LEESON Permanent Magnet AC Motors User Manual
Page 4
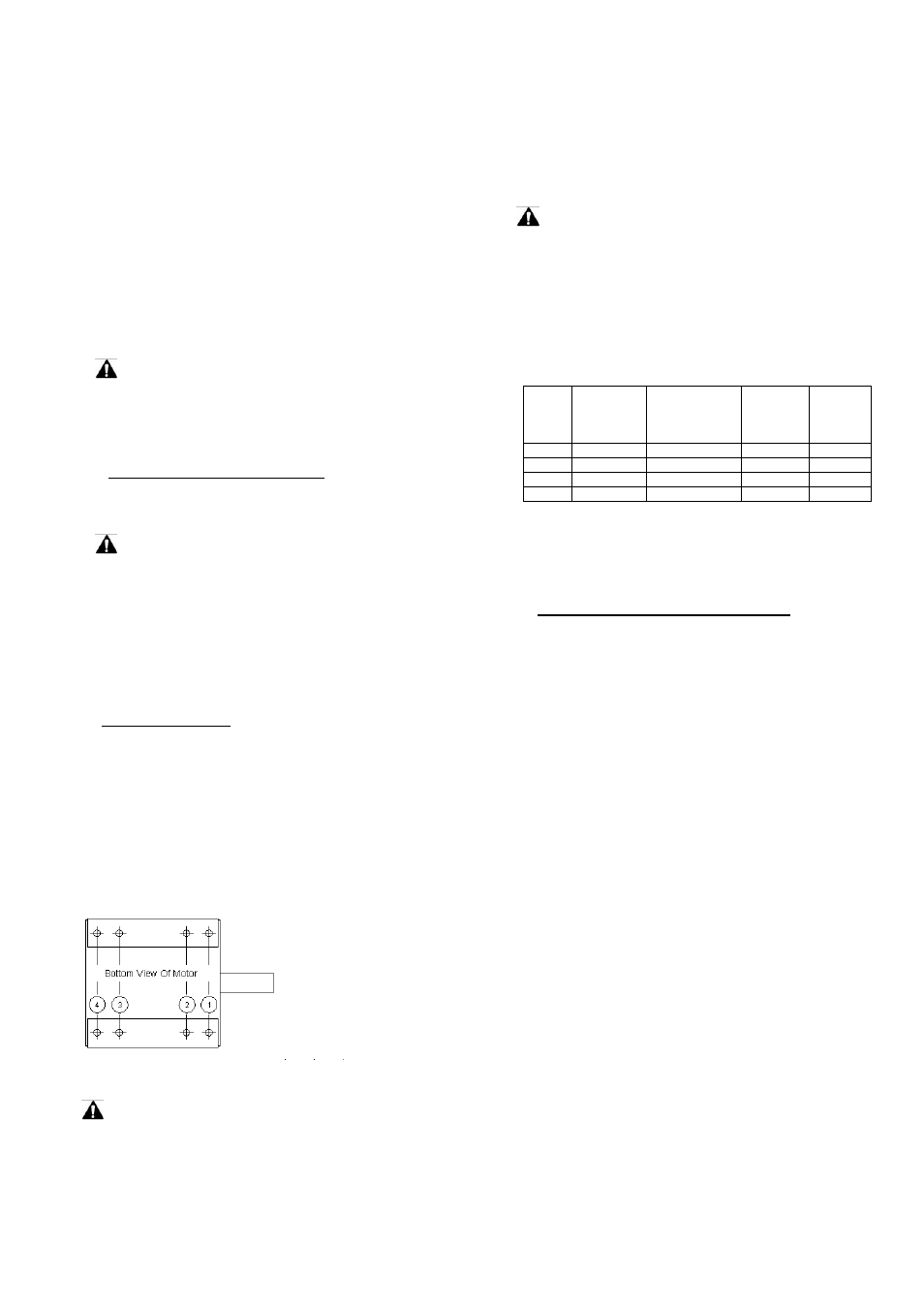
3.1.3
CONSTRUCTION SELECTION PER LOCATION
3.1.3.1
TOTALLY ENCLOSED MOTORS are suitable for
indoor or outdoor standard service applications. Severe duty
construction is recommended for severe service applications.
TEAO or AOM (Totally Enclosed Air Over) motors must be
mounted in the air stream. When the motor nameplate states
a minimum airflow the motor must be mounted in an air
stream meeting this minimum value.
TEFC (Totally Enclosed Fan Cooled) motors must meet a
minimum distance equal to ½ the shaft height between the
fan guard grill openings and the nearest obstruction.
3.1.3.2
HAZARDOUS LOCATIONS MOTORS: Not all
motors covered by this manual are intended for hazardous
duty locations. Motors intended for hazardous duty locations
are labeled with the division and class.
