Theory of operation, 1 brief history of reflux samplers, 3 steam supplement – Yokogawa Advanced Reflux Sampler User Manual
Page 6
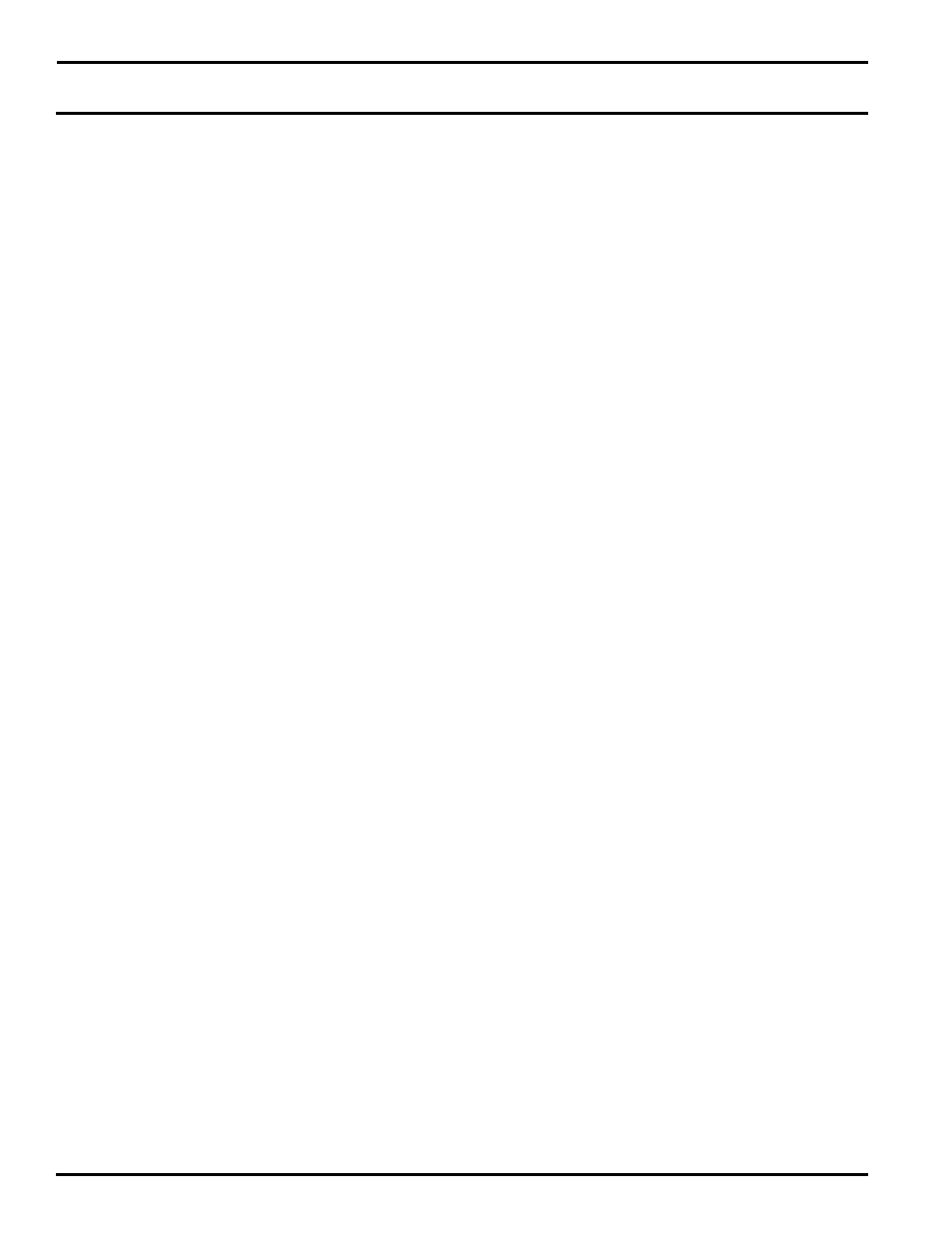
6
All Rights Reserved. Copyright © 2011, Yokogawa Electric Corporation. Subject to change without notice.
April 2011
IM 11A00V01-01E-A
This section of the manual describes the basic theory of operation, designed to give the user a better understanding and
help in operation and maintenance.
3.1 Brief History of Reflux Samplers
The concept of the Reflux Sampler was introduced in mid 1970’s and until the inception of the Advanced Reflux Sampler
(YARS), it had changed very little. Process analysis needs during the mid 1970’s were not as critical as they are now and
consequently, the Reflux Samplers designed previously no longer meet today’s demands that are more stringent. The
reflux sampler was originally designed to overcome the problem of constantly plugging sample probes installed on the
Transfer Line Exchangers (TLE) of ethylene cracking furnace effluents. This high temperature cracked gas effluent is high
in particulate and condensables (moisture and heavy hydrocarbons) content and therefore prone to plugging. The idea
that the condensables could be used to backwash a particulate filter was conceived and a Reflux Sampler was then
developed. A simple filter mesh was used to trap the particulate matter.
3.2 Filter Section
The lower section of the YARS is for particulate filtration and provides some primary sample cooling. Typically flange
mounted directly to a customer supplied process isolation valve and flange mounted to the heat exchanger section of
the YARS. The filter media is nominally stainless steel wire mesh that traps any particulate matter such as coke from the
ethylene furnaces and/or catalyst fines. During normal operation, the temperature at the filter section outlet should be
in the order of 120
o
F (50
o
C), indicating a balanced refluxing condition is established. This filter section is cooled by the
condensate that has dropped out from the heat exchanger mounted directly above the filter. The condensate also acts as
a trap for finer particulate matter. In certain environmental conditions where sub-zero temperatures are anticipated, it may
be desirable to insulate the filter section. This will prevent premature condensing and allow for a balanced refluxing action.
3.3 Steam Supplement
For the YARS to function reliably there must be sufficient quantity of condensable media in the sample. For applications
that have high particle loading and limited condensables present, steam should be added at the inlet. The YARS filter
section has a steam inlet facility located at the inlet. A suitably rated needle valve is provided for regulating a nominal flow
of steam in to the filter section via an inverted tube such that the steam is directed up in to the filters. Note that the steam
is added directly to the sample and therefore the composition will be affected the H
2
O addition. As each application has
many different operating parameters, there are no specific settings for the quantity of steam addition and each application
is set-up individually.
3.4 Inlet Temperature Section
Mounted between the filter and heat exchanger section is the inlet temperature thermowell. As standard, a suitable
temperature gauge is installed in the thermowell. The purpose of temperature measurement at this point in the YARS is
to help establish the correct temperature gradient required for refluxing. The two undesirable conditions within the filer
section are as below:
•
Temperature reading too high – will cause the heat exchanger to work excessively and indicates a problem
elsewhere in the system
•
Temperature reading too low – will cause the condensable media to dropout early in the filter section and not
provide proper filter cleansing by reflux.
When troubleshooting the YARS, consider the correct temperature at this point.
3.5 Heat Exchanger Section
This is truly unique to the YARS in many respects. This section provides the cooling of the sample and is most critical to
the overall operation. As the sample gas rises from the filter section, through the inlet temperature section, it is channeled
in to the heat exchanger chamber. The sample gas rises through a chamber in which the cooling coils are concentrically
mounted. The design of the heat exchanger is such that maximum surface area contact between the cooling coils and
3. THEORY OF OPERATION