Safety rules when using an impact wrench, Lane end d.h.moppett (man. director), Accessories – Universal Air Tools UT150 (HP150) User Manual
Page 4
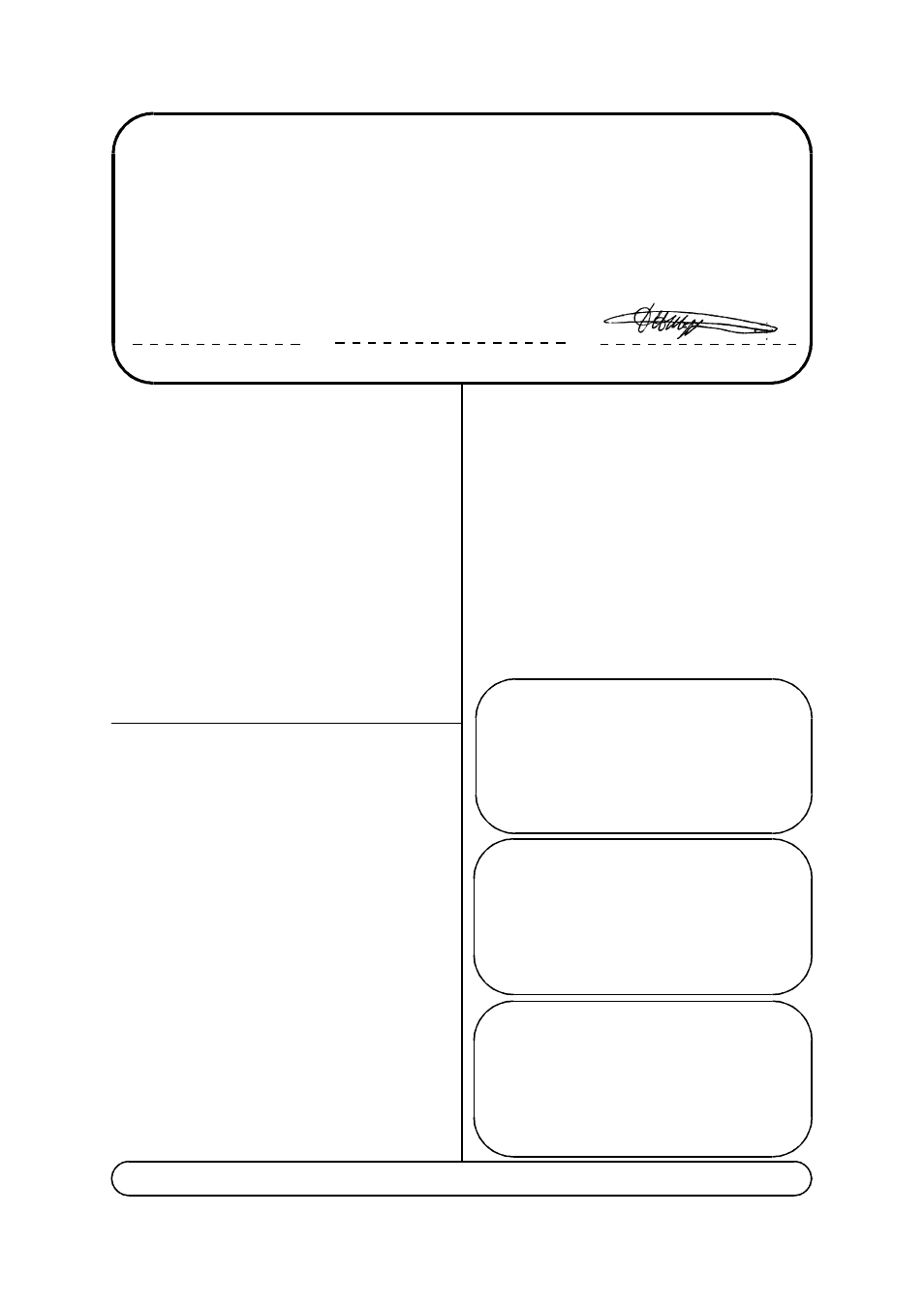
tool is running.
10) Do not exceed maximum recommended air pressure.
11) Use safety equipment as recommended.