WARNING:
HAZARDOUS LOCATIONS
Hazardous Locations motors are intended for installations in
accordance with NEC Article 500. For all installations involving
Hazardous Locations motors, consult the applicable national
codes, local codes, and the authority having jurisdiction. Failure
to do so may cause serious injury or death to personnel.
Division 2 Installations – Class I only: Use only motors
that are CSA Certified and bear the CSA Certification Mark.
These motors include a phrase on the main motor
nameplate that indicates the motor is CSA Certified for Class
I, Division 2 / Zone 2 locations.
WARNING:
EXPLOSION HAZARD
A motor should never be placed in an area with a hazardous
process or where flammable gases or combustible materials
may be present unless it is specifically designed and
nameplated for this type of service. Hazardous Locations
motors are intended for installations in accordance with NEC
Article 500. For all installations involving Hazardous Locations
motors, consult the NEC, local codes, and the authority having
jurisdiction. Failure to follow these instructions could result in
serious personal injury, death and/or property damage. (For
other limitations see section 1.3).
3.2
MOUNTING MOTOR
3.2.1
RIGID BASE (FOOTED):
The motor must be
securely installed to a rigid foundation or a mounting surface to
minimize vibration and maintain alignment between the motor
shaft and the load’s shaft. The mounting surfaces of the four
mounting pads must be flat within 0.01 inches for 210 frame &
smaller; 0.015 inches for 250 frame & larger. [IEC 0.25 mm for
130 frame & smaller, 0.38 mm for 160 frame & larger]. This may
be accomplished by shims under the motor feet. For special
isolation mounting, contact manufacturer for assistance.
3.2.2
RIGID BASE HOLE SELECTION -6 OR 8 HOLES
3.2.3
VERTICAL MOUNTING
WARNING:
FALLING OBJECT HAZARD
The lifting provision on standard horizontal footed motors is not
designed for lifting the motor in a vertical shaft up or shaft down
position. (see Diagram 2.2.1). Doing so may cause the motor to
fall. Lifting method / provisions for mounting a rigid base (footed)
motor vertically is the responsibility of the installer.
VERTICAL SHAFT DOWN: Most standard horizontal motors
through 449 Fr. (excluding brake motors) can be mounted in a
vertical shaft down orientation. For vertical brake motors see
section 3.3.6.2.
VERTICAL SHAFT UP:
WARNING:
HAZARDOUS LOCATIONS VERTICAL
MOUNT: Hazardous locations motors must NOT be mounted
vertically shaft up without approval by the motor manufacturer.
Without proper retaining provisions the rotor may move axially
and contact components, creating a spark hazard.
Belted or Radial Load when mounted vertically
: The
following frame sizes / constructions with applied (axial) down
loads within the limit stated are acceptable when mounted vertical
shaft up.
Table 3-1 Belted or Radial Load Applications (All speeds)
Frame
Size
Enclosure
Construction
Shaft Up
OK
Max
Applied
Down
Load2
180
TEFC
All
Yes
35 lbs
210
TEFC
All
Yes
40 lbs
250
TEFC
All
Yes
40 lbs
280
TEFC
Cast Iron
Yes
30 lbs
Notes:
The max applied down load is any applied load external to the
motor, including such things as sheave weight, fan loads, axial
belt force, pump load, etc. If the application is direct drive with
no applied radial load or is beyond the limits listed, consult the
motor manufacturer.
3.3
APPLICATION ASSEMBLY TO MOTOR
NOTICE:
EQUIPMENT DAMAGE
Do not connect or couple motor to load until correct rotational direction
is established.
3.3.1
GENERAL: PROPER ALIGNMENT
of the motor
and driven equipment minimizes vibration levels, maximizes
bearing life, and extends the overall life of the machinery. Consult
the drive or equipment manufacturer for more information.
NOTICE:
BEARING FAILURE
During assembly do NOT force components onto the shaft.
Striking or hammering the component may result in bearing
damage.
3.3.2
DIRECT COUPLING:
Use flexible couplings if
possible.
For applications that apply radial, axial or moment loading on the
motor shaft see section 3.3.3.
NOTICE:
BEARING FAILURE
Unless approved by the motor manufacturer, do NOT direct
couple a vertical shaft up motor or roller bearing motor. Direct
coupling a vertical shaft up motor or a motor with a roller bearing
may result in bearing damage.
3.3.3
DIRECT CONNECTED:
Radial loading for direct
connected equipment (gears, fans etc.) must be approved by the
motor manufacturer unless within the maximum overhung load
limits (Table 3-2). Combined loading (axial, radial and/or
moments) must be approved by motor manufacturer. For belted
loads see section 3.3.4.
Location 1 and 3 holes for short frame:
(NEMA) 182, 213, 254, 284
(IEC) 112S, 132S, 160M, 180M
Location 2 holes are for F1,
F2 Conversion (if provide)
Location 1 and 4 holes for long frames:
(NEMA) 184, 215, 256, 286
(IEC) 112M, 132M, 160L, 180L