Dwyer TE User Manual
Dwyer instruments, inc, Series te orifice plate flowmeter, Bulletin f-te
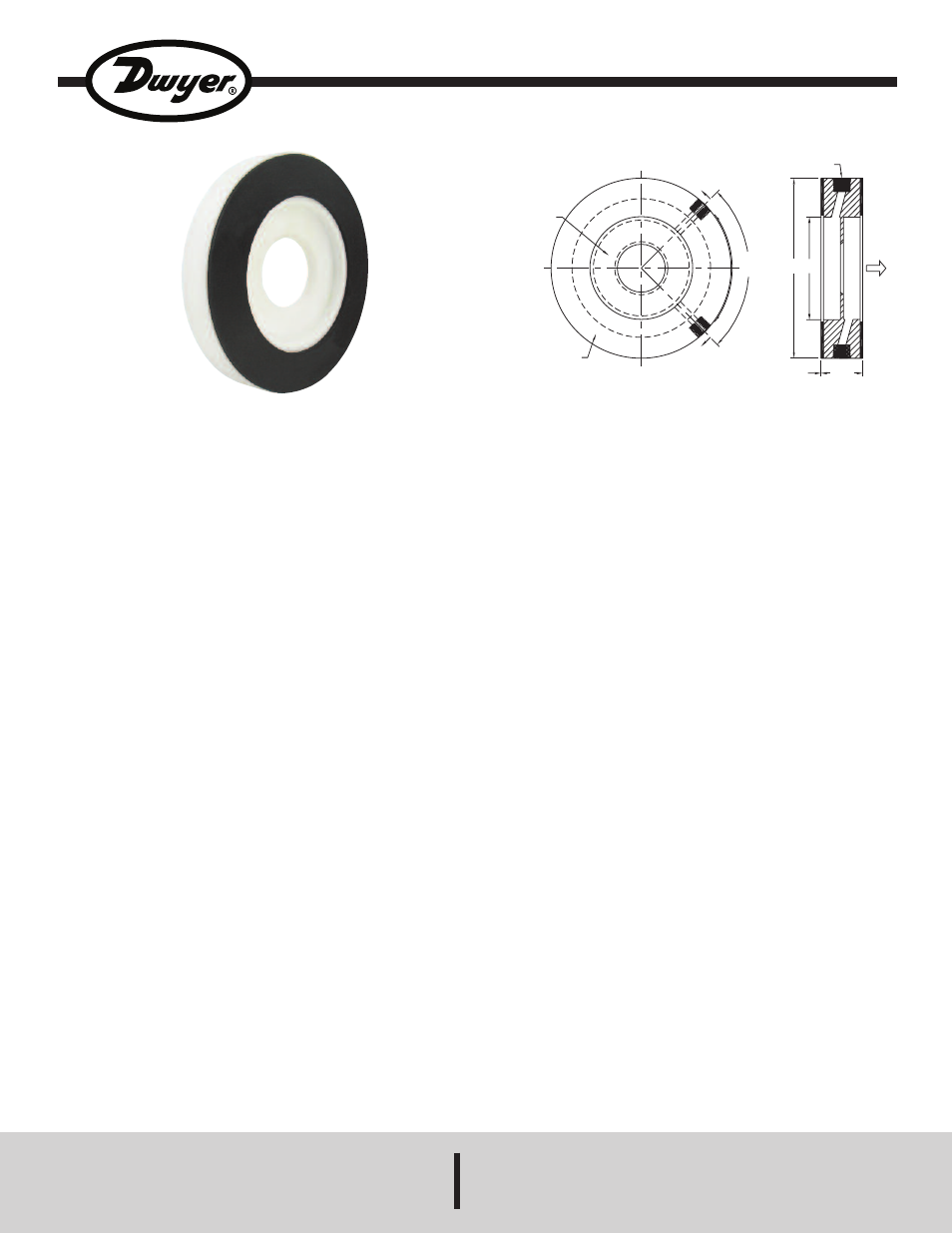
Series Te orifice plate flowmeter
Specifications - Installation and operating Instructions
Bulletin f-Te
The Series Te orifice plate flowmeter offers one-piece PTFE construction
similar to the OP and PE Series orifice plates, which incorporate a unique holder
or carrier ring containing metering taps and integral gaskets. Available for line sizes
from 1/2˝ to 24˝, the Series TE orifice plate can be used with gases, liquids,
corrosive, and high temperature fluids. The Series TE can be easily installed by
slipping the unit between standard flanges (orifice flanges are not required). The
Series TE was designed for use anywhere there is an application for a conventional
flow orifice plate. It can also be used in place of other primary differential producers
for efficiency and cost effectiveness.
accURacY
The Series TE Flowmeter utilizes the corner tap proportions as defined in ISO
5167. While this code may not be referred to as International Standard until
accepted by the ISO Council, the ASME Fluid Meters Research Committee has
suggested that the dimensionless coefficient equation developed by the
International Standards Organization (ISO) and presented in ISO 5167 is
significantly better for the broad spectrum of flow measurement applications
throughout process industries.
