Maintenance, Warning – Aerovent IM-167 User Manual
Page 7
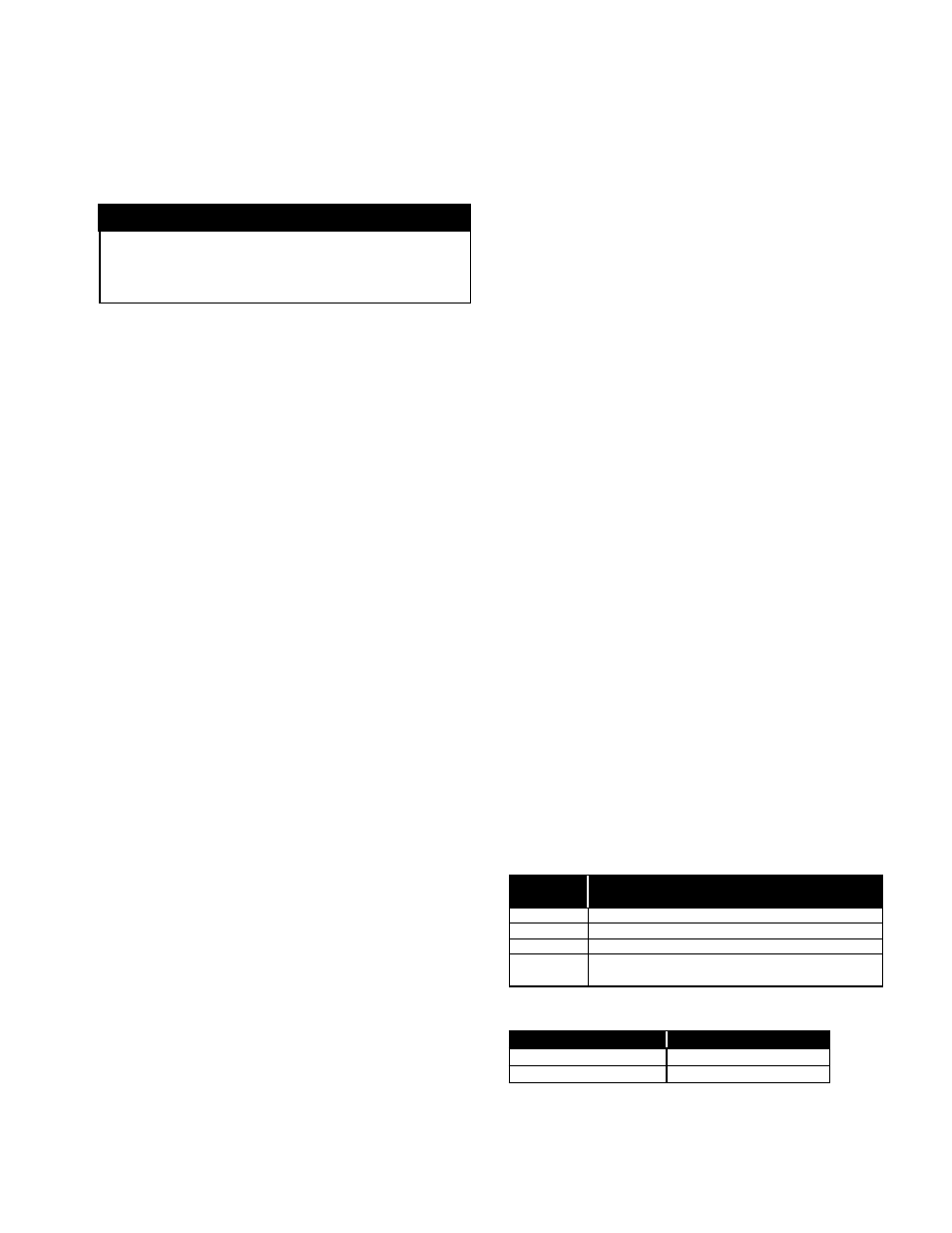
Aerovent IM-167
7
Maintenance
Installation and maintenance are to be performed only
by qualified personnel who are familiar with local codes
and regulations and experienced with this type of equip-
ment.
CAUTION: Sharp edges and screws are a potential injury
hazard. Avoid them.
WARNING
Hazardous moving parts. Unit may contain pro-
tected fan motor which may start automatically
and cause injury. Allow time for reset. Disconnect
power before servicing.
