Goulds Pumps 3410 - IOM User Manual
Page 32
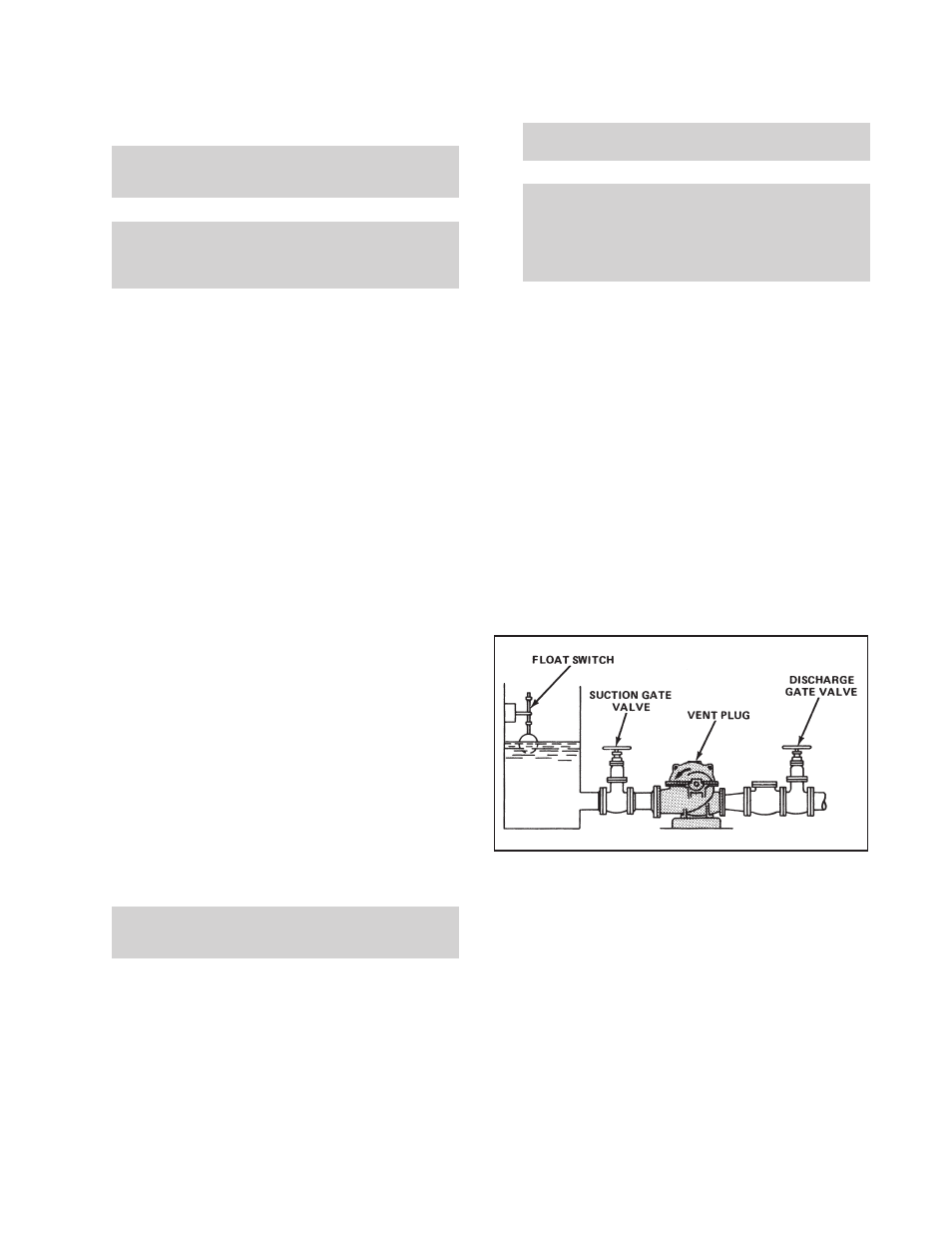
MECHANICAL SEAL FLUSHING/
COOLING PIPING
!
The mechanical seal must have an appropriate seal
flush system. Failure to do so will result in excess
heat generation and seal failure.
!
Sealing systems that are not self purging or self
venting, such as plan 23, require manual venting
prior to operation. Failure to do so will result in
excess heat generation and seal failure.
Mechanical Seals
For satisfactory operation, there must be a liquid film
between seal faces to lubricate them. If liquid flashes to
vapor, faces will run dry and be damaged. In general, this
requires that liquid be cooled so that vapor pressure is well
below stuffing box pressure. Doubtful cases should be
referred to Goulds for a recommendation. Refer to seal
manufacturer’s drawing for location of taps. Some methods
which may be used to flush/cool the seal are:
• Cool Liquid Flushing – External Source. A clean,
cool compatible liquid is injected from an outside
source directly into seal gland. Flushing liquid must
be at a pressure 5 to 15 PSI greater than pressure in
stuffing box. One-half to two GPM (2-8 LPM)
should be injected. A control valve and rotometer can
be placed in the inlet line to permit accurate
regulation.
• Cool Liquid Flushing – Product Cooling. In this
arrangement, pumped liquid is piped from the pump
casing, and is cooled in an external heat exchanger,
when required, then injected into seal gland. A control
valve and rotometer can be placed in the inlet line to
permit accurate regulation.
• Other piping plans are available.
CONNECTION OF DRAIN PIPING
Tapped openings around stuffing box for draining leakage
are optional. Check assembly dimension print for size and
location.
Check rotor for free turning.
!
Rotate shaft by hand to ensure it rotates smoothly
and there is no rubbing which could lead to excess
heat generation and or sparks.
PRIMING THE PUMP
!
Pumps must be fully primed at all times during
operation.
!
A build up of gases within the pump, sealing system
and or process piping system may result in an
explosive environment within the pump or process
piping system. Ensure process piping system, pump
and sealing system are properly vented prior to
operation.
General
The pump must always be fully primed and suction pipe
full of liquid before pump is started.
If pump is run dry, rotating parts within pump may seize to
stationary parts since they depend upon liquid being
pumped for lubrication.
Several different methods of priming can be used,
depending upon type of installation and service involved.
Supply Above Pump
When pump is installed as shown in Fig. 27, pump will
prime itself. Open gate valve on suction and close
discharge gate valve. Remove vent plug until all air is
expelled and water flows through openings. Close air vent
valves, start pump, and open discharge gate valve. Pump
will continue to be primed for any future starting.
This method is simplest and, particularly for automatic
operation, safest. A float switch in suction reservoir can be
arranged to stop pump, should there be failure of liquid
supply.
Priming with Foot Valve
With pump installed on suction lift, with foot valve at end
of suction line, priming can be done any of following three
ways:
1.
Outside Supply (Fig. 28). Close discharge gate valve,
remove vent plug, and open valve in priming supply
line until all air is expelled and water issues from vent
openings. Close air vents, close valve in priming
supply line, and start pump; then open discharge gate
valve.
30
3410 IOM 1/2010
Fig. 27