Part 1 installation – Midco Unipower MPG Series User Manual
Page 4
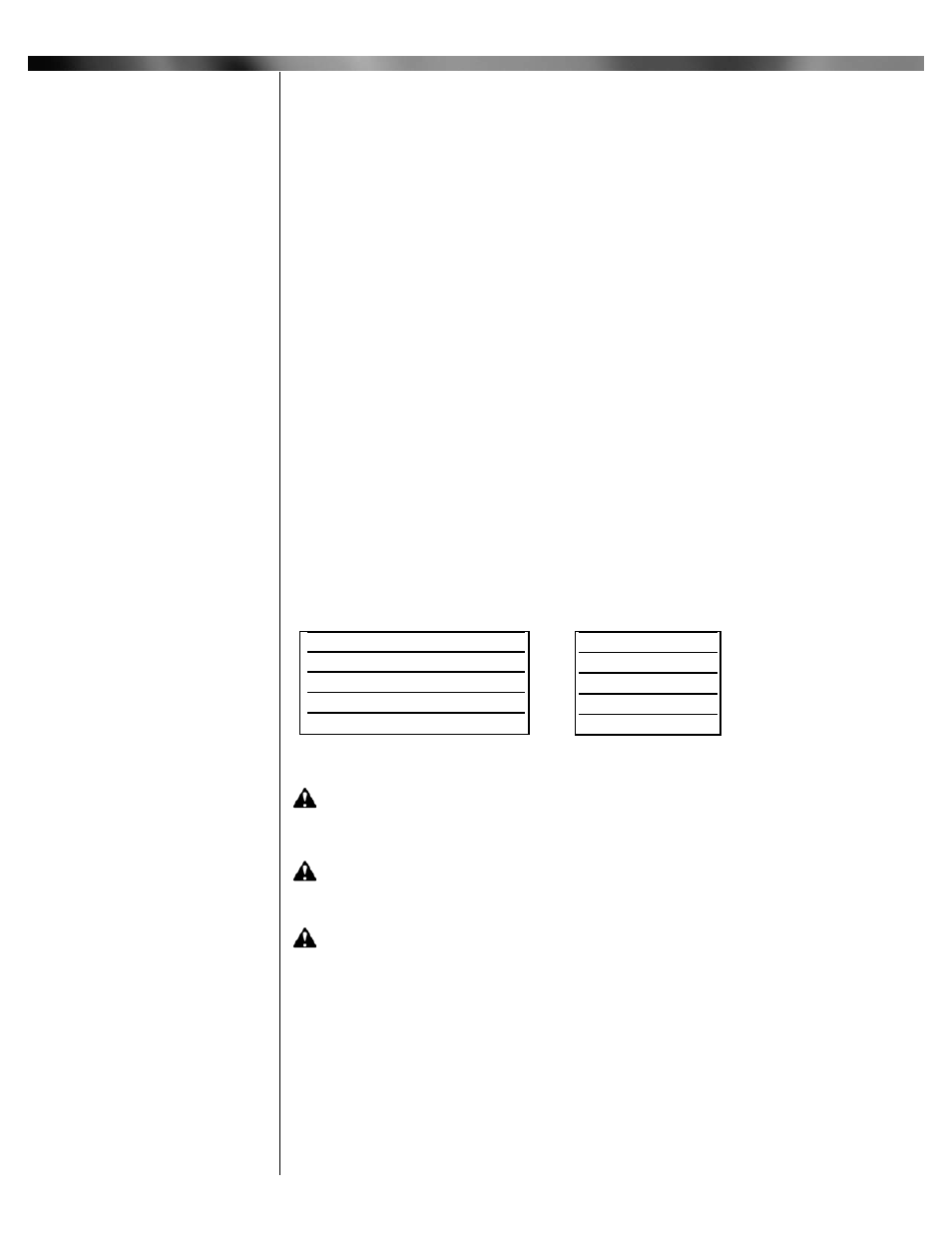
The MPG gas burner is designed for "in-shot" firing. It can be fired into the ash pit of a boiler
designed for solid fuels, or it can be fired into the primary heat exchanger of a boiler designed for
liquid or gaseous fuels. The ash pit installation requires a refractory lining.