Preventive maintenance is the best way to avoid unnec-
essary expense and inconvenience. Routine maintenance
should cover the following items:
a. Tighten all setscrews, bolts and wire connections.
b. Check belt tension and sheaves for wear.
c. Lubricate fan bearings (see Tables 5 and 6).
d. Cleaning of unit, wheel and damper (if present).
All motors containing ball bearings are permanently
lubricated from the factory. No additional maintenance
is required.
1. Before performing any maintenance on the fan, be
sure power is turned off and locked in the OFF
position at the service entrance.
2. Fans should be carefully checked at least once a
year. For critical or rugged applications, a routine
check every two or three months is suggested.
3. For repairs within the warranty period, the motor
must be taken to the motor manufacturer’s autho-
rized service dealer.
4. A periodic motor check should consist of spinning
the motor shaft with the power off to be sure the
motor turns freely and the bearings run smoothly.
The belt on belt driven units should be removed
from the motor sheave.
5. When removing or installing a belt, do not force
the belt over the sheave. Loosen the motor mount
so that the belt can be easily slipped over the
sheave.
6. The belt on belt driven units should be removed and
carefully checked for glazing, cracks, ply separation
or irregular wear. A small irregularity in the contact
surface of the belt will result in noisy operation. If
any of these defects are apparent, the belt should
be replaced. Check the sheaves also for chipping,
dents or rough surfaces which could damage the
belt.
7. The correct belt tension is important. Too tight of
a belt will result in excess bearing pressure on the
motor bearings and shaft pillow blocks and may
also overload the motor. Too loose of a belt will
result in slippage which will quickly “burn” out belts.
A belt should feel “live” when thumped, approxi-
mately
1
⁄
4
" belt deflection (3 to 5 lb.) when subject
to finger pressure at midpoint between sheaves.
8. The belt alignment should also be checked to be
sure the belt is running perpendicularly to the rotat-
ing shafts. Fan and motor shafts must be paral-
lel. Improper alignment will result in excessive belt
wear.
9. Check sheave setscrews to ensure tightness. Proper
keys must be in keyways.
10. Do not readjust fan RPM. If sheaves are replaced,
use only sheaves of identical size and type.
11. If unit is to be left idle for an extended period, it is
recommended that belts be removed and stored in
a cool, dry place to avoid premature belt failure.
12. The standard pillow block bearings on belt driven
fans are factory lubricated and are provided with
external grease fittings. Lubrication annually is recom-
mended, or more frequently if needed (see Table 5).
It is recommended to add fresh grease at start-
up. Use only 2 or 3 shots of a recommended
lubricant with a hand gun in most cases (see Table
6). Maximum hand gun rating 40 P.S.I. Rotate bear-
ings during lubrication where good safety practice
permits.
CAUTION: Greases of different soap bases
(lithium, sodium, etc.) may not be compatible when
mixed. Prevent such intermixing by completely purg-
ing the bearing of old greases.
The most frequent causes of bearing failure are
not greasing often enough, using an excessive
quantity of grease, or using incompatible greases.
Excessive vibration, especially if the bearing is not
rotating, will also cause bearings to fail. Bearings
must also be protected from water and moisture to
avoid internal corrosion.
13. During the first few months of operation it is rec-
ommended that the bearing setscrews be checked
periodically to ensure that they are tight.
14. The rotating wheel requires particular attention since
materials in the air being handled can build up on
the blades to cause destructive vibration or weaken
the structure of the wheel by corroding and/or erod-
ing the blade metal. Regular inspection and correc-
tive action at intervals determined by the severity of
each application are essential to good service life
and safety.
INTERVAL
TYPE OF SERVICE
(MONTHS)
12 to 18
Infrequent operation or light duty in clean atmosphere.
6 to 12
8 to 16 hrs./day in clean, relatively dry atmosphere.
3 to 6
12 to 24 hrs./day, heavy duty, or if moisture is present.
1 to 3
Heavy duty in dirty, dusty locations; high ambient
temperatures; moisture laden atmosphere; vibration.
Table 5. Suggested Fan Bearing Greasing Intervals
Table 6. Grease Manufacturers
MANUFACTURER
GREASE (NLGI #2)
Shell
Shell Gadus S2 V100 2
Exxon/Mobil
Ronex MP