LEESON Permanent Magnet AC Motors User Manual
Page 7
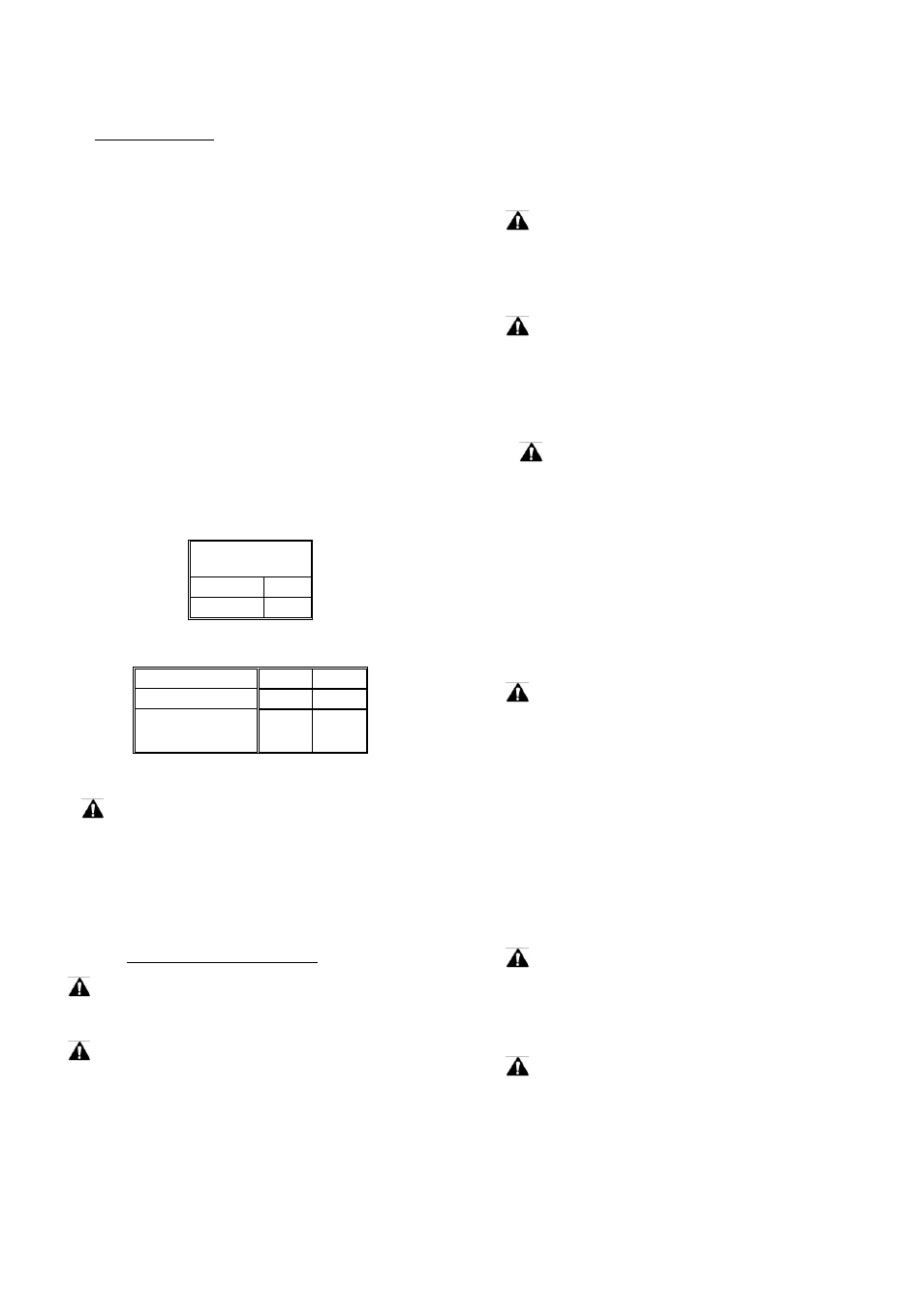
3.3.6.4
Thermal Protection
General Information: When thermal protection is provided,
“WITH OVERHEAT PROTECTIVE DEVICE” will be stamped on
the nameplate. The motor is provided with an overheat
protective device that does not directly open the motor circuit.
Motors nameplated with this phrase have either thermostats,
thermisters or RTDs. The leads to these devices are routed into
the motor conduit box or into an auxiliary box. The lead markings
are defined on the nameplate.
THERMOSTAT: The circuit controlled by the thermostats must
be limited to a maximum of 600 volts and 360 volt-amps. See
connection decal provided inside the terminal box cover. Failure
to connect these over temperature devices (when provided) will
void the motor warranty.
THERMISTERS OR RESISTANCE TEMPERATURE
DETECTORS (RTDs)
These sensors are to be connected to a solid state resistance
monitoring device designed for use with thermistors or RTDs
Failure to connect these over temperature devices (when
provided) will void the motor warranty.
