7 self acting temperature controller, 8 instrument air for the vortex tube, 9 vortex theory of operation – Yokogawa Advanced Reflux Sampler User Manual
Page 7
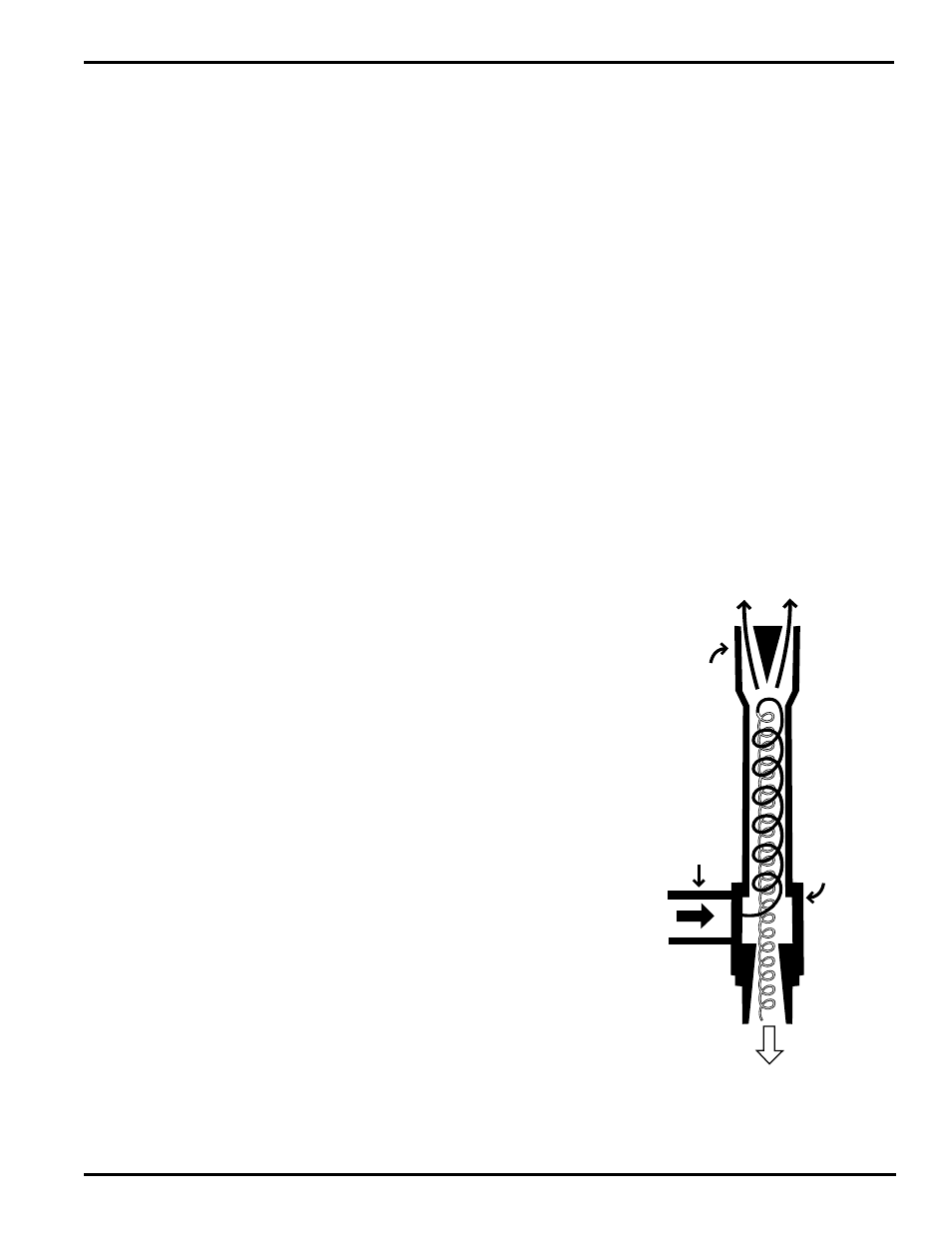
7
All Rights Reserved. Copyright © 2011, Yokogawa Electric Corporation. Subject to change without notice.
April 2011
IM 11A00V01-01E-A
the sample gas is achieved. There are two cooling coils located in the same heat exchanger chamber, which helps
provide more accurate and efficient cooling. In the head-space of the heat exchanger, a stainless steel fine filter mesh is
installed to act as a mist trap and final liquid sample droplet trap prior to existing the sampler. Flow of the cooling media
through each coil is automatically controlled to ensure a constant outlet temperature is maintained. The sample is normally
saturated at the outlet temperature and pressure. The cooling media is supplied by vortex air cooler(s) via the self-acting
controller.
3.6 Outlet Temperature Section
Located on the outlet of the heat exchanger is the outlet temperature indicator. For self-acting controller units, a
temperature sensor is installed. The self-acting temperature controller is located (screwed) directly in to the top of the
heat exchanger in to the headspace area. This provides the most accurate temperature reading and control of the actual
sample outlet temperature. The purpose of temperature measurement at this point in the YARS is to control the final outlet
temperature (or maximum dewpoint). Depending upon the application, this outlet temperature may be typically between
41-80
o
F (5-27
o
C).
3.7 Self Acting Temperature Controller
The operation and maintenance of the adjustable self-acting temperature controller is described herein.
3.8 Instrument Air for the Vortex Tube
The standard media used by the Vortex air tube(s) is ISA grade Instrument air. It is possible to change the cool air
outlet temperature by adjusting the recessed screw (needle valve) located in the hot air exhaust. A counter-clockwise
adjustment of the valve will produce colder temperatures while a clockwise adjustment will produce warmer temperatures.
This ability to adjust the temperature may be considered when fine-tuning the temperature control system to ensure
optimum temperature stability. The performance of the Vortex tubes is also based on the incoming instrument air
temperature. For more efficient operation, avoid direct sun light (and other heat emitting sources) when running the air line.
3.9 Vortex Theory of Operation:
Vortex tubes are simple devices that contain no moving parts and
therefore may be used as a reliable device for generating a cold air supply.
Compressed air (clean, dry, ISA Grade) will enter the cylindrical chamber
(to the left of the diagram) and is caused to rotate internally. This rotating
air moves down the inner walls of the hot air exhaust chamber at extremely
high velocity. When exiting the hot exhaust (to the top of the diagram), a
portion of the air is directed back through the center at lower speed than
the exiting air. Heat transfer from the inner, slow moving air to the exiting,
fast moving air causes cold air to be generated. This cold air exits via the
cold air exhaust (shown at the bottom of the diagram).
Vortex tubes produce less air flow at colder temperatures and have less
BTUH capacity. Tubes are available in a variety of sizes depending upon
the application. Maximum efficiency will be achieved when operating
at 100 psig instrument air pressure and while they can operate at lower
pressure, the efficiency will be less (typically 60% efficient at 55 psig)