The coefficient values used in the Series TE Flowmeter bore calculations represent
the same confidence level assigned to the flange and radius taps widely accepted
in fluid flow measurement.
The accuracy assigned to the coefficient values is ±0.6% full scale for d/D (Beta)
values 0.2 to 0.6 and ±0.7% for Beta values 0.7 to 0.75 (i.e. ß of 0.7 would have
an uncertainty value of ±0.7% full scale).
Accuracy of the differential signal produced by the Series TE Flowmeter equals
that of a properly manufactured and installed flange or radius tap orifice meter.
MoUnTInG
The orifice metering primary shall be suitable for installation between standard
ANSI 125#/150# PVC or steel flanges mounted on HDPE, PVC or steel pipe. The
unit shall be "self centering" within the bolt circle of the flanges. No alignment of the
orifice shall be necessary. Drilling and or tapping of the main or flanges will not be
allowed or required. The overall laying length shall be 1.25˝ including pre-attached
ring type 1/8˝ thick Buna "N" Gaskets. Flange bolts should be 1.25˝ longer than
standard flange bolts.
pipe Requirements: Upstream and downstream pipe requirements are contingent
upon two factors: (a) Beta Ratio-ratio of the orifice bore to the pipe ID (d/D); (b) The
type of fitting or disturbance upstream of the Series TE Flowmeter. For most
applications, 10 pipe dia. upstream & 5 dia. downstream are sufficient. (5 pipe dia.
up and 2 dia. down are acceptable for non-critical applications.)
DWYeR InSTRUMenTS, Inc.
phone: 219/879-8000
www.dwyer-inst.com
p.o. BoX 373 • MIcHIGan cITY, InDIana 46360, U.S.a.
fax: 219/872-9057
e-mail: [email protected]
SpecIfIcaTIonS
Service: Air and compatible gases, corrosives, high temperature fluids, and liquids.
Wetted Material: Monolithic (single piece) constructed entirely of PTFE, Buna-N
gaskets.
accuracy: ±0.6% full scale flow (Beta = .2-.6) ±0.7% for Beta greater than .6.
Temperature: -40 to 200°F (-40 to 93.3°C).
pressure: 150 psi max (10 bar).
Head Loss: 1-Beta ratio
2
eg: 1 - 0.7
2
= 1 - 0.49 = 51% of the d.p.
Line Sizes: 1/2˝ to 24˝, special and non-standard sizes available.
process connections: 1/4˝ female NPT.
Installation: Standard flange 125#/150# rating.
pipe Requirements: General requirements 10 diameter upstream and 5 diameter
downstream.
Weight: Varies with line size. See chart.
ORIFICE PLATE
1/4 [6.35]
THICK TYPICAL
A
4-1/2
[114.3]
FLOW
1/4 NPT
PRESSURE FITTING
INCLUDES RING GASKET
ADHERED TO FACES
1-1/4
[31.75]
A
BODY
(CARRIER RING)
CL
OD ID
LOW
PRESSURE
CL
Installation Tips: (a) If possible, do not install a valve upstream if it is going to be
throttled. Install on the downstream a minimum of 6 diameters from the Series TE
Orifice Plate. (b) The use of straightening vanes is not necessary for most
applications.
Installation: (a) Insert bolts through bottom half of the flange bolt circle. (b) Slide
flowmeter between flanges (make sure arrow on flowmeter faces in the direction of
flow). (c) Make sure pressure connections are properly positioned. For horizontal
air or gas lines, install with the connections on or under the horizontal center line.
They should also be correctly oriented so as to not be blocked by bolts when
remainder of bolts are inserted. (d) Add rest of bolts and nuts leaving all bolts loose
so the flowmeter is free to move. (e) If necessary, the flowmeter can be centered
using a steel ruler to measure the total side to side movement and set flowmeter
at half way point all around. (f) Lubricate & tighten bolts diametrically alternating to
recommend flange torque. (g) Check to insure the flowmeter is installed with the
arrow facing in the same direction as flow.