Impeller wear rings (optional), Gasket, Shaft – Goulds Pumps 3410 - IOM User Manual
Page 48: Impeller, Shaft sleeve, Bearings, Seals, General
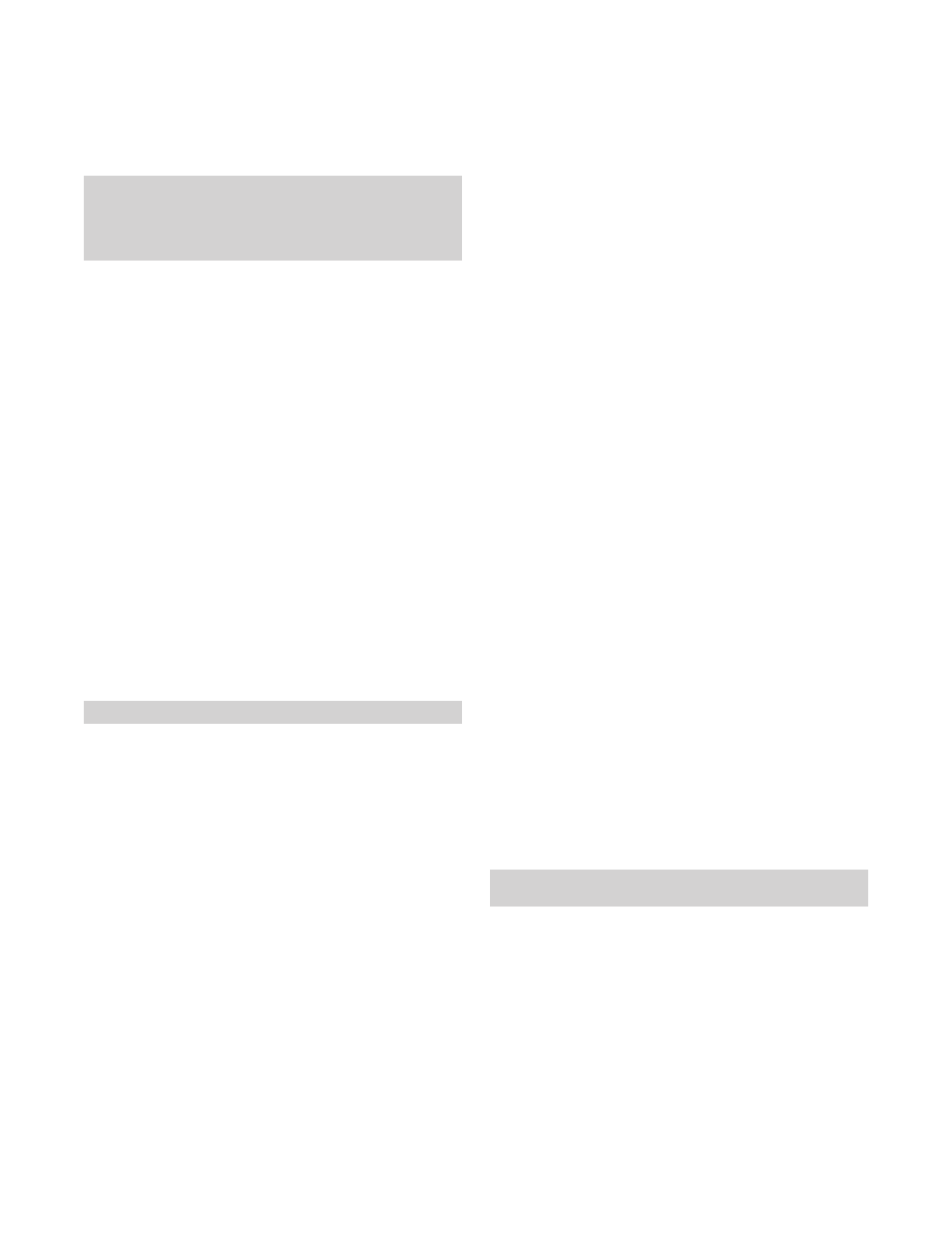
IMPELLER WEAR RINGS
(OPTIONAL)
If the unit has impeller wear rings (142) and it is necessary
to replace rings (Fig. 38), proceed as follows:
NOTE: If impeller was supplied without wear rings and
excessive wear requires, wear rings may be fitted in the
field. Fitting wear rings will require remachining of
impeller. Contact your local Goulds representative for
details.
