moisture to
avoid internal corrosion.
13. During the first few months of operation it is recom-
mended that the setscrews be checked periodically
to assure they are tight.
14. The rotating wheel requires particular attention since
materials in the air being handled can build up on
the blades to cause destructive vibration or weaken
the structure of the wheel by corroding and/or erod-
ing the blade metal. Regular inspection and correc-
tive action at intervals determined by the severity of
each application are essential to good service life
and safety.
Table 3. Suggested Fan Bearing Greasing Intervals
Table 4. Grease Manufacturers