Theory of operation – Ashcroft 4480 - Pneumatic Transmitter User Manual
Page 6
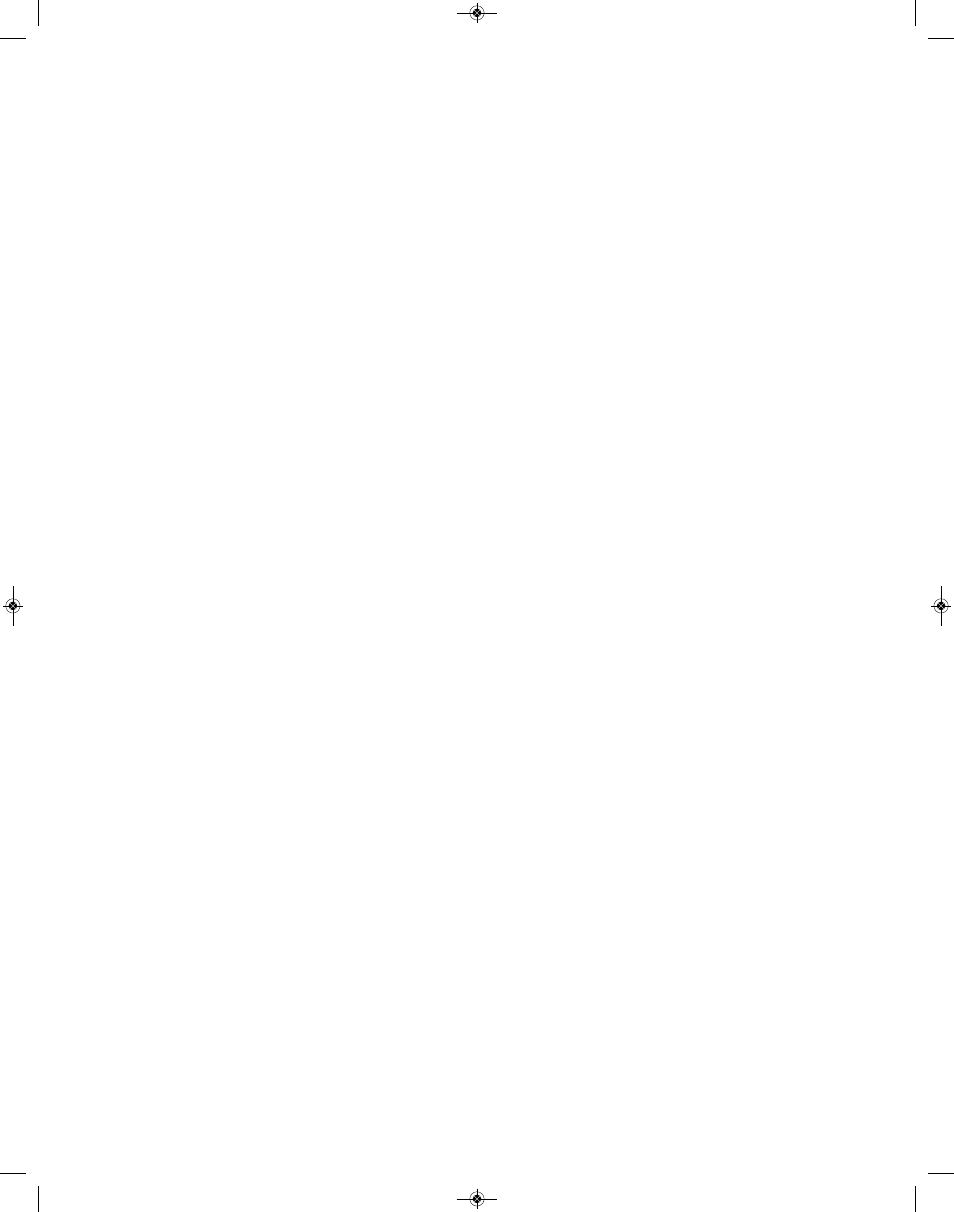
6
Input Element
The input element of the pressure transmitter is a pressure-
sensitive bourdon tube. As mounted in a transmitter, increasing
pressure raises the free end of the bourdon tube, while
decreasing pressure lowers it. The height of the free end with
respect to any fixed reference point is, therefore, a direct
measure of internal pressure.
