KB Electronics KBRG-255 User Manual
Page 16
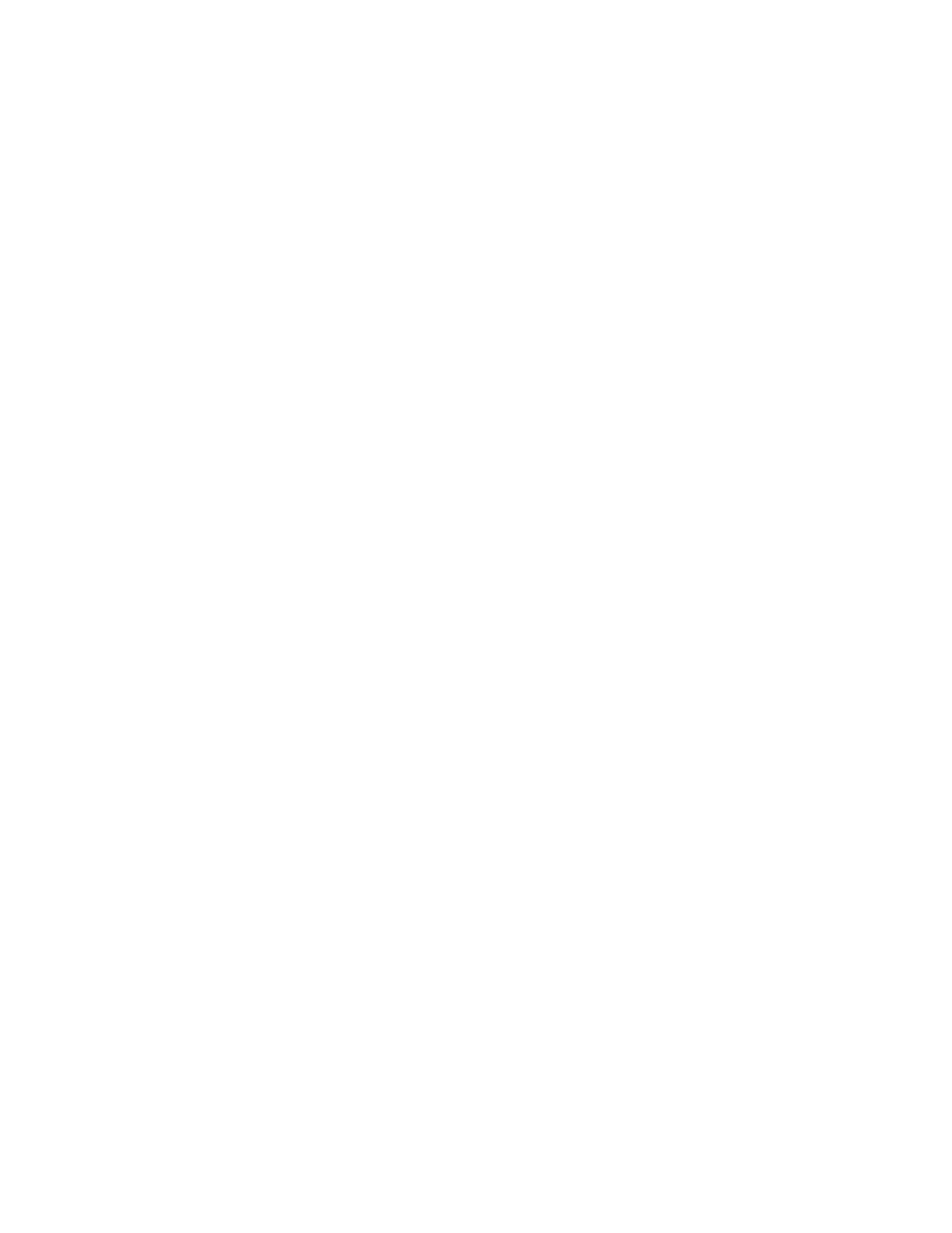
12
C. Deadband (DB) – The DB trimpot sets the amount of main speed potentiometer rotation
required to initiate control voltage output. It is factory adjusted to approximately 25% of
rotation.
The DB trimpot also determines the amount of delay that will occur before regeneration
starts. (Regeneration occurs when the applied load torque is in the same direction as the
motor rotation.)
To readjust the DB to factory setting:
i.
Set Main Speed pot to zero speed position.
ii.
Set DB trimpot to full CCW position.
iii. Adjust DB trimpot CW until motor hum is eliminated.
(See fig. 10, p. 11 for graphic illustration of the DB trimpot.)
Note: If the deadband trimpot is set too low (CCW direction), the motor may oscillate
between forward and reverse. Adjust deadband trimpot CW until the instability
disappears. (Oscillation may also occur due to response setting. See section VIII, G, p.
13.)
D. Forward Current Limit (FWD CL) and Reverse Current Limit (REV CL) Trimpots –
These trimpots are used to set the maximum amount of DC current that the motor can
draw in both the forward and reverse directions. The amount of DC current determines
the amount of maximum motor torque in both the Speed Control Mode and Torque Control
Mode. They are factory set at 150% of the rated current (38.0 ADC).
Readjust the CL trimpots as follows:
i.
Turn CL trimpot to MIN (CCW) position.
ii.
Wire in a DC ammeter in series with armature lead. Lock shaft of motor.
iii. Apply power. Rotate CL trimpot CW until desired CL setting is reached (factory
setting is 1.5 times rated motor current). Be sure control is in Forward direction for
FWD CL trimpot adjustment and likewise with REV CL.
WARNING! Do not leave motor shaft locked for more than 2 – 3 seconds to prevent
motor damage.
CAUTION: Adjusting the CL above 150% of motor rating can cause overheating and
demagnetization of some PM motors. Consult motor manufacturer.
E. IR Compensation (IR Comp) – The IR Comp is used to stabilize motor speed under
varying loads. (Note: If control is in Tach Feedback mode, the IR Comp should be set
to minimum - CCW.)
Readjust the IR Comp trimpot as follows:
i.
Run motor at approximately 30-50% of rated speed under no load and measure actual
speed.
ii.
Load motor to rated current. Rotate IR Comp trimpot so that loaded speed is the
same as the unloaded speed measured in the previous step.
Control is now compensated so that minimal speed change will occur over a wide range
of motor load. [Note: Too much IR Comp will cause unstable (oscillatory) operation.]
F. Maximum Speed (MAX) – The MAX trimpot is used to set the maximum output voltage
of the control which, in turn, sets the maximum speed of the motor. In the Torque Control
Mode, the MAX trimpot setting determines the unloaded motor speed.
Adjust the MAX trimpot as follows:
i.
Rotate Main Speed potentiometer to full speed (CW).
ii.
Adjust MAX trimpot to desired maximum motor speed.
(Note: Do not exceed maximum rated RPM of motor since unstable operation may result.)