Dwyer HF User Manual
Page 4
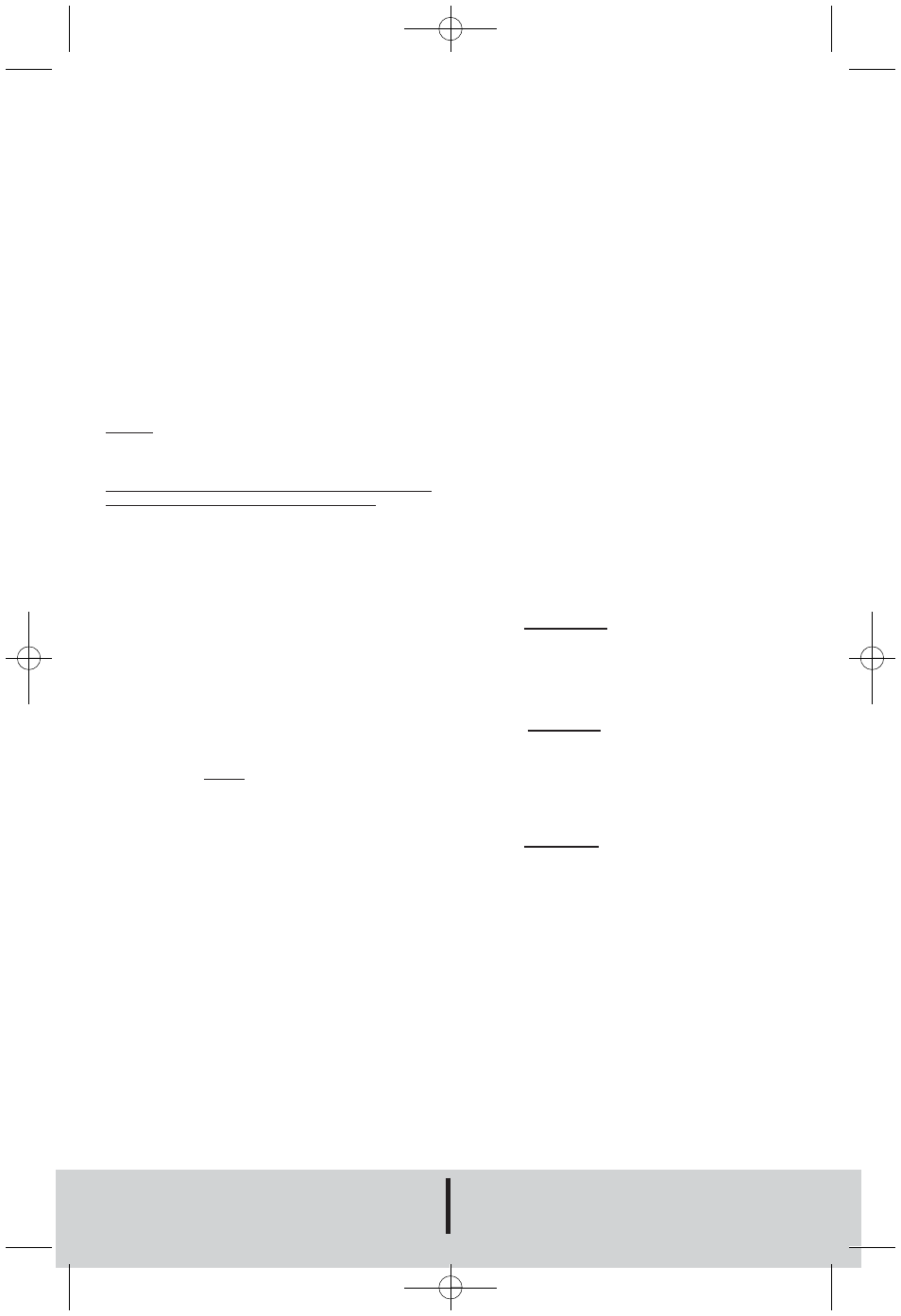
DWYER INSTRUMENTS, INC.
Phone: 219/879-8000 www.dwyer-inst.com
P.O. BOX 373 • MICHIGAN CITY, IN 46361,U.S.A. Fax: 219/872-9057 e-mail: [email protected]
©Copyright 2009 Dwyer Instruments, Inc Printed in U.S.A. 7/09
FR# 50-440843-00 Rev. 3
added, mainly have self-generated contamination.
In this case, proper filtration can help prevent fluid
component malfunction.
COMPRESSIBILITY OF AIR AND GASES
Air and gases are extremely compressible. Gas
density increases as pressure increases. In most
cases, correction factors should be used to obtain
accurate readings. See correction factors below.
