1 2-2 <2 quick start – Yokogawa Extractive Oxygen Gas Analyzer TDLS220 User Manual
Page 9
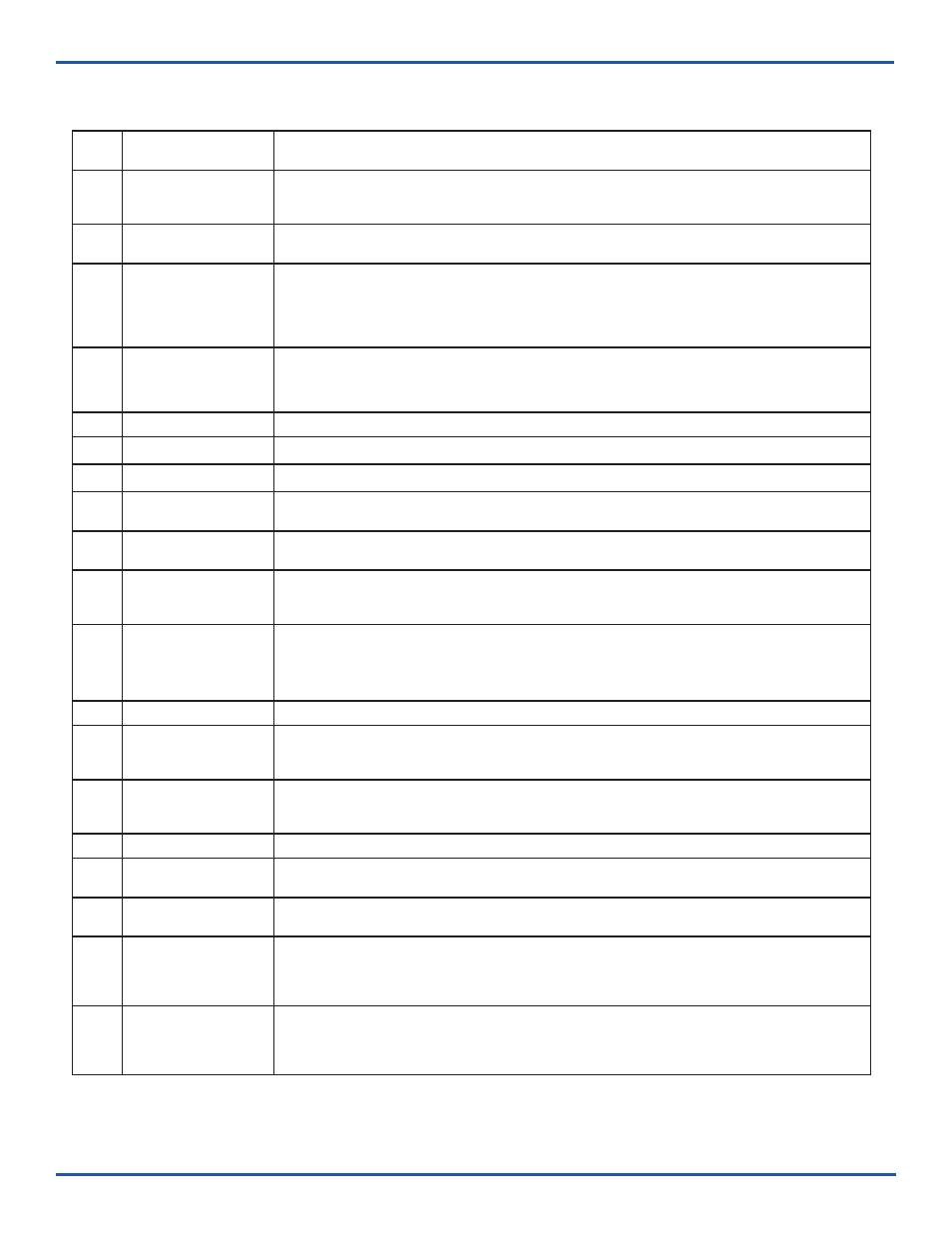
IM 11Y01B02-11E-A 3rd Edition :August 14, 2012-00
2-1
2-2
<2 QUICK START>
6.0
Checking
If there is an installed optional 6.5” Display and Keypad – Observe the Main Menu messages and status
information.
6.1
If there is no installed User Interface, then connect a laptop PC via Ethernet to the SBC mounted on the
backplane. Initiate the supplied UltraVNC software from the laptop to initiate a VNC session with the
‘blind’ analyzer and observe the analyzer Main Menu via the laptop.
6.2
AT this time there may be one or more alarm message due to low transmission, out of range parameters or other –
final system configuration is still required!
6.3
If the analyzer displays a Warning “Validation Required” then this indicates that there is no target gas
absorption peak found at start-up. Either, shut down the analyzer, introduce some measured gas into the
flow cell and re-start or perform a validation. This will ensure that the analyzer is correctly tuned to the
measurement gas absorption peak. If this Warning cannot be cleared by either method, please contact
Yokogawa Laser Analysis Division or your local agent for further assistance.
7.0
Configure
BASIC
By way of the appropriate user interface, the correct process parameters and other parameters can now
be entered.
7.1
Enter the Basic Menu and go to Configure.
7.2
Gas Pressure
Enter in the correct process gas pressure (if Active, see Advanced Configure).
7.3
Gas Temperature
Enter in the correct process gas temperature (if Active, see Advanced Configure).
7.4
If any other parameters are required to be set (such as analog I/O ranges, alarms levels, Auto Validation
sequences) then the Advanced Menu needs to be accessed.
Advanced Menu access is Password protected (default 1234, can be changed by user if necessary) and should only be
used by skilled and trained persons - Contact Yokogawa Laser Analysis Division or Local Agent if any doubts!
Go to the Data section under Basic and configure the appropriate ‘Record Result Data’ settings. This will
ensure the analyzer stores important information during operation that may be used to verify operation/
status/diagnostics and other trouble shooting.
8.0
Configure
ADVANCED
Using the correct password (Default 1234), enter in to the Advanced Menu, then the Configure.
8.1
Select the desired measurement units for path length, pressure and temperature.
8.2
Select Fixed or Active.
If Fixed, enter in the correct process gas pressure.
If Active, enter in the 4-20mA input signal range proportional to the pressure transmitter output range.
8.3
Select Fixed or Active.
If Fixed, enter in the correct process gas temperature.
If Active, enter in the 4-20mA input signal range proportional to the temperature range.
8.4
Configure the system I/O by entering in to the System I/O sub menu in Configure.
8.5
If the optional Analog I/O board is installed, then select Analog Output and set the appropriate 4mA and
20mA values for Ch 1 Concentration and Ch 2 Transmission.
8.6
Select what mode (Block, Track or Hold) the 4-20mA outputs are to be when the analyzer is in Warning,
Fault, Export Data and Calibration Modes.
8.7
Configure Digital I/O – Warnings and Faults. Many of these will be factory pre-set so if unsure about any
settings then leave as Factory Default.
Select and set level for Alarm Limit to either the Measured Gas or Transmission.
8.8
Go to the Data screen and set the appropriate parameters for ‘Record Result Data’ and ‘Spectrum
Capture’. These will ensure the analyzer stores important information during operation that may be used
to verify operation/status/diagnostics and other trouble shooting.