Periodic checks / proof tests, Periodic checks / proof tests 6.1 periodic checks, 2 proof tests – KROHNE TT 51 SERIES EN User Manual
Page 11
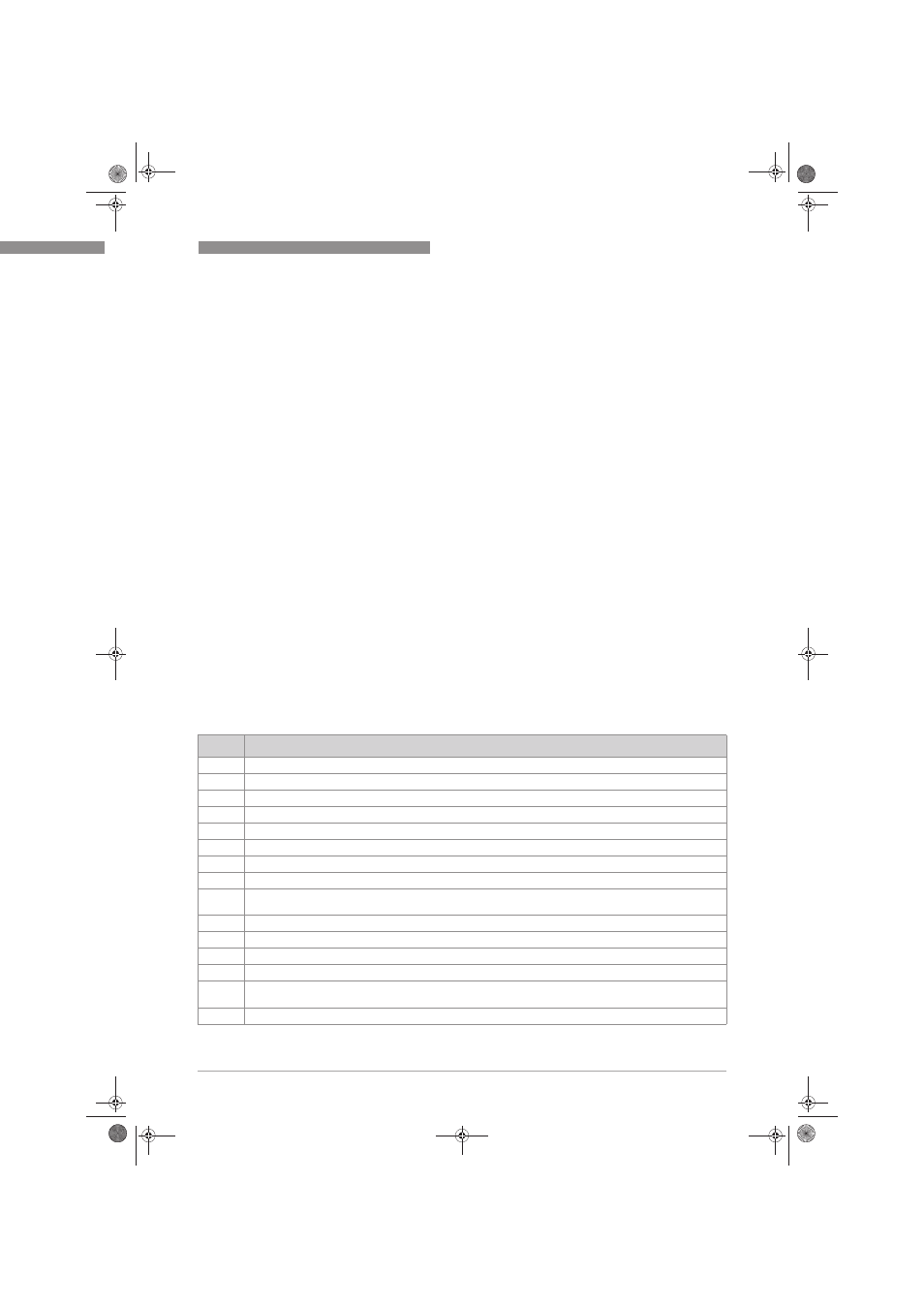
PERIODIC CHECKS / PROOF TESTS
6
11
TT 51 SERIES
www.krohne.com
09/2010 - 4000869801 - AD TT 51 SIL R01 en
Periodic checks / Proof tests
6.1 Periodic checks
The user of the transmitter is responsible for:
• The set-up, SIL rating and validation of any sensors connected to the transmitter
• Project management and functional testing
• Configuration of the transmitter according to the description in the following chapters.
It is recommended that the user performs regularly proof tests of the sensors used with the SIL
transmitters.
Proof test of the SIL transmitter should be made based on the required PFD depending on the
used sensor. For detailed information refer to
Safety-related characteristics on page 13.
For PFH figures a proof test interval of one year is recommended. The needed frequency of proof
tests necessary for the safety-related system must be found by the customer.
The proof tests should be done by the user at following measures:
• At commissioning of the SIL transmitter
• Replacement of the old connected temperature sensor by new ones
• Reconfiguration of the SIL device
• At need of the SIL transmitter relocation
6.2 Proof tests
The proof tests shall cover SIL safety test requirements. Up to 99% of the internal failures shall
be detected via the proof tests. The input to the SIL transmitter is simulated and tested for the
internal errors in the hardware and the firmware.
Proof test configuration
Step
Description
1
Connect transmitter to the PC via USB interface.
2
Start ConSoft (Check version: "Help menu → About").
3
Identify transmitter by clicking on "Read from transmitter" button.
4
Decide the choice of the SIL password (default value is "0000").
5
Configure the transmitter by selecting sensors tab in the transmitter window.
5.1
The sensor for Channel 1 and the connection for Channel 1.
5.2
The sensor for Channel 2 and the connection for Channel 2.
6
Choose measuring range for process value by selecting "Function" tab in the transmitter window
6.1
Select measuring output mapping (Channel 1; Channel 2; Ch 1 minus Ch 2; Ch 2 minus Ch 1; minimum of Ch
1 and Ch 2; maximum of Ch 1 and Ch 2; Average of Ch 1 and Ch 2).
6.2
Select output values in mA which correspond to the chosen measuring range.
6.3
Select filtering level and line frequency rejection.
7
In the error monitoring tab select check box for sensor break. Select upscale (≥21 mA) value.
7.1
Select check box for sensor short circuit. Select upscale (≥21 mA) value.
7.2
Select check box for sensor low isolation. Select upscale (≥21 mA) value.
Select desired resistance limit; default: 300 kΩ
7.3
Select check box for sensor backup.
.book Page 11 Thursday, September 9, 2010 4:19 PM