12) The tool is not electrically insulated. Do not use where there
is a possibility of coming into contact with live electricity.
13) Preferably shut off the air supply before changing sockets or at
least ensure that the hands are well clear of the operating trigger.
14) Take care against entanglement of moving parts of the tool with
clothing, ties, hair, cleaning rags, etc.
15) When loosening fasteners first ensure that there is sufficient
clearance behind the tool to avoid hand entrapment. The tool will
move away from the threaded joint as the nut/bolt etc. is loosened
and rides up the thread moving the tool with it.
16) Only use extensions, adaptors and universal joints suitable for use
with impact wrenches.
17) If the tool appears to malfunction remove from use
immediately and arrange for service and repair.
18) Prolonged exposure to vibration may cause injury.
Safety Rules When Using an Impact
Wrench
1) Read all the instructions before using this tool. All operators must be
fully trained in its use and aware of these safety rules. All service and
repair must be carried out by trained personnel.
2)The socket used must be of the correct drive size and the "impact"
type. Never use sockets other than impact type.
3) Do not use sockets with excessive wear to the input and output
drives. Check that the square on any other type of drive or the impact
wrench is not cracked or excessively worn before fitting or changing
socket, extension, etc. Make sure that the socket is firmly fixed to the
tool.
4) Always ensure that a stable position or footing is adopted before
using the tool.
5) Ensure that the tool has been correctly set up on a test joint.
Incorrect set up could cause joint breakage with sudden and
unexpected movement of the tool.
6) Use only correct spare parts for repair.
7) Always ensure that the reverse valve is in the correct position
before operating the tool. Do not run the tool unless the socket is first
located on the joint.
8) Check hose and fittings regularly for wear. Use quick connect
couplings only as recommended. See "Putting into Service". Do not
carry the tool by the hose and ensure that the hand is away from the
on/off valve when carrying.
9) Do not attempt to hold or guide the socket by hand when the
(26). Insert rotor (28) to rear end plate. Insert ball bearing (31) to
front end plate (30). Insert six rotor blades (29) to rotor. Insert
rotor and front end plate to cylinder (27). Insert cylinder to motor
case (32). Put motor housing gasket (24) and handle C.P. (1) on
motor case C.P. Screw four cap screws (23) through handle C.P.
Grip motor case C.P. in leather-covered or copper-covered vice
jaws. Put O-ring on motor case C.P. Put grease on the centre
hole of anvil (36), plunger A (39, plunger B (41), spring (40), cam
(38), anvil piece (37) and retainer (35). Assemble them as Fig. 2.
Grease up inside wheel and as shown in Fig 3, meeting the top
of anvil assembly with dented part of wheel inside, then put anvil
assembly into the wheel inclining a little. Put bushing (42) to
cylinder. Insert cylinder to rod of rotor. Put impact housing C.P.
(45) on motor case C.P. and screw four cap screw (48) through
impact housing C.P.
On completing assembly ensure all parts are tight and trigger and
reverse valve mechanisms operate freely. Depress trigger and
pour into inlet bushing (3) 10ml of a suitable pneumatic tool
lubricating oil. Release trigger and connect to a suitable air supply
and operate the tool slowly for 2 to 3 seconds to allow the oil to
circulate.
Distributor
Notes
Page No 4
Declaration of Conformity
Universal Air Tool Company Limited
Unit 8, Lane End Industrial Park, High Wycombe, Bucks, HP14 3BY, England
declare under our sole responsibility that the product
Model UT150 (HP150) 1½” SD Impact Wrench, Serial Number
to which this declaration relates is in conformity with the following standard(s) or other normative document(s)
EN792 (Draft), EN292 Parts 1 & 2, ISO 8662 Parts 1 & 7, Pneurop PN8NTC1
following the provisions of
89/392/EEC as amended by 91/368/EEC & 93/44/EEC Directives
Place and date of issue
Name and signature or equivalent marking of authorised person
Lane End
D.H.Moppett (Man. Director)
This document may not be copied wholly or in part by anyone without the consent of the Directors of Universal Air Tool Company Limited
© Copyright of Universal Air Tool Company Limited, established in the United Kingdom, 1994
Accessories
Designed & Written in the U.K.