Dwyer HF User Manual
Page 3
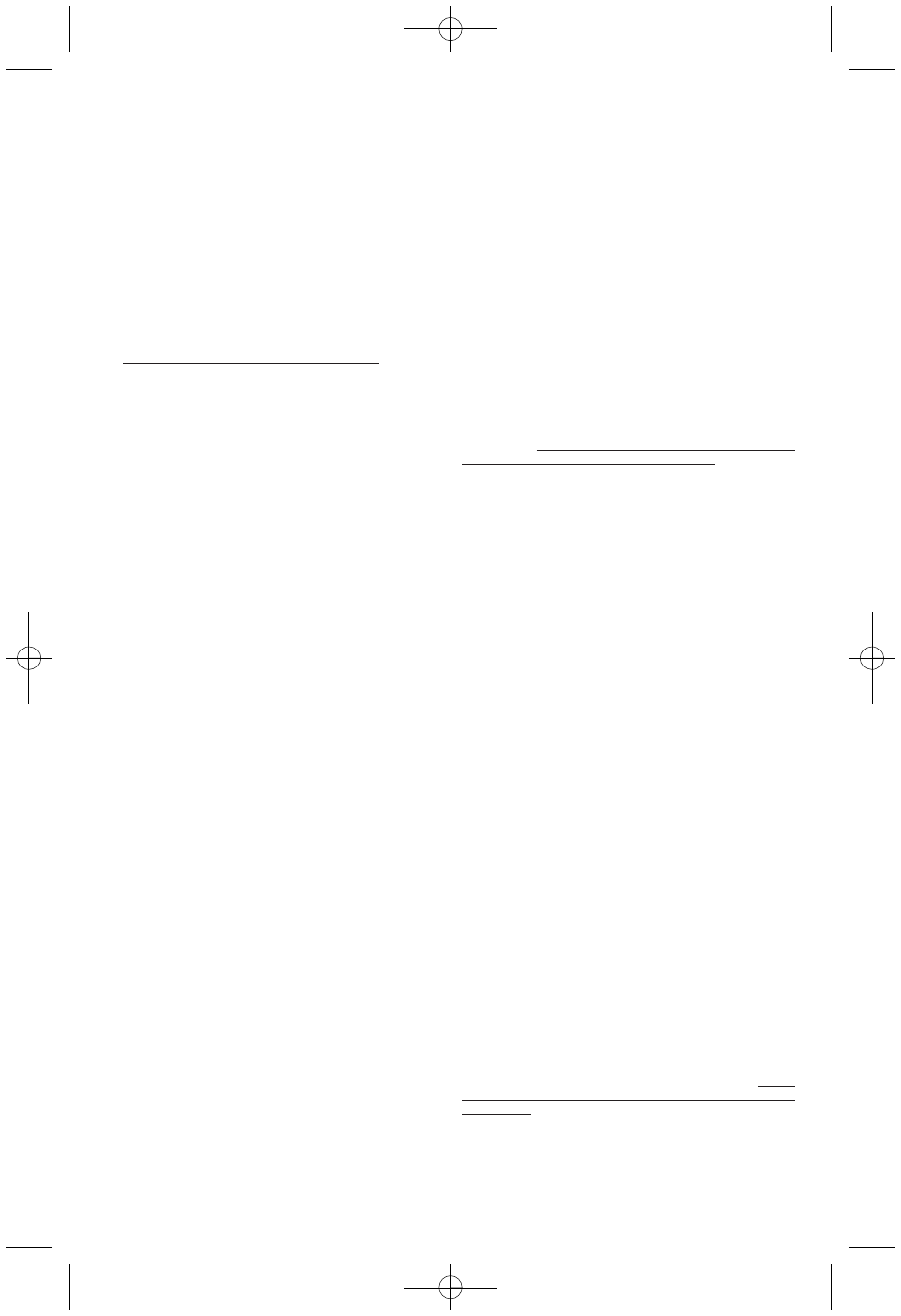
BASIC APPLICATION INFORMATION
The flow monitor can be installed directly in the fluid
line without flow straightening or special piping.
They are suitable for measuring the flow rate of most
liquids which do not contain particles larger than 74
microns.
1. The magnetic follower is sealed inside the Lexan
tube to allow use in areas where the unit might be
sprayed or washed with soap water.
2. Mount the monitor in a location allowing easy
access for reading and maintenance.
3. The monitor should not be located near hot pipes
or equipment which could damage the window tube
and/or scale.
4. Mount the monitor at least 1 ft (.3 m) from large
electric motors which can weaken or demagnetize
the internal magnet.
5. Aluminum should not be used for water.
WARNINGS AND PRECAUTIONS
1. These monitors are designed to operate in
systems that flow only in one direction, matching the
direction indicated by the arrow on the flow scale.
Operation in the reverse direction can damage the
monitor or other system components.