3.3.6.5
RTD Alarm & Trip Settings
Tables 3-6 & 3-7 are suggested initial RTD alarm and trip
settings. For motors found to operate significantly below these
values the settings may be reduced accordingly.
Table 3-6 Winding RTD – Temperature Limit (
8888
C)
40
8888
C Max Ambient
Temperature
(degrees C)
Alarm
Trip
130
140
Table 3-7 Bearing RTD – Temperature Limit (
8888
C)
40
8888
C Max Ambient
Bearing Type
Alarm
Trip
Standard bearings
110
115
Motors specified
with heat stabilized
bearings to 150 C
130
135
3.3.7
GUARDS
WARNING:
ROTATING PARTS HAZARD
When devices are assembled to the motor shaft, be sure to install
protective devices such as belt guards, chain guards, and shaft
covers. These devices must protect against accidental contact with
extremities, hair, and clothing. Consider the application and provide
guarding to protect personnel. Remove all unused shaft keys and
loose rotating parts to prevent them from flying off and causing
bodily injury. Failure to follow this warning could result in serious
personal injury, death and/or property damage.
3.4
ELECTRICAL CONNECTIONS
WARNING:
ELECTRICAL HAZARDS
Before proceeding read Section 1.1 on Electrical Safety. Failure to
follow the instructions in Section 1.1 could result in serious personal
injury, death and/or property damage
WARNING:
ELECTRICAL SHOCK HAZARD: Voltage may
be present at the motor terminals even after the motor has stopped
rotating. To assure there is no voltage at motor, remove input power
from VFD and follow VFD manufacture documentation for voltage
decay time before servicing motor. Failure to follow this instruction
could result in serious personal injury or death.
NOTICE: MOTOR NOT SUITED FOR OPERATION ON LINE
POWER
Permanent magnet motors can only be properly operated by a
variable frequency drive (VFD). Attempting to run in bypass mode
(across the line) may cause motor damage.
3.4.1
POWER SUPPLY / BRANCH CIRCUIT
WARNING:
POWER SUPPLY INCOMPATIBILITY
HAZARD
Check power supply to make certain that voltage, frequency and
current carrying capacity are in accordance with the motor
nameplate and VFD. Connecting the VFD to the wrong power
source could result in serious personal injury, death and/or property
damage.
WARNING:
BRANCH CIRCUIT SUPPLY HAZARD
Motor and control wiring, fusing, overload protection, disconnects,
accessories and grounding must always conform to the applicable
electrical codes as well as local codes and sound practices.
3.4.1.1
Fuses, Breakers, Overload Relays
Consult variable frequency drive (VFD) operating manual and
applicable electric codes for branch circuit protection sizing.
WARNING:
PROTECTIVE DEVICE DISABLED HAZARD
DO NOT bypass or disable these or other protective devices.
Protection removal could result in serious personal injury, death
and/or property damage.
3.4.1.2
AC Power Supply Limits
PM motors are designed to operate with variable frequency
drives with rated input voltage 600 VAC or less. Drive RMS
output voltage should not exceed motor nameplate voltage for
which the motor is connected
.
NOTICE:
REDUCED MOTOR PERFORMANCE
Operation outside of these limits will degrade motor performance
and increase operating temperature.
3.4.2
TERMINAL BOX
WARNING:
ELECTRICAL SHOCK HAZARD
Shaft rotation produces voltage in PM motors even when motor is
disconnected from power source. Do not open terminal box or
touch unprotected terminals while the motor shaft is rotating.
Failure to do so may cause serious injury or death to personnel.
3.4.2.1
Conduit Opening
For ease of connections, motors are typically provided with large
terminal boxes. Most motors have conduit access in 90 degree
increments, the terminal box conduit opening is typically provided
via knockouts, holes with covers, or the terminal box is rotate-
able. Fabricated conduit boxes may have a removable plate for
the installer to provide correctly sized hole(s).
3.4.3
LEAD CONNECTIONS
Electrical connections are to be made per nameplate connection
diagram or separate connection plate.
In making connections follow
the applicable electrical code as well as local codes and practices.
WARNING:
ELECTRICAL CONNECTION HAZARD
Failure to correctly connect the motor leads and grounding
conductor can result in serious personal injury or death. Motor lead
connections can short and cause damage or injury if not well
secured and insulated.
3.4.4
GROUND CONNECTION(S)
WARNING:
ELECTRICAL GROUNDING HAZARD
For general information on grounding (USA) refer to NEC Article
250. Improper grounding of an inverter fed motor may result in
frame voltages in excess of 500 Volts. In making the ground
connection, the installer must make certain that a good electrical
connection is obtained between motor and grounding lead. Failure
to properly ground motors, per the applicable national code (such
as NEC Article 430) and local codes may cause serious injury or
death to personnel.