CALIBRATION
All standard Dwyer Instruments,Inc. air flow monitors
are calibrated for air with a specific gravity of 1.0 at
100 psig and 70°F (6.89 bar and 21.1°C). Monitors
are calibrated in SCFM, Standard Cubic Feet per
Minute. A standard cubic foot or air is defined as a
cubic foot of air at 70°F at atmospheric pressure,
14.7 PSI at sea level. Since most industrial
pneumatic systems typically operate at 90-100 PSI,
standard Dwyer Instruments, Inc. Monitors are
calibrated for inlet conditions of 100 PSI at 70°F.
When operating the monitor at other pressures or
temperatures, a correction factor should be used to
maintain the original design accuracy of the monitor.
When inlet pressure of the monitor is at or near 100
PSI, the air flow can be read directly from the monitor
scale. When pressure is other than 100 PSI, use the
following correction factor tables.
CORRECTION FACTORS FOR AIR AND GASES
SCFM (indicated) x (CF) = SCFM (actual)
CF = (f
1
) x (f
2
) x (f
3
)
Note: It is not necessary to use all correction factors.
TABLE 1
(f
1
) PRESSURE CORRECTION FACTORS
f
1
=
TABLE 2
(f
2
) TEMPERATURE CORRECTION FACTORS
f
2
=
TABLE 3
(f
3
) SPECIFIC GRAVITY CORRECTION FACTOR
f
3
=
INTERNAL GAGE PRESSURE
System pressure will vary from location to location in
a typical dynamic air or gas system. Because of this,
it is important that an accurate pressure gage be
used to determine flow conditions as close as
possible to the inlet port of the flow monitor.
4. If inner cartridge assembly or body casing
cannot be cleaned, is scored, pitted or damaged
beyond repair, replace monitor.
5. Clean polycarbonate window with soap and
water or a compatible cleaning solvent.
6. Clean and inspect O-ring assemblies for nicks
and cuts. Replace as necessary.
7. After monitor is cleaned, reassemble in reverse
order of disassembly.
8. Clean and inspect monitor every six months.
Properly filtered monitor will provide years of
trouble free service. If unit is not properly protected
by a filter, damage and malfunction can occur.
Damage caused by excessive contamination is not
covered by warranty.
9. If the cartridge clip is removed or lost, a new clip
should be used. Cartridge retainer clips are Waldes
No. 5105-12H for 1/4˝ and 1/2˝ models, No. 5105-
18H for 3/4˝, 1˝, 1-1/2˝, and 2˝ models.
RECOMMENDED FILTRATION
The manufacturer recommends system filtration of
at least a 74 micron filter or a 200 mesh screen. If
inadequate filtration has caused monitor failure, it
will normally fail in the open position. Some
systems may require a magnetic filter. Important:
Monitor damage caused by excessive
contamination is not covered by warranty.
STABILIZED CONTAMINATION
The goal of filtration is to create effective protection
from system contamination. Proper filtration
stabilizes contamination to allow fluid components
to function properly. A fluid system is considered
stabilized when “contamination in” equals
“contamination out.” Proper filtration must reduce
initial contamination to a stabilized level within an
acceptable time period. The entire system should
be stabilized in time to prevent premature wear or
damage to monitor components.
CONTAMINATION SOURCES
Fresh Fluid - When new or fresh fluid is stored
inside holding tanks, the fluid may be
contaminated with scale or metal flakes from inside
the tank. To prevent this type of contamination,
filter fresh fluid before adding to the system.
New Machinery - When building new machines, a
certain amount of built-in contamination is
unavoidable. Typical built-in contamination might
include dust, dirt, chips, fibers, sand, flushing
solutions, moisture, weld splatters and pipe
sealants. Flushing the system before operation can
reduce contamination but cannot eliminate it
entirely. Unless the system is flushed at a high
velocity some contamination will not be dislodged
until the system is in operation. System
contamination can cause fluid component
malfunction.
Environmental Contamination
- When
performing routine maintenance, the systems fluid
is commonly exposed to environmental
contamination. Exercise caution during routine
maintenance to prevent this type of contamination.
Change breather filter and system air filter regularly.
Self-Generated Contamination - Self-generated
contamination is a product of wear, cavitation, fluid
breakdown and corrosion. Systems that are
carefully flushed, maintained and have fresh fluids
√
14.7 + psig
––––––––––
114.7 psia
√
√
530
––––––––
460 + °F
1
–––––––
Sp. Gr.
F-55:HF Bulletin 7/24/09 9:54 AM Page 4