Operation – Warren Controls 1800 Series Heavy Globe Control Valves User Manual
Page 9
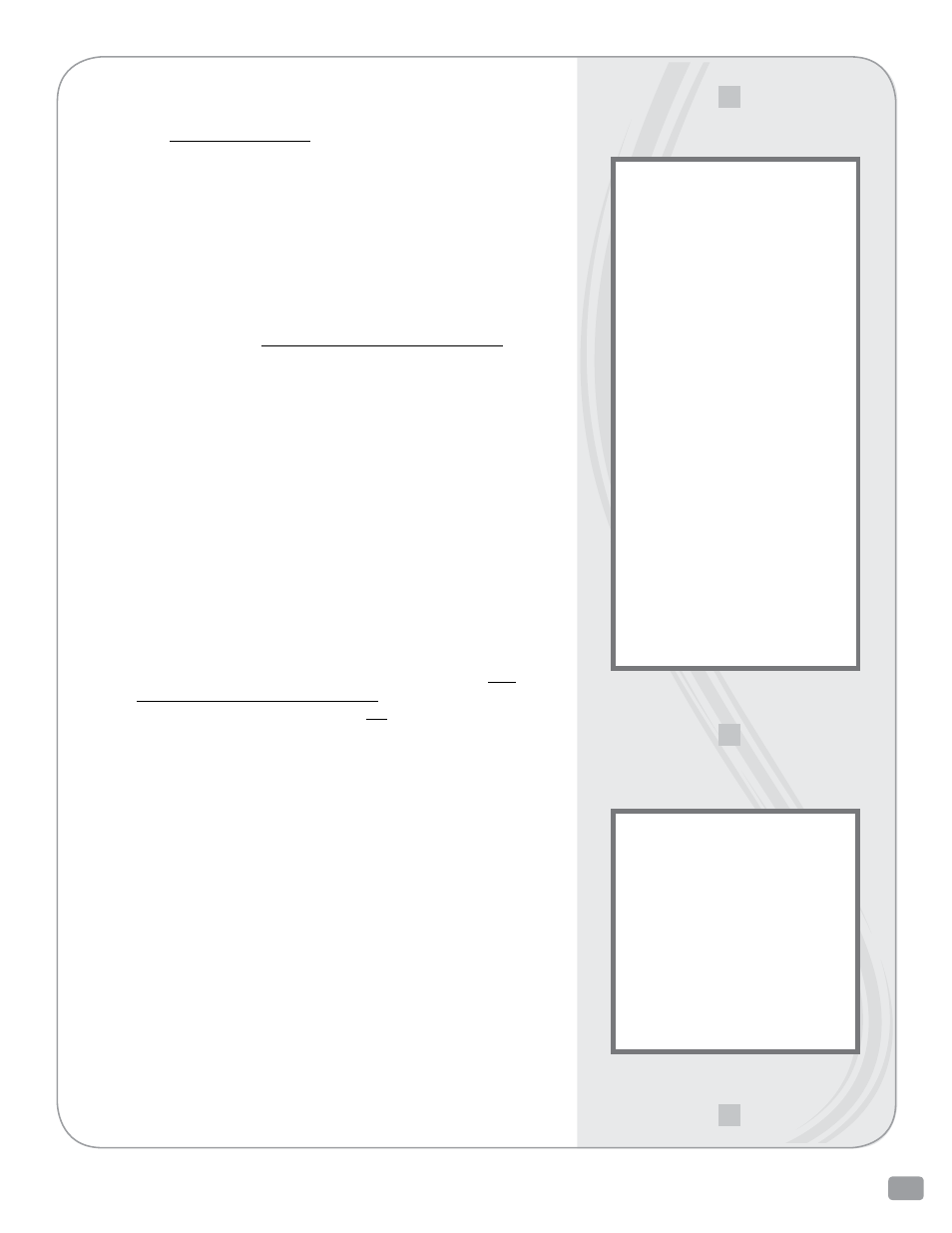
9
Series 1800 IOM1800 A 1209
operatIon
• Close inlet and outlet stop
valves.
• Check that valve responds
through rated travel in
relation to changes in input
signal. Rated travel is
shown by position of travel
indicator on valve stem
relative to travel indicator
on yoke.
• For valves fitted with
a handwheel, manually
operate valve with
no air applied, using
handwheel through rated
travel to check freedom
of movement. Return
handwheeel to its standby
position.
• Place valve in operation.
for proper operation
in all applications,
control valves must
be piped properly.
If you need detailed
information, please
refer to the "Heat
exchanger Bypass
piping applications"
document.
• Be sure to leave clearance to allow for actuator removal
(See Dimensions & Weights section for actuator removal
clearance).
• Before installing, be sure valve and piping are clean inside
and free of scale, chips, welding spatter, and foreign material.
Thoroughly blow out or flush pipe lines.
• The valve must be installed with the fluid flowing in the
correct direction(s). For proper operation in all applications,
control valves must be piped according to the corresponding
flow arrows, inlet markings, and port markings present
on each valve (See Information Present on Control Valves
section for location of important information on valve).
• Pipes must be aligned squarely with the valve at each
connection.
• If the valve has screwed ends, do not apply pipe dope to the
threads of the valve body or to the first two threads of the
pipe.
• If the valve has flanged ends, tighten flange bolts evenly to
prevent excessive stress and the possibility of cracking.
• If the valve has welded ends, prevent plug and cage
distortion by keeping excess heat from the body.
• The valve, actuator, and accessories (if so equipped) are
assembled, tested, and calibrated at the factory. The
actuator nameplate specifies set-up parameters used (See
Information Present on Control Valves section for location of
important information on valve). Do not exceed the supply
pressure listed on the actuator nameplate or you will damage
the valve and void the warranty.
• Supply air, instrument signal, and accessories should be
connected to ports or terminals as indicated on the control
valve.
• Final tuning may be required under actual operating
conditions.
• On critical or dangerous equipment, provide suitable safety
and emergency systems to protect personnel and property
from injury due to a valve malfunction. If the valve handles
flammable, toxic, corrosive or explosive fluids, provide for
safety in the event of valve leakage or malfunction.
• Do not obscure flow arrow plates or nameplates with paint.
If flow arrow plates or nameplates will be covered with
insulation, it is recommended the information on the plates
be transcribed on the outside of the insulation in the same
location as the plate.