Yokogawa EJA310E User Manual
Page 68
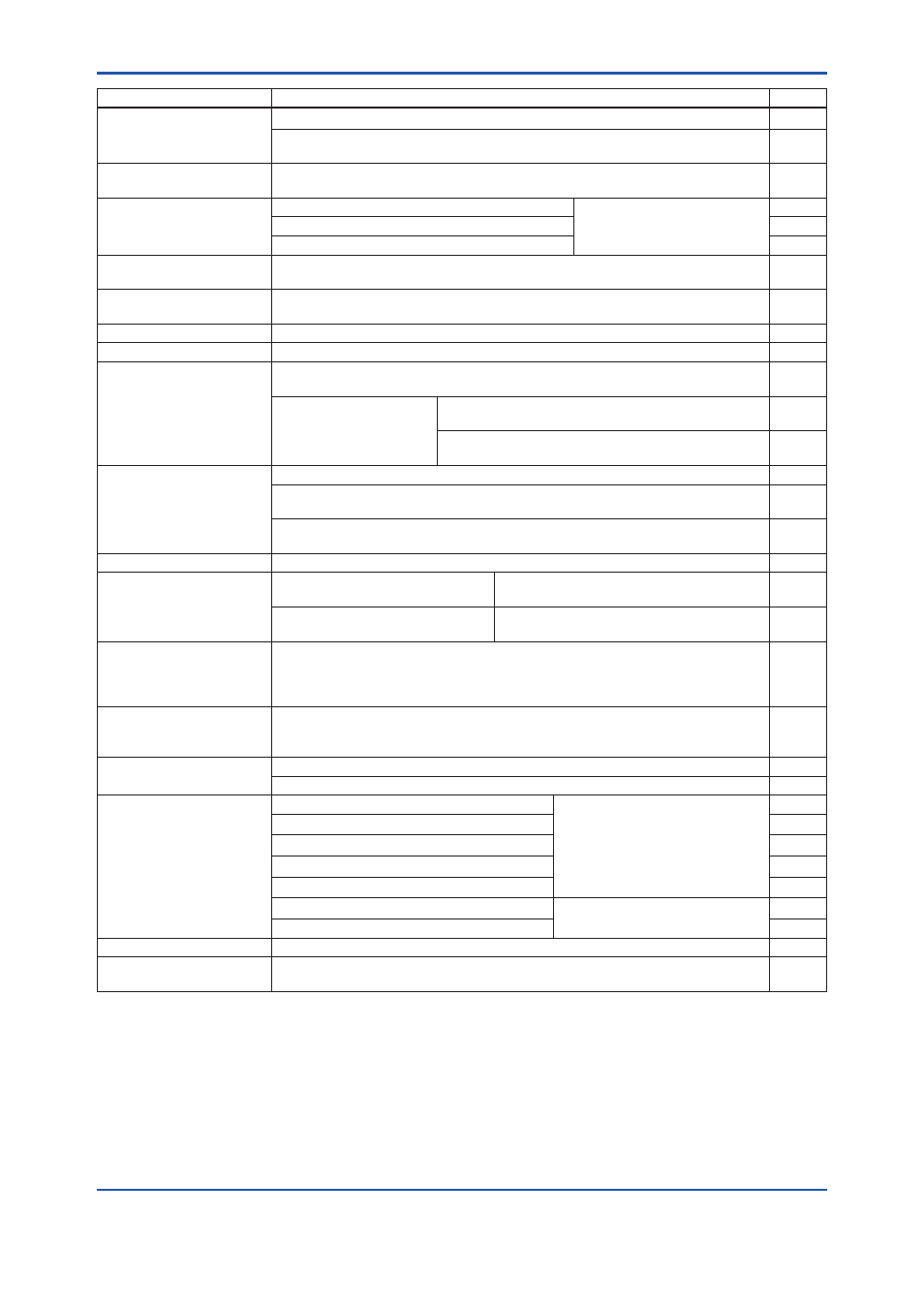
<9. General Specifications>
9-20
IM 01C25B01-01E
Item
Description
Code
Oil-prohibited use with
dehydrating treatment *
4
Degrease cleansing treatment and dehydrating treatment.
