I. introduction – MAHLE RTI BRC550 User Manual
Page 3
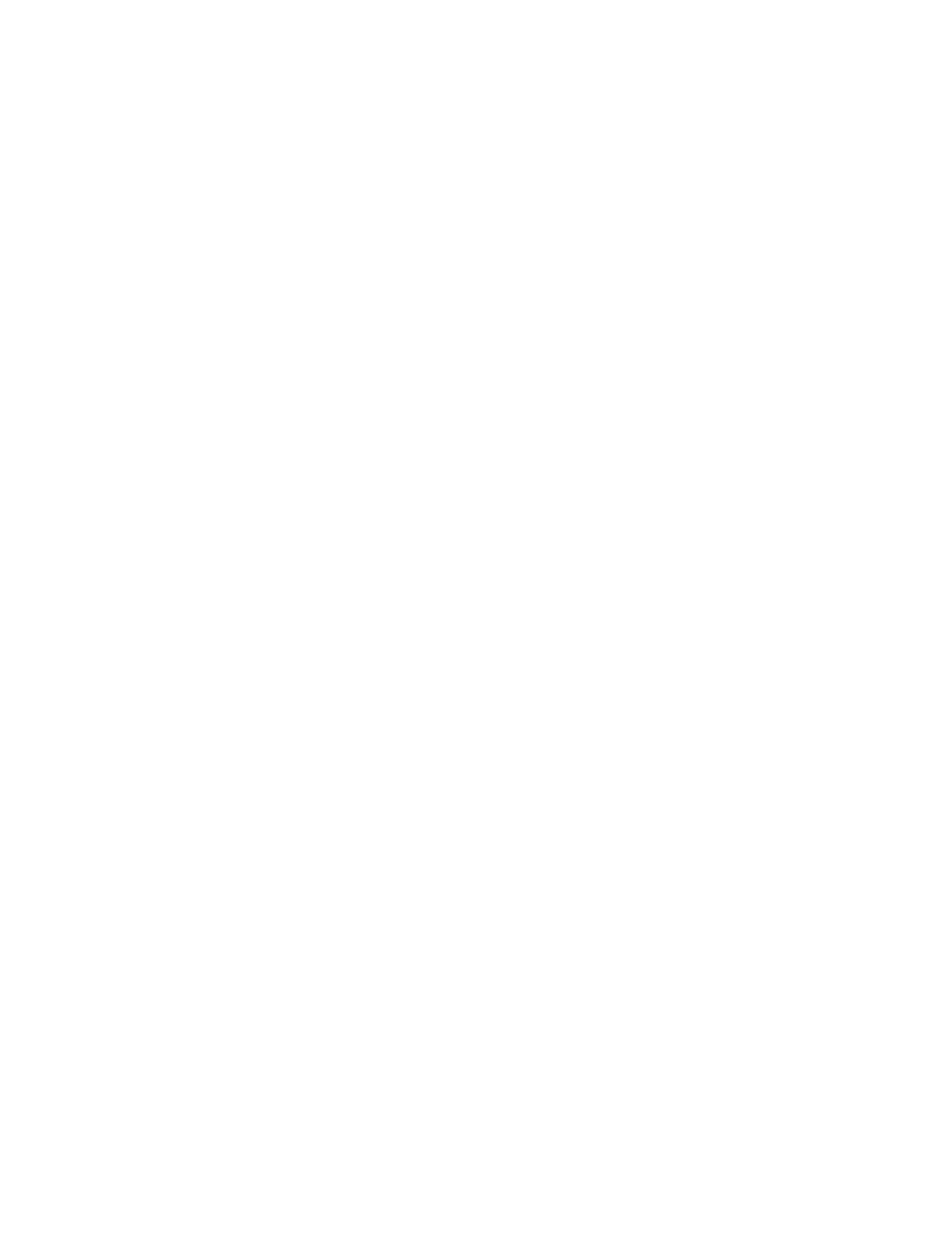
Page 1
I. Introduction
Thank you for your purchase of a BRC500/550 brake lathe. Congratulations on your choice! The
BRC500/550 is designed to outperform every other comparable brake lathe in all respects.
The BRC550 is just like the BRC500 except that the BRC550 comes with an exclusive RTI feature
that we call “offset step feed”. The offset step feed can be turned on or off. When off, the BRC550
operates in the same way as the BRC500. When the offset step feed is on, the feed for the brake
disc cutting tools is turned on and off intermittently so as to create a non-directional finish
automatically. Non-directional finish is normally only an issue when cutting at high feed rates. The
BRC500 when set at low feed rates for a finish cut will produce a surface finish so good, that no
directional pattern is noticed.
The BRC500 was designed as a completely new product, with the new requirements for brake disc
turning for modern late model automobiles and light trucks in mind. The BRC500 is designed to
minimize run out. In fact “near zero” run out can be easily achieved. Minimizing brake disc run out
is an important aspect of modern brake service. Additionally, the BRC500 is designed to allow you
to produce a surface finish that is superior to that on most new rotors. The BRC500 can
consistently produce better than 35 micro inches where most other lathes can do no better than
40 or 50 micro inches. This smooth surface finish is required for fast break in and maximum
stopping power. Brake lathes designed in the past (even many that are sold today) cannot in most
cases match the results of the BRC500.
Another major design innovation with the BRC500 is the simplicity of the set-up using a new
concept in adaptor and arbor design. You will note that the BRC500 uses a special “hub surface
locator” along with a special high mass “outboard supporting cone” and a special 1 3/16" (30 mm)
“big arbor” . With this one basic standard set-up, composite and hubless rotors with a hat diameter
of less than 6.95 inches (176 mm) can be turned--this set-up and the big arbor with 40% more
strength than competitor’s arbors is one of the secrets to achieving near zero run out and a
superior finish. For larger rotors on HD trucks, a larger set of adaptors is required as an option--the
set-up being similar. For hub-type rotors, a set of bearing race cones are supplied as standard.
Drums are set-up in a manner almost the same as with rotors. Changeover time from drums to
rotors or from rotors to drums is less than one minute.
Running the BRC500 is simple. It can be set for one of two spindle speeds. In most cases you will
use the 110 RPM slow speed, but by making a fast belt change, the speed can be increased to 220
RPM to allow an extra superior finish on small passenger car rotors. The BRC500 can be used as
a “single pass-one cut” machine by selecting a feed rate setting of 2.5-3. This is the recommended
technique for drums. However, RTI recommends a “two pass” machining process for rotors, with
a setting of 5-6 for a rough “foundation” cut just deep enough to clean up the rotor, and an extra
fine finish cut, with a depth of only 0.001-0.002" (0.025-0.05 mm) per side and a setting for the feed
of 1, taking full advantage of the special electronics and cutting tool design of the BRC500/550.
This two pass technique will not remove any more material than necessary, and even though it may
take a few minutes longer, it will result in a more perfect rotor in every respect.
The precision machined components of the BRC500/550 are produced by our affiliate, Hunger in
Germany, using the most modern and sophisticated machine tools in the world. For more than 30
years, Hunger has been the leading automotive brake lathe manufacturer in Germany. The
electrical controls are made in the USA, with final assembly of the electrical control components
and assembly/testing of the complete lathe done by RTI in the USA.