Installation in explosive and fire danger zones, Description, Function – Micropump EagleDrive ELE User Manual
Page 7
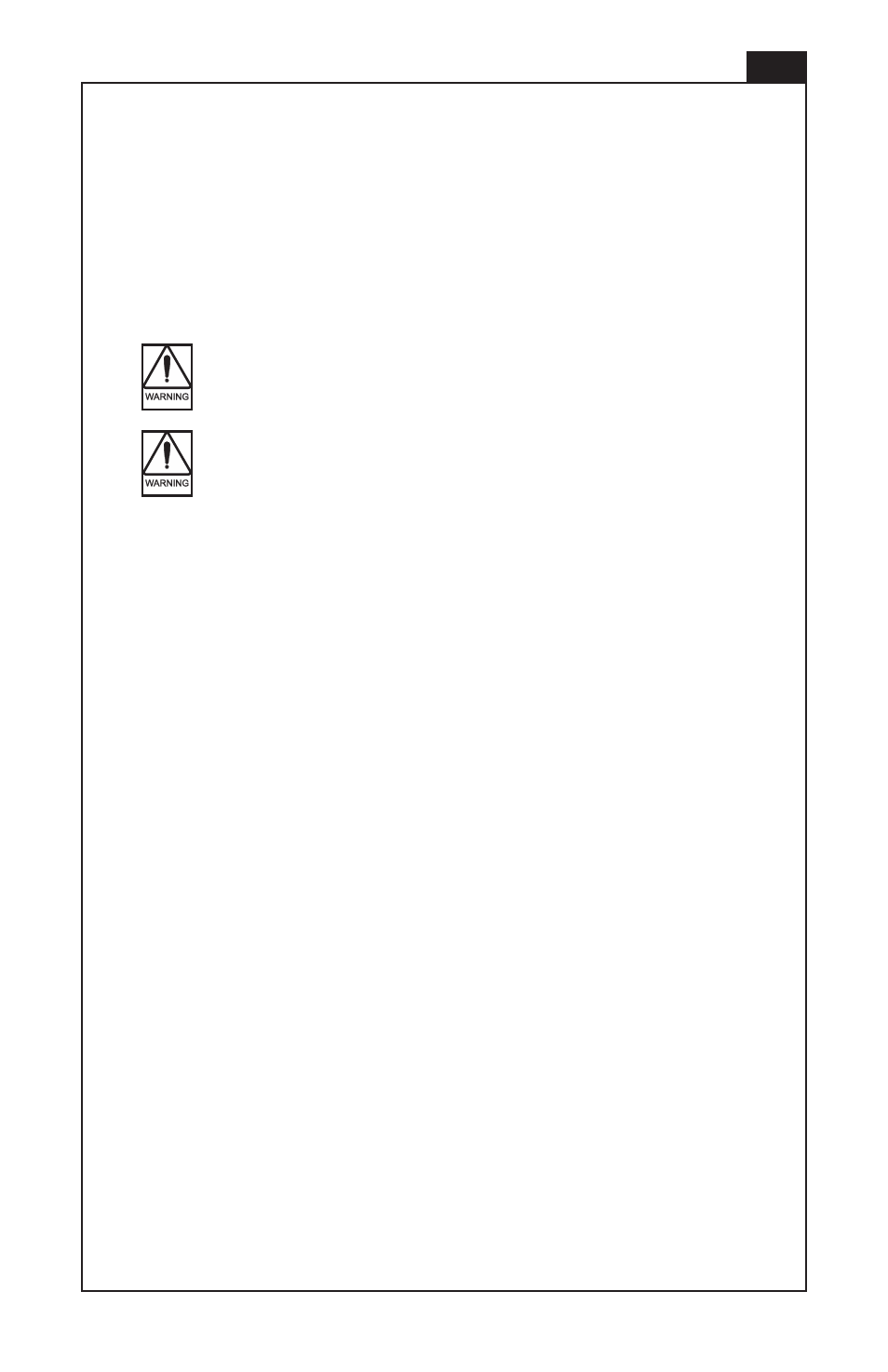
7
DOC No: 8540 REV D
Installation in Explosive and Fire Danger Zones
Micropump offers products designed and tested for installation in explosive or fire danger
zones. Contact your local Micropump distributor or contact Micropump directly to deter-
mine if your EagleDrive product combination can be certified for this use.
In Addition to the warnings provided throughout this manual, the following must be
considered in any explosion or fire danger zone installation:
Ensure the pump head, motor, and any mounting adapter are suitable for
area classification.
Description
The EagleDrive is a brushless DC motor with integrated controller specially designed to
be electromagnetically coupled to a variety of Micropump pump heads. When properly
assembled to the pump head with sealing o-ring, this comprises a sealed unit where
the driven magnet is within a magnet cup that separates the pumped fluid from the
atmosphere.
The enclosed versions are within a thermoplastic housing. The motor is capable of
rotating in both directions and has several speed control input options. A tachometer
signal, with a 0-5 V square-wave output provides speed feedback. The tachometer
output has 2 pulses per revolution. The output frequency is multiplied by 30 to obtain
RPM. The main input power is 12-36 VDC from a class 2 (SELV) source.
There are two EagleDrive models, the MS and EL. Both models operate from 12-36
VDC, with speed control input, 0-5V square wave tachometer feedback, and FWD/REV
capabilities. Instructions for utilizing other speed input signals are provided in this manual.
Both EagleDrive models can be controlled using one of these options:
1. Externally applied 0-5 VDC supply
2. Externally applied 4-20 mA signal (conditioned with external resistor)
3. Manually-adjusted speed control (through use of external potentiometer)
Function
The driven magnet is connected to the pumping parts and is sealed in the magnet cup.
This magnet forms the rotor of the brushless DC motor and is driven by the rotating
magnetic field in the stator. Rotation of the pumping elements produces flow.
The control signal controls pump speed. Internal feedback monitors the rotational speed
of the pump and regulates the speed in relation to the control voltage. The controller
increases current to regulate speed against increasing back pressure (within the
operating limits of the pump and motor).
Ensure that pumping liquid temperature, and motor housing temperature
are maintained within acceptable range as specified by Micropump
Certification of ATEX Conformity.