2. The window tube is made of polycarbonate which
can be safely cleaned with soap and water. many
other cleaning agents can damage this material,
causing discoloration or crazing. To check
compatibility, call General Electric’s polycarbonate
Compatibility Reference Line at 1(800)845-0600,
USA.
3. To maintain accuracy and repeatability, many
internal parts are precision machined and thus
require filtration or at least 74 micron or 200 mesh
screen.
4. All monitors are tested and calibrated using a light
hydraulic oil. Units are well drained, but some oil
residue may remain. Please check compatibility with
your fluid. Cleaning may be required before use. See
“Cleaning and Inspection.”
5. When installing aluminum or brass monitors onto
steel pipe, take caution not to over tighten
connections. Threads could strip if over tightened.
6. Aluminum and brass monitors should not be used
in systems where piping is not supported. Heavy
weight can cause the monitor to bend and
malfunction.
7. Do not exceed the maximum operating pressure
or temperature limit.
8. Pressure and flow surges can disengage the
outer magnet follower from the transfer magnet. If
this occurs, a shock suppressor should be used to
avoid repetitive malfunctions.
9. Caution should be used when using Teflon
®
thread tape on joints. Leave at least 1/8˝ (3 mm) of
exposed pipe on the end.
10. These monitors use an internal transfer magnet
in their design. Because of this be aware of the
following:
a. Keep computer disks or tapes away from these
units.
b. If metal particles are flowing through this device,
a magnetic filter may be required.
BASIC INSTALLATION
Series HF Flow Monitors are installed in-line and are
direct reading. They can be mounted in a vertical or
horizontal position as long as flow is in the direction
of the arrow on the side. No straight pipe is required
before or after the monitor. If necessary, 90° elbows
can be installed on both ends without significant
flow variation. When installing, apply a small amount
of pipe thread sealant tape or pipe thread sealant to
assure a good seal. Locate filter, if used, in front of
monitor and in a location allowing easy access for
routine maintenance. Refer to Warnings and
Precautions for additional information.
FLUID FLOW IN REVERSE DIRECTION
These monitors will not allow flow in the reverse
direction, opposite to the arrow on the scale. In the
reverse direction unit will act like a leaky check
valve.
If the application requires occasional reverse flow,
install a check valve in parallel with the monitor
which will force flow around the unit when reversed.
This type of check valve can be obtained from your
local fluid component distributor.
WARNING: Do not remove monitor from
system without proper and adequate safety
measures if fluid or gas is toxic, corrosive or
flammable. Shut down system and relieve
pressure before removing flow monitor from
system.
DISASSEMBLY
Important: It is not necessary to remove the window
tube or window seals to clean the monitor. Note
how the unit is disassembled to aid in reassembly.
Warning - Shut down system and relieve pressure
before removing monitor from flow line.
1. Use a clean, dry cloth to remove all foreign matter
from exterior of monitor, especially around threaded
connections.
2. Remove monitor from flow line.
3. With the arrow on the scale pointing upward,
secure the unit in a vice using the flats on the inlet
connection. DO NOT apply wrench or vice to Lexan
tube.
4. Use a wrench on the flats provided on the outlet
connection and turn counter-clockwise to loosen.
Either port may come loose. Do not remove end
connection at this time.
5. Remove monitor from vice. Hold unit so the end
connection that has been loosened is on top.
Remove loose connection.
6. Tilt open end of monitor over a clean cloth to
expose inner cartridge. Remove inner cartridge
assembly from body casing. NOTE: Because the
transfer magnet is coupled magnetically to the
magnet follower, you will notice a light resistance
when removing the cartridge. If cartridge does not
slide out, insert a wooden dowl in opposite end of
monitor and push or rap lightly on dowel until
cartridge breaks free. IMPORTANT: If inner cartridge
does slide out freely, it may be a sign of
contamination. Locate and remove the source of
contamination before returning monitor to service or
the problem will reoccur. It may be necessary to
install finer filtration or a magnetic filter in the
system. The transfer magnet is a powerful Alnico
magnet. Keep it away from metal chips and filings.
They can be difficult to remove when reassembling
and will cause premature failure.
7. Examine inner cartridge assembly for
contamination. If the inner cartridge assembly has
no contamination and is working properly,
reassemble unit and return to service. If
contamination is found, proceed to Cleaning and
Inspection.
CLEANING AND INSPECTION
1. Soak inner cartridge assembly in a suitable
cleaning solvent or soap and water. Caution: When
using a compressed air hose, wear proper eye
protection.
2. Remove parts from solvent. Use compressed air
and/or scrub lightly with a soft brush to remove any
remaining contaminants. Remove any magnetized
particles from transfer magnet.
3. Remove any contaminants from inside body
casing.
F-55:HF Bulletin 7/24/09 9:54 AM Page 3