K5
Degrease cleansing treatment and dehydrating treatment with fluorinated oilfilled
capsule. Operating temperature –20 to 80°C( –4 to 176°F)
K6
Capsule fill fluid
Fluorinated oil filled in capsule
Operating temperature –20 to 80°C( –4 to 176°F)
K3
Calibration units *
5
P calibration (psi unit)
(See Table for Span and
Range Limits.)
D1
bar calibration (bar unit)
D3
M calibration (kgf/cm
2
unit)
D4
Long vent *
6
Total length: 119 mm (standard: 34 mm); Total length when combining with
Optional code K1, K2, K5, and K6: 130 mm. Material: 316SST.
U1
Gold-plated capsule gasket
*
13
Gold-plated 316L SST capsule gasket. No PTFE is used for wetted parts.
GS
Gold-plated diaphragm *
14
Surface of isolating diaphragm is gold plated, effective for hydrogen permeation.
A1
130 Pa abs calibration *
12
Minimum input puressure at calibration testing: 130 Pa abs (1 mmHg abs)
S1
Output limits and failure
operation *
7
Failure alarm down-scale: Output status at CPU failure and hardware error is
–5%, 3.2 mA DC or less.
C1
NAMUR NE43 Compliant
Output signal limits:
3.8 mA to 20.5 mA
Failure alarm down-scale: Output status at CPU
failure and hardware error is –5%, 3.2 mA DC or less.
C2
Failure alarm up-scale: Output status at CPU
failure and hardware error is 110%, 21.6 mA or more.
C3
Body option *
8
Without drain and vent plugs
N1
N1 and Process connection, based on IEC61518 with female thread on both sides
of cover flange, with blind kidney flanges on back.
N2
N2 and Material certificate for cover flange, diaphragm, capsule body, and blind
kidney flange
N3
Stainless steel tag plate
304SST tag plate wired onto transmitter
N4
Data configuration at
factory *
9
Data configuration for HART
communication type
Software damping, Descriptor, Message
CA
Data configuration for BRAIN
communication type
Software damping
CB
European Pressure
Directive *
10
PED 97/23/EC
Category: III, Module: H, Type of Equipment; Pressure Accessory-Vessel, Type of
Fluid; Liquid and gas, Group of Fluid: 1 and 2
Lower limit of Process and Ambient temperature for EJX110A : –29°C
PE3
Advanced diagnostics *
27
Multi-sensing process monitoring
• Impulse line blockage detection *
28
• Heat trace monitoring
DG6
Material certificate *
15
Cover flange *
16
M01
Cover flange, Process connector *
17
M11
Pressure test/
Leak test certificate
Test Pressure: 16 MPa (2300 psi) *
18
Nitrogen(N
2
) Gas *
25
Retention time: one minute
T12
Test Pressure: 25 MPa (3600 psi) *
19
T13
Test Pressure: 3.5 MPa (500 psi)*
20
T01
Test Pressure: 500 kPa (2000 inH
2
O) *
21
T11
Test Pressure: 50 kPa (200 inH
2
O) *
22
T04
Test Pressure: 32 MPa (4500 psi) *
23
Nitrogen(N
2
) Gas or water *
26
Retention time: one minute
T09
Test Pressure: 50 MPa (7200 psi) *
24
T08
High accuracy type
High accuracy
HAC
High pressure-proof
structure
Maximum working pressure for differential pressure measurement: 25MPa*
29
HG
Contact Yokogawa representative for the codes indicated as ‘-’.
*1:
Applicable for Electrical connection code 2, 4, 7, and 9.
*2:
Applicable for Electrical connection code 2 and 7.
*3:
Not applicable for option code /AL.
*4:
Applicable for Wetted parts material code S, H, M, and T.
*5:
The unit of MWP (Max. working pressure) on the name plate of the housing is the same unit as specified by Option code D1, D3,
and D4.
*6:
Applicable for vertical impulse piping type (Installation code 7) and Wetted parts material code S, H, M, and T.
*7:
Applicable for output signal code D, E and J. The hardware error indicates faulty amplifier or capsule.
*8:
Applicable for Wetted parts material code S, H, M, and T; Process connection code 3, 4, and 5; Installation code 9; and Mounting
bracket code N. Process connection faces on the other side of zero adjustment screw.