In the pressure transmitter, a vane assembly is secured to the
free end of the input element. This assembly comprises a thin
metal vane mounted vertically on a bracket provided with a
means of vertical adjustment. For any applied pressure, the
lower edge of this vane establishes a height which is an accu-
rate measure of applied pressure.
Flexure and Nozzle Assembly
The flexure is a cantilevered leaf spring one end of which is
free to move vertically to follow the lower edge of the vane.
The free end rests on and is actuated by the feedback bellows.
A disc clamped by two jam nuts on a threaded rod mounted
over the leaf spring contacts the spring to establish the range
of operation. This disc is in contact with the leaf spring at all
times. By moving the disc along the length of the leaf spring,
the deflection of the free end of the spring for a given applied
air pressure can be varied.
Two opposed nozzles having a short gap between them are
mounted on the free end of the leaf spring by means of a tem-
perature-compensating, bi-metallic strip. The opposed nozzles,
actuated by the feedback system of leaf spring and bellows,
are moved vertically on opposite sides of the vane, as shown
in Figure 16. Supply pressure applied to one nozzle crosses
the gap as a jet of air to the other nozzle. As the vane cuts
across this jet of air, the pressure developed at the collector
nozzle is altered to a degree proportionate to the extent of
interference by the edge of the vane.
An increase in process pressure will cause the vane to rise,
allowing pressure at the collector nozzle to increase as the
vane moves from the jet of air. This increase in pressure is
transmitted to a pneumatic relay which acts to increase pres-
sure in the feedback bellows, raising the leaf spring. As the
leaf spring rises, the lower edge of the vane cuts the jet of air
to establish a new pressure null in the feedback bellows. This
pressure will be directly proportionate to the new position of
the vane.
If process pressure decreases, the vane will be lowered into
the jet of air, causing collector nozzle pressure to decrease.
This is translated by the pneumatic relay into a decrease in
pressure in the feedback bellows. The leaf spring moves down,
moving the nozzles lower with respect to the vane, until a new
null is established. The air pressure in the feedback bellows is
the transmitted signal.
Pneumatic Relay
As described above, the opposed nozzles and vane act as an
error detector. Any movement of the vane with respect to the
opposed nozzles will be reflected as a change in pressure at
the collector nozzle. As shown in Figure 7, this pressure is
applied to chamber A in the pneumatic relay, where it acts
against diaphragm D2. Supply pressure is admitted to cham-
ber C, where it acts against diaphragm D1, by the opening of
the pilot valve.
If an imbalance exists between the forces applied to
diaphragms D1 and D2, the diaphragm assembly will move
toward the chamber exerting the lower force. Since diaphragm
D2 has approximately four times the area of diaphragm D1,
balance is achieved when pressure in chamber C is four times
that in chamber A. If pressure in chamber A increases due to
an increase in pressure at the collector nozzle, the diaphragm
assembly will drive the pilot valve open, admitting supply pres-
sure to chamber C until balance is again established. If pres-
sure in chamber A decreases, the diaphragm assembly will be
driven from the ball valve end of the pilot valve, allowing pres-
sure from chamber C to exhaust through chamber B to atmos-
phere until balance is again established.
As shown in Figure 7, the pressure established in chamber C
is applied to the feedback bellows and the transmitted air line.
Any error pressure established at the collector nozzle is, there-
fore, amplified and relayed as a corresponding change of pres-
sure in the feedback bellows, causing the nozzle assembly to
follow vane movement. This pressure is therefore an accurate
measure of input process pressure, and maybe used for
remote indication or to actuate pneumatic control devices.
THEORY OF OPERATION
I&M008-10061-1-01 250-1969-C_I&M008-10061-1/01 250-1969-C 12/20/13 9:09 AM Page 6