1.
Remove old rings by removing three set screws (320)
and pulling ring (142) off impeller hub.
2.
Clean hub and press on new ring (142).
3.
Drill and tap three holes 120 degrees (1600 mils) apart
with 7/32 drill and 1/4" - 20NC tap on each ring. Use
5/16" x 1/4" cup point safety set screws. Tighten screws
and lightly upset threads. Do not use existing holes.
GASKET
Inspect parting gaskets (331). If torn or otherwise damaged,
cut a new gasket of 1/32" (.8 mm) non-asbestos (see
recommendations below). Use upper half casing as a
template. Strike the sheet with a soft face hammer. This will
cut the gasket against the edge of casing. The gasket must
cover entire surface of the parting flange, especially around
wear ring locks and stuffing box, or internal leakage from
high to low pressure zones in pump will occur.
The following gasket materials are recommended if pre-cut
replacement gaskets are not available:
Recommended Gasket Material
NOTE: Gasket thickness is 1/32".
• JM - 961
• Durable - Durlon
• Garlock Blue Guard 3000
• Armstrong - N8090
• Rodgers - D7031
• Or equivalent.
SHAFT
Check shaft (122) for runout to see that it is not bent.
Straighten if required. Bearing seats must be in perfect
condition. Replace shaft if necessary. Check keyways for
burrs or foreign matter.
IMPELLER
Check impeller (101) and replace if there is:
• Excessive erosion, especially on inlet vanes.
• Gasket mating surface deterioration to point that
gasket (428) cannot seal properly.
• Excessive erosion of surfaces. If impeller diameter has
to be cut, it should be dynamically balanced.
Imbalance can be corrected by grinding outside of
shrouds near periphery.
SHAFT SLEEVE
The sleeve (126) surface in the stuffing box area must be
smooth and free of grooves. If grooved, replace. O-ring
groove in end of sleeve nut must be in good condition.
Impeller end of sleeve must be in good condition to ensure
gasket (428) will seal properly. The original diametric
clearance between shaft sleeve and the stuffing box bushing
is 0.030 - 0.034" (.76 - .86 mm). If this clearance has
increased to more than 0.050 - 0.060" (1.27 - 1.5 mm) the
sleeve, and at times, the stuffing box bushing, should be
replaced.
BEARINGS
Ball bearings (112 and 168) can be checked for visible wear
by slowly turning races and watching for pits or worn areas
on balls or raceways. Bearings can also be inspected by
holding inner race and spinning outer race. If any rasping
noises are emitted or bearing catches or binds, it should be
replaced. If any wear on race is apparent, replacement is
suggested.
Replace ball bearings if worn, loose, rough, or noisy when
rotated.
SEALS
Check seals (332 and 333) for wear, cracks, cuts,
deformities, and signs of excessive leakage. Check thrust
bearing end cover (109A) for signs of leakage and damage.
Check grease fittings (113) or oil breathers (113A) (oil
option) for serviceability, replace as required.
GENERAL
All parts should be cleaned before assembly. This is
especially important at O-ring grooves, mating surfaces and
bearing areas. Threads on dowels, screws, nuts, and studs
should be in good condition. Ensure anti-rotation pins
(445A) are firmly pressed into wear rings (103).
NOTE: See preventive Maintenance for specific
instruction for bearing cleaning.
46
3410 IOM 1/2010