Installation, Testing – Warren Controls E030 Electric Actuator User Manual
Page 6
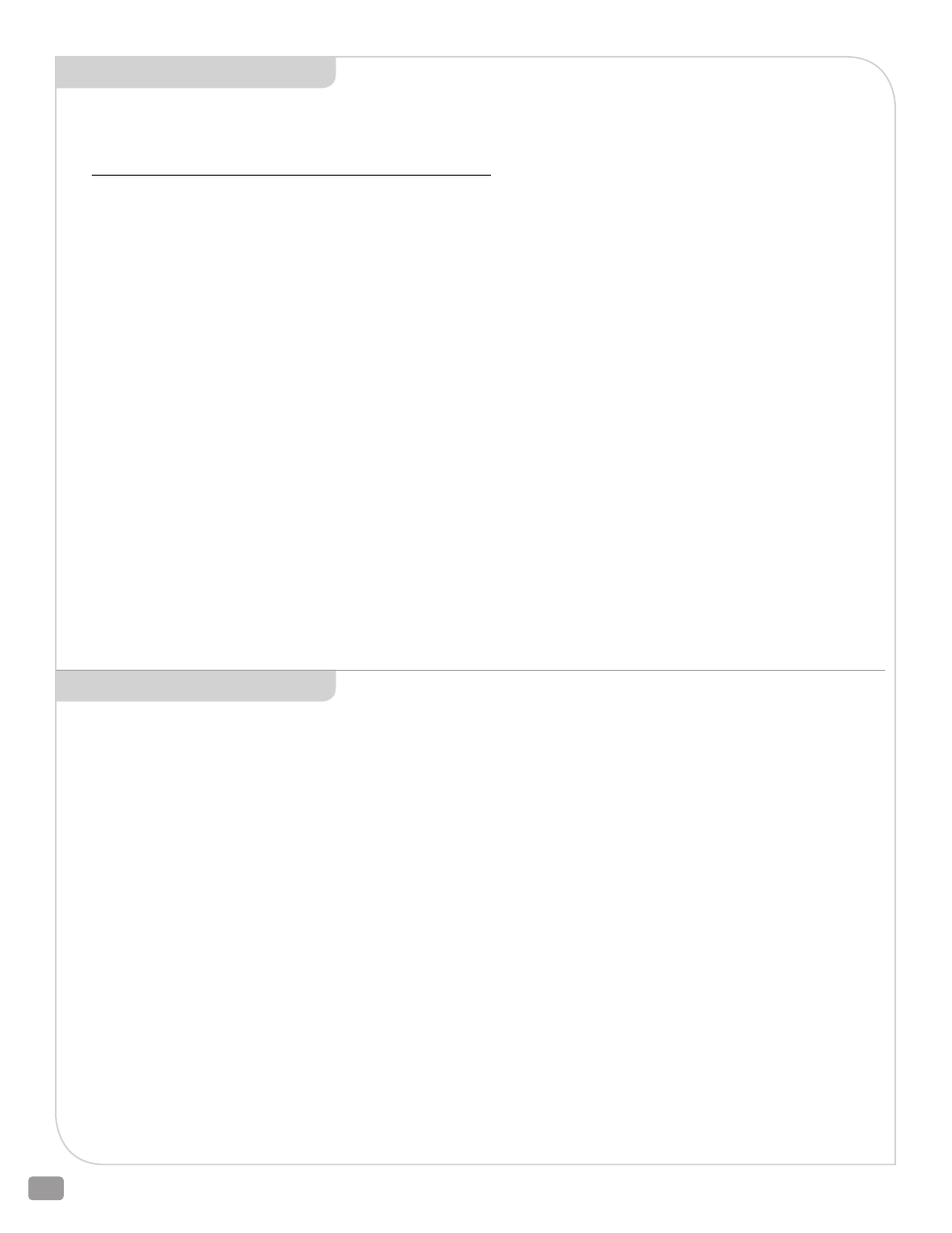
6
2600 Emrick Blvd • Bethlehem, PA 18020 • USA • 800-922-0085 • www.warrencontrols.com
INSTALLATION
1. Disengage the 24 VAC building power circuit before wiring. Verify that the battery inside the VMS-35 has its wires disconnected and
leave them that way for now. Disconnect them if they are connected.
2. Connect the VMS-35 to the actuator(s) as shown on wiring diagram. The VMS-35 can power one or two actuators.
Actuator A: Connect terminal N01 to white wire from actuator to drive the valve stem to the rotation switch position. Connect terminal
AC to red wire from actuator to provide power. Connect grounded reference – negative/black wire from actuator to terminal LN. Also
connect the control signal (-) to the black wire from the actuator. Connect terminal C1 to the control signal positive (+). If the control
signal is 4-20mADC a KR500 500 ohm resistor is required. Terminate the resistor between terminals N01 an LN.
Actuator B: Connect terminal N02 to white wire from actuator to drive the valve stem to the rotation switch position. Connect terminal
AC to red wire from actuator to provide power. Connect grounded reference – negative/black wire from actuator to terminal LN. Also
connect the control signal (-) to the black wire from the actuator. Connect terminal C2 to the control signal positive (+). If the control
signal is 4-20mADC a KR500 500 ohm resistor is required. Terminate the resistor between terminals N02 an LN.
3. While still disconnected, wire the VMS-35 to 24 volts AC power. Connect the hot to terminal L then neutral to terminal LN.
4. Engage the 24 VAC building power.
5. Verify that building power is live then connect the loose red wire inside the VMS-35 enclosure to the positive (+) battery terminal and
the black wire to the negative (-) battery terminal.
NOTE: Engage the 24 VAC power to the VMS-35 before connecting the battery. Connecting the battery first causes the VMS-35 to go
into the power failure mode. If there are conditions other than power failure during which the actuator should be driven to the rotation
switch position (See page 11 for explanation of rotation switch position), replace the jumper between RC & LN with a contact that opens
on demand.
TESTING
Disconnecting the jumper between RC & LN, with building power on, will drive the actuator to the rotation switch position (See page 11
for explanation of rotation switch position).
Testing the VMS-35 and the charging system and battery is recommended yearly. To test charging measure the voltage between terminals
TG & BT. TG is negative. When the power supply is charging correctly the voltage will be 13 - 14 volts DC. To test the battery disconnect
LN or L, wait for the actuator to return to the rotation switch position (See page 11 for explanation of rotation switch position) and then
measure the voltage between TG & BT. A good and adequately charged battery will be between 10 - 12 volts DC.
The VMS-35 is a standby power supply.
It is intended to drive an actuator to either open or close a valve during a power failure. The VMS-35 can power one or two actuators.