V. cutting brake rotors/discs – MAHLE RTI BRC550 User Manual
Page 12
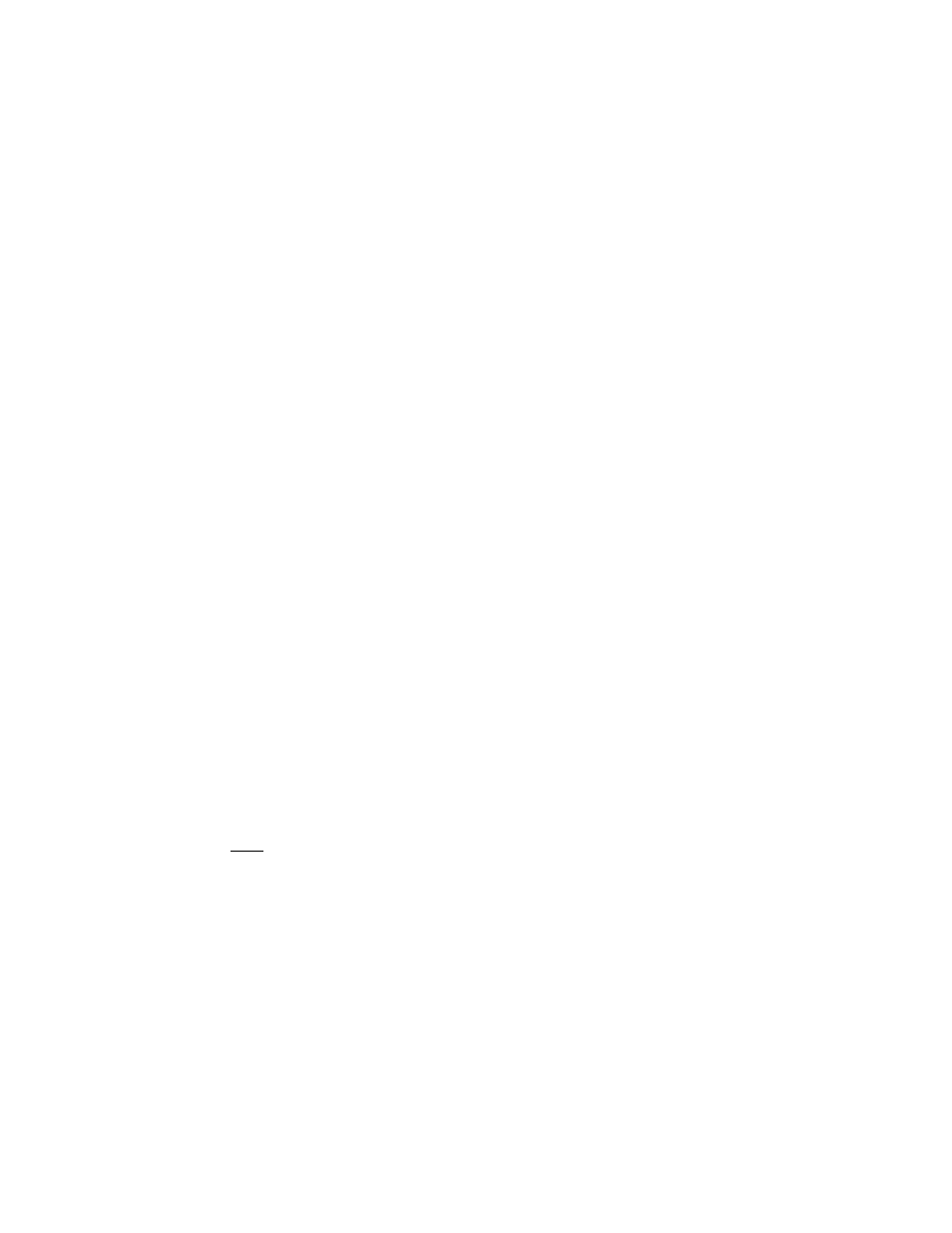
Page 10
V. Cutting Brake Rotors/Discs
A. Hubless Rotors. Figure 5 shows the most common adaptor set-up. Install the Hub Surface
Locator onto the arbor with the smallest diameter flat surface against the arbor flange. The largest
diameter flat surface with the slots now simulates the flat surface of the hub of the vehicle. (Unlike
other lathes, on the BRC500/550, special care has been taken to grind both surfaces of the Hub
Surface Locator so that there is near zero run out of the large diameter flat surface.) Now install
the Spring, Inboard Supporting Cone and brake rotor/disc as shown. The Inboard Supporting Cone
will be pushed toward the rotor by the spring and will keep the rotor centered. Install the Outboard
Supporting Cone and clamp the total assembly by installing spacers as needed and tightening the
left hand thread of the arbor nut. Be sure to spacers extend slightly past the arbor shoulder, use
the special washer, and do not over-tighten the nut. Figure 5 shows the set up using the standard
adaptors for brake rotors with an inside hat diameter less than 6.95" (176 mm). Figure 6 shows
the same set up using the optional HD truck adaptors for larger rotors. The standard adaptors can
be used for larger rotors, but in some rare cases the optional adaptors are needed to minimize
vibration on extra large rotors with extra thin hat web sections.
B. Composite Rotors. One revolutionary aspect of the special adaptors designed for the
BRC500/550 is that these adaptors work very well for composite type rotors as well. No special
care or set up for composite rotors is required. The secret is the fact that the rotor hat web section
is clamped tightly with full metal to metal contact between the Hub Surface Locator, rotors hat web,
and the Outboard Supporting Cone.
C. Vibration Dampening. The BRC500/550 comes with a Vibration Dampener rubber ring. This
should be installed onto the largest outside diameter of the rotor. There are many other types of
vibration dampener types, including a device using two (2) rubbing blocks. On any rotor larger than
10" (255 mm) some type of vibration dampening device is recommended to avoid excessive high
pitched noise or vibration when machining the rotor.
D. Rotor and Hub Assembly. See Figure 7 for the set up for rotors with the hub installed. Here
instead of clamping to the rotor hat web section, the clamping is to the bearing races in the hub.
To insure that there is no abnormal run out, first be sure that the bearing races are in good
condition with no pitting and then after first tightening the arbor nut, loosen it very slightly and re-
tighten.
E. Check Spindle/Arbor/Rotor Rotation. Plug the power cord into a receptacle with the correct
power rating and safety features as described in the Safety section of this manual.
Be sure all items are clear of the spindle/arbor/rotor assembly, and be sure that the black knobs
in the center of both hand wheels are pulled outward. The start the lathe momentarily by pushing
the green start button. Check for proper rotation. Stop the spindle/arbor/rotor’s rotation by pushing
the red mushroom stop switch.
F. Setting up for cutting. With the black knob inside the hand wheel pulled out, manually turn the
wheel, moving the cutting tool slide and the cutting tips to a position almost touching the rotor’s
largest diameter. Note that there are two locking levers, one on the top of each cutting tool holder
along with a graduated adjusting knob to the left. By locking down one lever, with the other
loosened, turning the adjusting knob will move the tool holder with the lever loosened. Move each
tool holder so that the cutting tips are very close, but not touching each side of the rotor--then move
the tool slide and cutting tips so that they are approximately 1/4" (6 mm) inside the rotor’s largest
diameter braking surface.