General information, Optional pressure switch unit, 5/2-way double valves with c – Ross Controls CATEGORY 4 - 5_2 VALVES CROSSMIRROR SERIES 77 User Manual
Page 8: Sensing, Schematic (valve in the de-actuated position), Ross, Irror
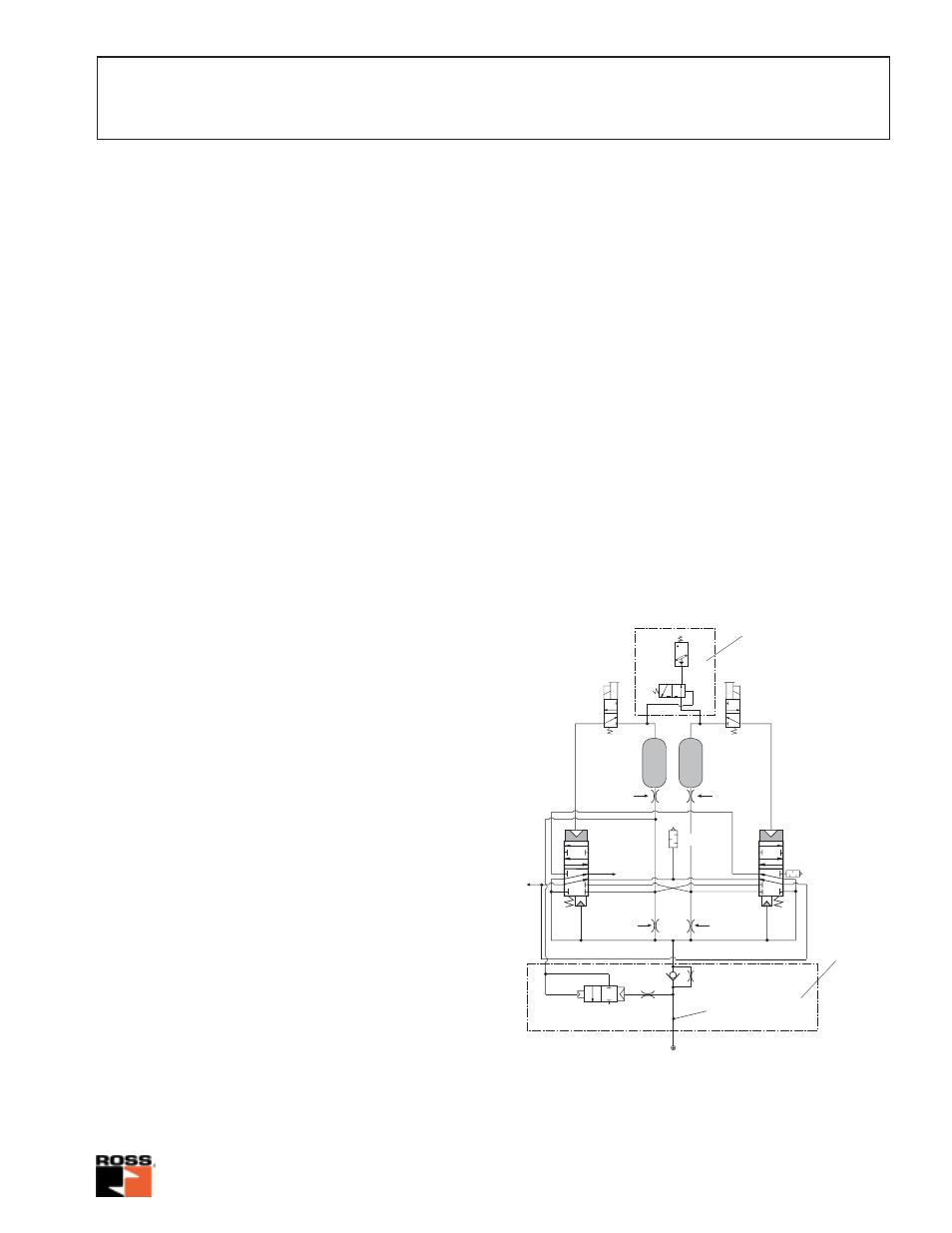
8
www.rosseuropa.com
GENERAL INFORMATION
Pressure Switch Unit (optional)
In case of a valve malfunction, the standard valve
shifts back to the at-rest-position; i.e. pressure
from port 1 to port 2. By actuating the valve again,
the cause of the malfunction (dirt or asynchronous
signals) can be eliminated and the valve can
operate normally again. In order to detect such a
malfunction, a valve with pressure switch unit is
available.
This pressure switch unit can be used to signal a
malfunction and to interrupt valve piloting. Properly
wired into the electric circuit, the pressure switch
can prevent a new valve cycle until the malfunction
has been analyzed and eliminated.
The new ROSS 5/2-way
C
ROSS
M
IRROR
®
double
valve is designed as a self-monitoring valve. It can
be used for controlling pneumatic presses for cold-
forming of metal (optionally in connection with addi-
tional devices such as pilot-operated check valves),
if the electric control of the valve is designed in
accordance with prEN..."Pneumatic Presses" (June
1998). The mirror-image-type air flow pattern in the
C
ROSS
M
IRROR
®
double valve allows an alternating
pressure buildup from the de-actuated (pressure
port 1 to work port 2) to the actuated mode (pressure
port 1 to work port 4) only if the following conditions
are fulfilled:
1. The solenoid control signals must actuate the
solenoid pilot valves synchronously or with a time
difference of < 0,5 sec.
2. Both main valve systems must be in the at-rest
position before the valve is actuated.
3. Both main valve systems must have moved into
the actuated position within a defined time span of
< 0,5 sec.
Additional work-safety features are incorporated in
the base:
1. A check valve in the inlet port prevents the cylin-
der from falling abruptly when a loss of pressure
occurs. In such a case a small bypass will allow the
cylinder to move gradually into the at-rest-position.
2. When an unexpected loss of pressure occurs with
the electric pilot signal still being present, another
valve integrated in the sub-base is designed to
prevent any uncontrolled valve shifting and cylinder
movement that might occur when the pressure
returns. In case of a pressure loss this valve opens
the pilot air line and thereby prevents the main valve
system from shifting when pressure returns. All pilot
valves and main valve systems must be in the at-
rest-position before a restart of the system after a
pressure loss.
Schematic
(Valve in the de-actuated position)
5/2-Way Double Valves
with C
ROSS
M
IRROR
®
-Sensing
A5
A4
A3
A2
A1
A7
A8
A6
1A
1B
2B
2A
B2
B8
B7
B6
B1
B3
B4
A
B
P5
2
1
3
12
2
1
3
12
B5
N
O
Q
Pressure switch unit
(optional)
CHAMBER "A"
CHAMBER "B"
EXH. 5
EXH. 3
OUTLET 2
OUTLET 4
Pressure Port 1
AIR SUPPLY
Sub-base with
pressure failure
monitoring