Storage, transport, preparation, installation – NORD Drivesystems B1050 User Manual
Page 11
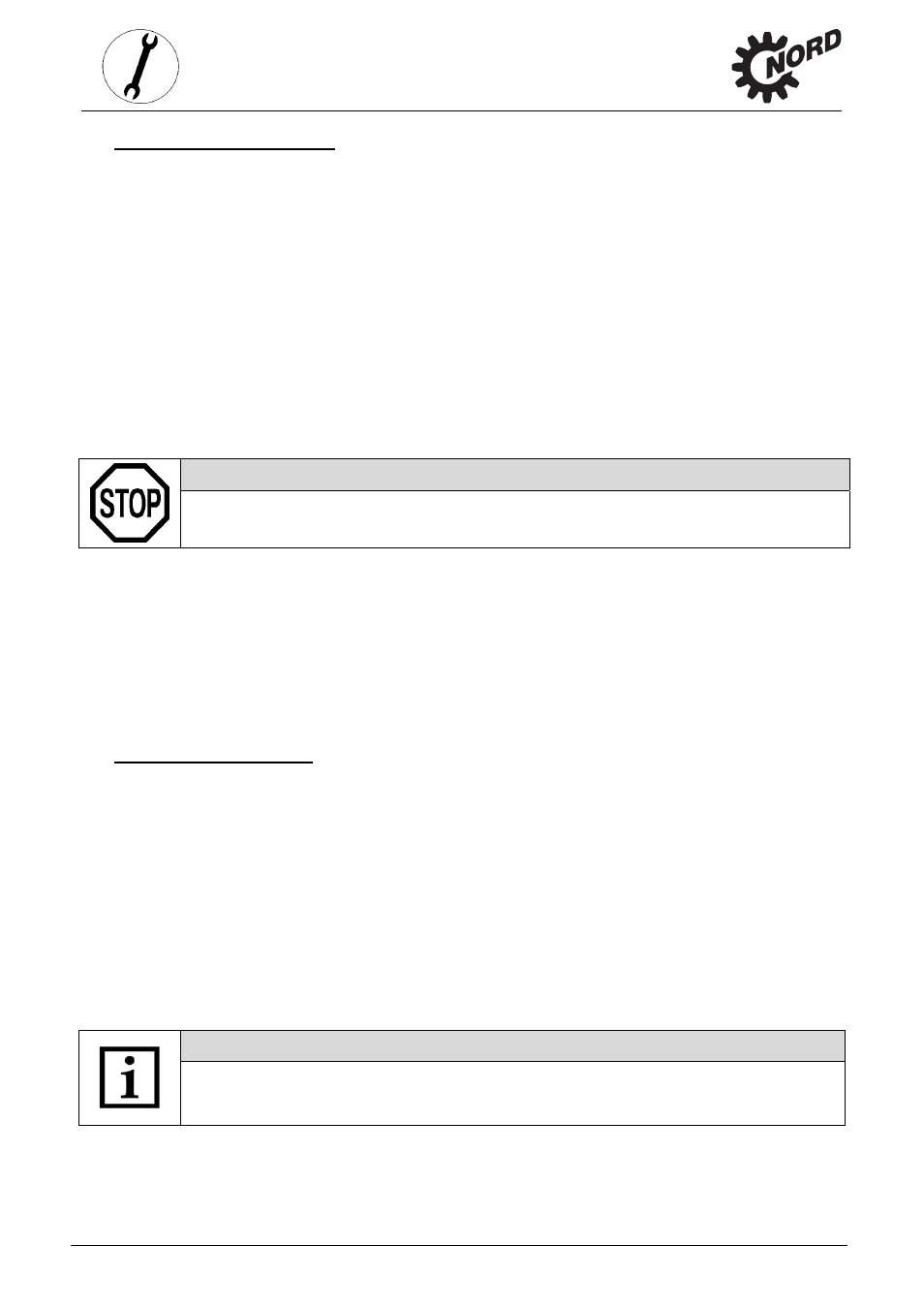
3. Storage, Transport,
Preparation, Installation
-12- B1050-GB-0213
www.nord.com
3.4 Preparing for installation
The drive unit must be inspected and may only be installed if no damage is apparent. In
particular the radial seals and the sealing caps must be inspected for damage.
All bare metal surfaces and shafts of the gear unit are protected against corrosion with oil,
grease or corrosion protection agents before shipping.
Thoroughly remove all oil, grease or corrosion protection agents and any dirt from the shafts and
flange surfaces before assembly.
In applications where an incorrect rotational direction may result in damage or potential risk, the
correct rotational direction of the drive shaft is to be established by test running the drive when
uncoupled and guaranteeing such for subsequent operation.
Gears with integrated return stops are marked with arrows on the driven/driving sides. The
arrows point in the rotation direction of the gear unit. It must be ensured, when connecting the
motor and during motor control, that the gear unit can only operate in the rotation direction, e.g.
by means of a rotary field test.
Attention!
With gear units with an integrated back stop, switching the drive motor to the blocked rotation
direction, i.e. incorrect rotation direction, can lead to gear damage.
Ensure that no aggressive or corrosive substances are present in the area surrounding the
installation site or are subsequently expected during operation, which attack metal, lubricants or
elastomers. In case of doubt, please contact Getriebebau NORD and take the recommended
action.
Oil expansion tanks (Option OA) must be fitted in accordance with the attached works standard
WN 0-530 04.
Oil expansion tanks (Option OA) must be fitted in accordance with the attached works standard
WN 0-521 30.
3.5 Installing the gear unit
The base or flange to which the gear unit is fitted should be vibration-free, torsionally rigid and
flat. The smoothness of the mating surface on the base or flange must be according to tolerance
class K of DIN ISO 2768-2. All contamination to the bolting surfaces of gear unit and base or
flange must be thoroughly removed.
The base must be designed according to the weight and torque, taking into account the forces
acting on the gear unit. Bases which are insufficiently rigid may lead to radial and axial
displacement during operation, which is not measurable when the unit is stopped.
When attaching the gear unit to a concrete base using masonry bolts or base blocks, appropriate
recesses must be provided in the base. Tensioning bars must be cast into the concrete base in
their aligned state.
The gear unit must be precisely aligned with the drive shaft of the machine in order to prevent
additional forces from being imposed on the gear unit due to distortion.
Note!
The service life of shafts, bearings and couplings depends on the precision of alignment of the
shaft. Therefore, zero deviation should always be aimed for in alignment. For this, e.g. the
requirements for the coupling should be obtained from the special operating instructions.
The tolerances of the shaft ends and the flange connections should be obtained from the
dimension sheet.