Technical description, Hs 8030 hd engine, Main winches – Liebherr HS 8030 HD Litronic User Manual
Page 5: Crawlers, Control, Noise emission, Hydraulic system, Swing, Boom luffing
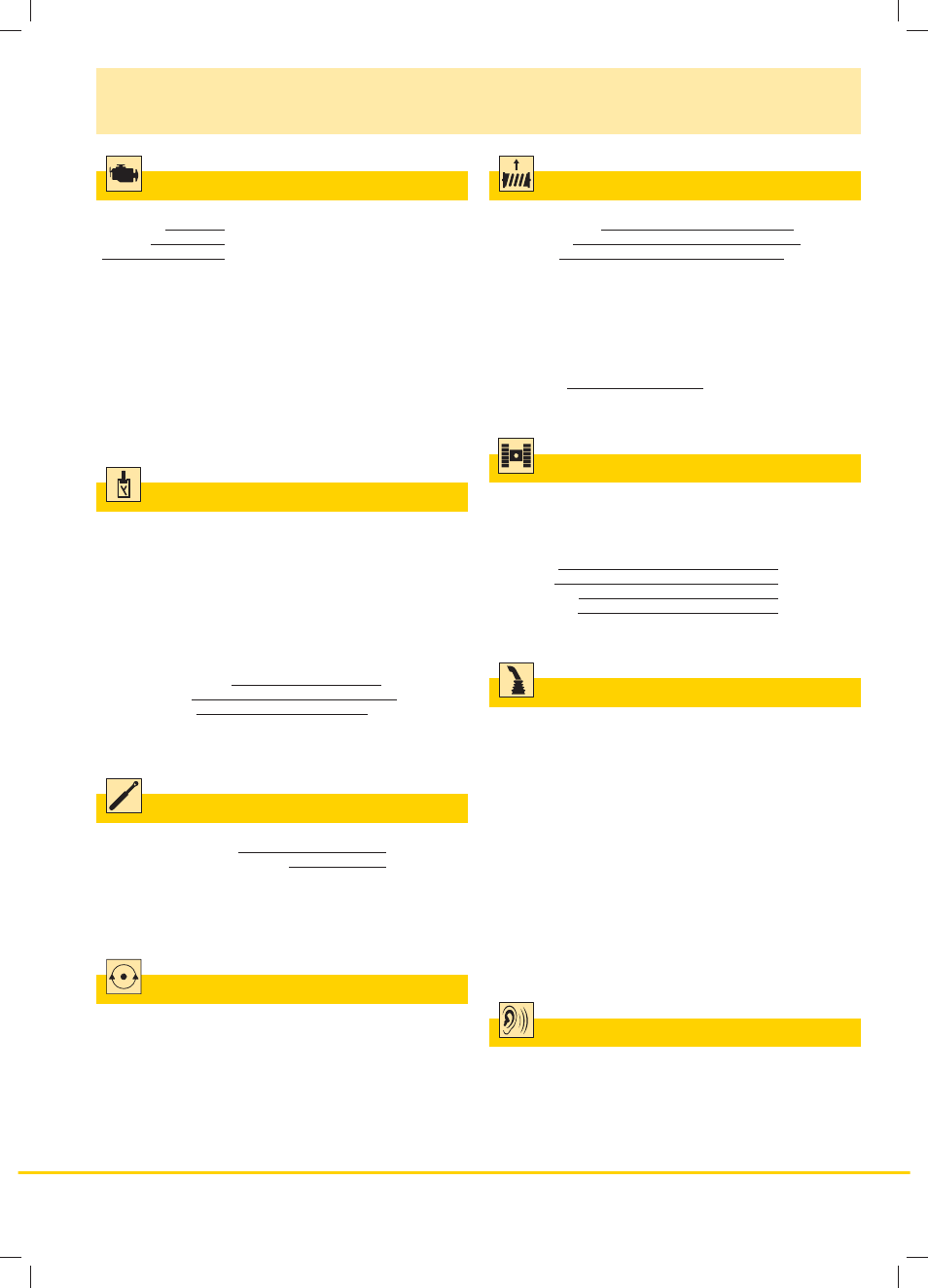
HS 8030 HD
5
Technical description
HS 8030 HD
Engine
Power rating according to ISO 9249, 180 kW (241 hp) at 2000 rpm
Engine type
Liebherr D 934 A7 SCR
Fuel tank
470 l capacity with continuous level
indicator and reserve warning
Engine complies with NRMM exhaust certification EPA/CARB Tier 4i
or 97/68 EC Stage III B.
