Dwyer 275 User Manual
Page 7
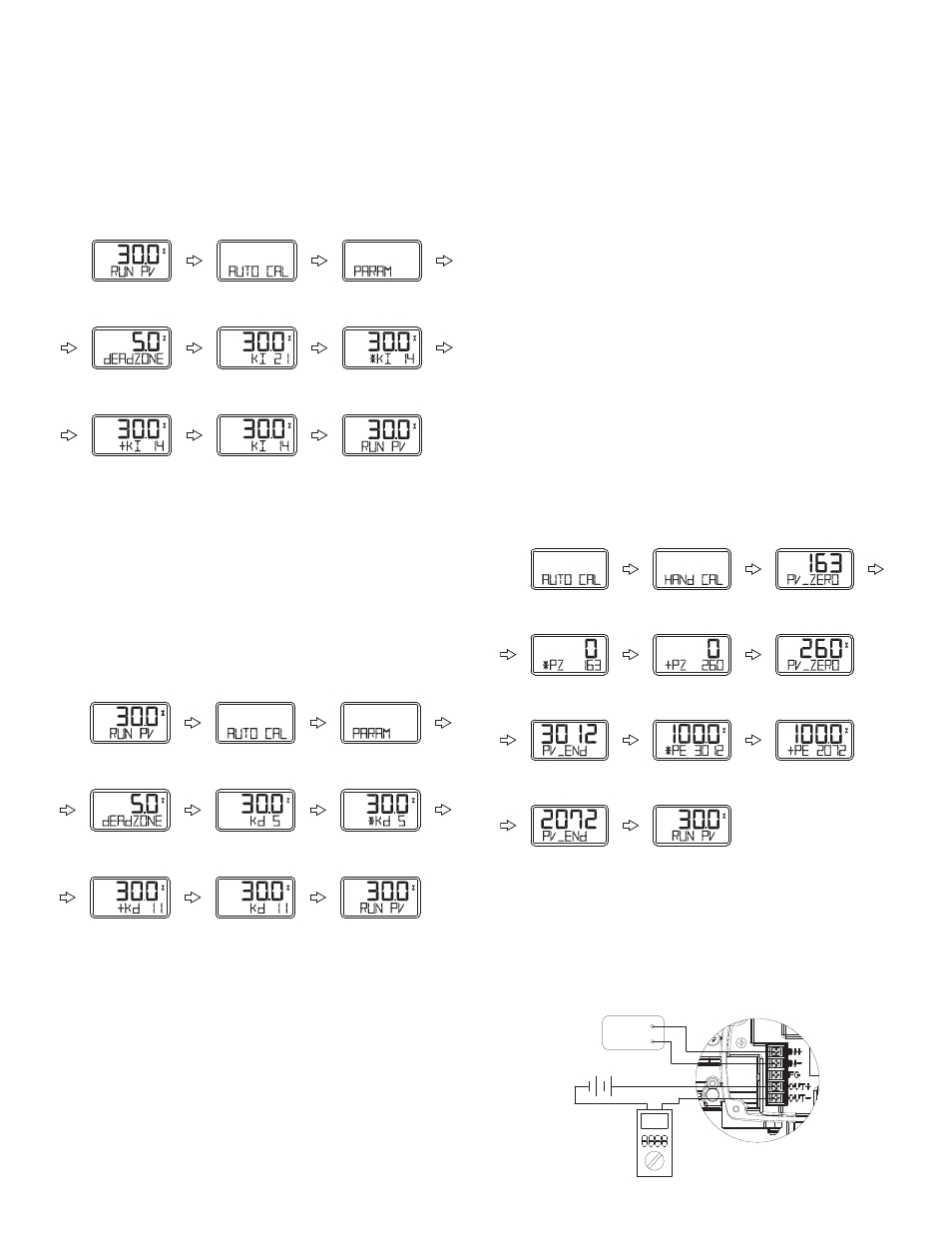
KI
1-3. Adjustment method and procedure same as dEAdZONE.
4. Push
5. Push
6. Adjust KI value with
immediately without additional operation. Users can easily check its
adjustment by changing the current input signal to the positioner.
Optimum control value is found by adjusting values during valve
operation. Push
appears on LCD.
7. Push
8. Push
Kd
1-3. Adjustment method and procedure same as dEAdZONE.
4. Push
displayed.
5. Push
6. Adjust Kd value with
immediately without additional operation. Users can easily check its
adjustment by changing the current input signal to the positioner.
Optimum control value is found by adjusting values during valve
operation. Push
appears on LCD.
7. Push
8. Push
HAND CAL
When auto calibration is started, Series 275 positioner set zero points
and end points based on full stroke.
Hand Calibration Types
PV_ZERO: Edit mode to change the zero point of valve.
PV_END : Edit mode to change the end point of valve.
TR_ZERO : Edit mode to change the zero point of transmitter.
TR_END: Edit mode to change the end point of transmitter.
Adjustment of valve zero point (1 to 5) and end point (6 to 10).
1. Push
mode is displayed. Push
mode is displayed.
2. Push
started.
3. Push
mode it is available to change valve zero point, and the valve stem
moves automatically to the current zero point. On LCD, valve stroke
is displayed as 0%. +PZ message that indicates edit mode of zero
point and inner value showing current zero point position is also
displayed.
4. Adjust valve stem by pushing
has arrived at the desirable zero point, save it with
message appears on LCD.
5. Push
(Push
6. In order to change valve end point, push
mode and PV_END mode begins.
7. Push
this mode it is available to change valve end point, and the valve
stem moves automatically to current end point. On LCD, the valve
stroke is displayed as 100%. *PE message indicating edit mode of
end point and inner value of end point is also displayed.
8. Adjust valve stem with using
arrives at the desirable end point, save it with
message appears on LCD.
9. Push
10. Push
(Push
Adjustment of zero point (1 to 4), end point (5 to 9) of transmitter.
If valve zero point and end point are changed, transmitter is also
changed automatically. Usually there is no need for the transmitter zero
point and end point to be adjusted by users, but if transmitter output
signal is unstable, transmitter zero point and end point should be
adjusted. The ammeter showing feedback signal is necessary and the
connection should be done as shown.
page 7
Feed back signal
(12 ~ 30V)
4 ~ 20 mA
INPUT
(1) Push
seconds.
(2) Push
(3) Push
(4) Push
(5) Push
(6) Push
after adjustment with
(7) Push
(8) Push
RUN MODE.
(1) Push
seconds.
(2) Push
(3) Push
(4) Push
three times.
(5) Push
(6) Push
after adjustment with
(7) Push
(8) Push
RUN MODE.
(1) Push
three times.
(2) Push
(3) Push
(4) Push
after adjustment with
(5) Push
(6) Push
(7) Push
(8) Push
adjustment with
(9) Push
(10) Push
RUN MODE.