The combustion chamber serves to contain and promote combustion and to protect non-heat
exchange surfaces from direct flame contact. Built-up combustion chambers should be made of
2600° insulating firebrick. As an alternative, a monolithic floor can be cast in place, using a high
temperature (2400°) light weight insulating refractory. Check with your supplier to determine the
thickness which will yield equivalent insulating qualities.
The combustion chamber sizes given in Table 3 are based on the maximum rated burner
capacity. If the input is to be permanently set at a reduced rate the combustion chamber floor
area can be reduced proportionately to the proposed input, with the length as closely
proportioned to twice the width as possible.
Where recommended size combustion chambers (225,000 BTU/sq. ft.) can be
accommodated, the type of construction shown in Figure 1 should be used. If lack of space
prohibits use of this construction, higher BTU values per square foot can be allowed for by using
the constructions shown in Figures 2 and 3.
The back wall of the combustion chamber should be carried 2 or 3 courses higher and
overhung to deflect the flames from direct impingement on the rear heat exchanger surface. Hard
firebrick should be used to prevent erosion of the brick by high velocity gases.
The burner is equipped with a mounting flange for direct attachment to the boiler front. The
burner nozzle must not extend into the combustion chamber. It should be sealed into the opening
as shown in Figures 1 - 4.
The refractory lined combustion chamber can be omitted in "Scotch Marine" and "Steam
Generator" boilers or warm air furnaces that do not include ash pits. The burner is fired directly
into the heat exchanger, requiring no refractory unless the combustion chamber is so short that
flame would impinge excessively on the rear heat exchanger wall (this is particularly important in
a warm air furnace). Refractory protection is recommended if the length of the primary chamber
is less than 20% larger than the length given in Table 3. In any case, the burner entry wall must
be refractory lined if it is not a heat exchanger surface.
___________________________
WARNING: The chimney shall be inspected for unsafe conditions such as
deteriorated masonry and excessive soot or other blockage or potential blockage.
Installation must conform with local codes or in the absence of local codes with NFPA,
ANSI Z223.1-latest edition.
WARNING: No movable vent connector damper is permitted on any power gas burner
installation. The chimney should be inspected for unsafe conditions such as deteriorated
masonry and excessive soot or other blockage or potential blockage. Check your local
authorities for regulations covering barometric draft regulators on gas equipment.
WARNING: The vent connector shall not be connected to a chimney already venting
solid fuel burning equipment, an incinerator or an open fire place.
The MPG burner does not depend on chimney draft. Combustion air is supplied by the forced
air blower, which is sufficient to supply adequate air for any normal application. This reduces the
function of the chimney to remove of flue products from the boiler. A chimney height of 15' above
the boiler flue outlet will generally prove ample if the recommended or larger vent connector and
chimney diameters are used. The chimney must of course, extend several feet over the roof of
the building, or adjacent buildings. Vent connector material should be 24 gauge or heavier steel,
galvanized to resist corrosion. The horizontal run of vent connector should be pitched upward
from the appliance flue outlet at least 1/4" to the foot. Avoid excess elbows or other constructional
features that would create excessive resistance to flow of flue products. Fasten joints with sheet
metal screws to prevent sagging. The vent connector should be maintained at least 6" from
combustible building materials; more if it is uninsulated. Where it passes through partitions
constructed of combustible materials a ventilated thimble should be used. Refer to your local
building codes. The vent connector should be firmly cemented into the chimney but must not
4
Part 1 Installation
IV
Chimney, Vent
Connector and
Draft Control
Gas Input,
MBH/Hr Width/Height " Length "
500
12"
26"
1000
15"
34"
1500
18"
42"
2000
21"
50"
2500
24"
58"
Table 3: Recommended Combustion
Chamber Minimum Required Dimensions
Max Input, Flue Pipe
MBH/Hr Diameter "
700
9"
950
10"
1400
12"
1950
14"
2500
16"
Table 4: Recommended Size of Flue
Pipe and Chimney - Based on Maximum
Height of 15’ and Lateral Run of 15’
OTE: For actual
vent diameter
information refer to
the ational Fuel
Gas Code Handbook
- Latest Edition
III
Combustion
Chamber
Continued