ECO-Silent-Mode:
For work not requiring high engine power, the diesel engine can be
operated in the ECO-Silent-Mode (e.g. for inserting reinforcement
cages or for lift crane operation).
Due to the ECO-Silent-Mode which can be preselected by the operator
the engine runs with optimum fuel efficiency. This lowers consumption
and reduces noise emission.
Main winches
Winch options:
Line pull (nom. load)
100 kN
Rope diameter
24 mm
Rope speed
0-130 m/min
The winches are outstanding in their compact design and easy
assembly. Clutch and braking functions on the free-fall system are
provided by a compact designed, low wear and maintenance-free
multi–disc brake.
The drag and hoist winches use pressure controlled, variable flow
hydraulic motors. This system features sensors that automatically
adjust oil flow to provide max. winch speed depending on load.
Option:
Tagline winch
20 kN with free fall
Crawlers
The track width of the undercarriage is changed hydraulically.
Propulsion through axial piston motor, hydraulically released spring
loaded multi–disc brake, maintenance-free crawler tracks, hydraulic
chain tensioning device.
Drive speed
0 – 1.8 km/h
Track force
459 kN
3-web grousers
600 mm
Transport width
2500 mm
Control
The core of the Liebherr hydraulic crawler cranes is the Litronic control
system.
Developed and manufactured by Liebherr, this comprehensive system
encompasses all control and monitoring functions and is designed
to withstand extreme temperature changes and the rough heavy
duty tasks common in the construction industry. Complete machine
operating data, warnings and failure indications are clearly displayed in
the required language on the high resolution monitor in the operator’s
cab.
Documentation of operating data (PDE) enables optimum diagnosis as
well as early detection and prevention of more serious defects.
An electro-hydraulic proportional control allows several movements to
be performed simultaneously. This ensures that all categories of loads
can be positioned with utmost precision.
Options:
s¬ 0$%¬0ROCESS¬DATA¬RECORDING
s¬ '3-'023¬TELEMATICS¬MODULE
Noise emission
Noise emissions correspond with 2000/14/EC directive on noise
emission by equipment used outdoors.
Hydraulic system
A double axial displacement pump with integrated gearbox supplies
the open loop hydraulic system, allowing all functions to be operated
simultaneously. To minimize peak pressure an automatic working
pressure cut–off is integrated. This spares pumps and saves energy.
The hydraulic oil is cleaned through electronically controlled pressure
and return filters. Possible contamination is signalled in the cabin.
The use of synthetic environmentally friendly (biodegradable) oils is
possible.
Ready made hydraulic retrofit kits are available to customize
requirements e. g. powering casing oscillators, hydraulic grabs etc.
Pumps for working tools
2x 239 l/min
Oil tank capacity
500 l
Working pressure
max. 350 bar
Swing
Consists of roller bearing with internal teeth for lower tooth flank
pressure, fixed axial piston hydraulic motor, spring loaded and
hydraulically released multi–disc holding brake, planetary gearbox and
pinion.
Swing speed from 0 – 3.5 rpm continuously variable.
Boom luffing
Double-acting cylinder
Max. stroke (from 0°- 84°)
2050 mm
Boom luffing speed from 15° to 84°
23 sec.
Boom angle 0° = transport position
For boom assembly the boom foot can be lowered to -15.5°.