Introduction, Typical operation and requirements – General Pump Pump Installation and Service Manual User Manual
Page 2
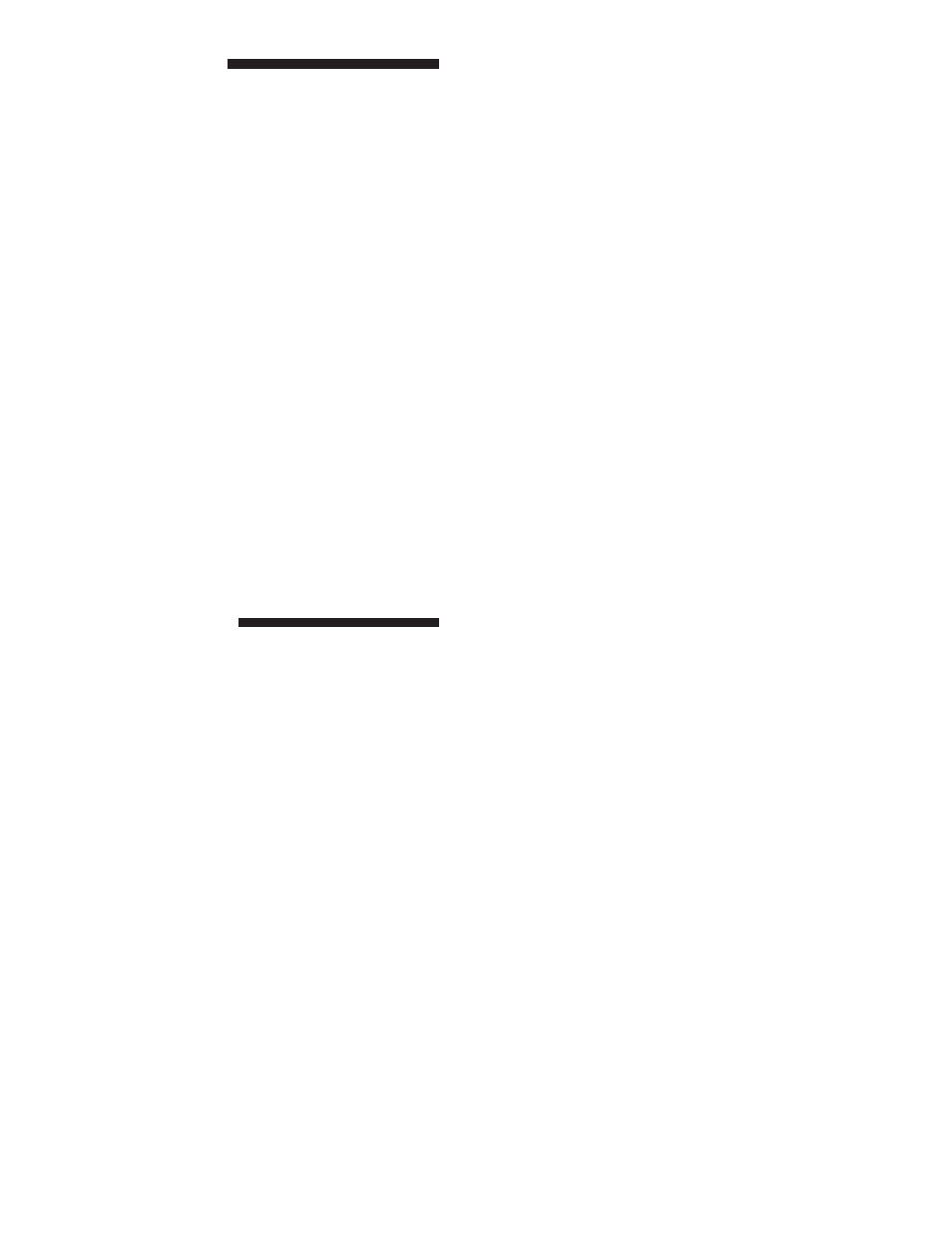
INTRODUCTION
Thank you for purchasing a GENERAL PUMP Pressure
Washer Pump. With proper installation and maintenance
it will provide you with many years of dependable,
trouble-free service.
This manual was developed as a basic guide to
understanding the operation and requirements,
installation, and servicing of GENERAL PUMP positive
displacement pumps.
Pressure cleaning equipment is potentially hazardous
and could cause personal injury or property damage if
installed, repaired, or operated in an unsafe manner, or in
a manner which is not consistent with the manufacturer’s
recommendations or requirements.
There are many manufacturers of pressure washer
pumps and complementary components. Be sure that the
required components you choose to use are consistent
with the high quality standards of GENERAL PUMP
pumps.
GENERAL PUMP does not assume liability or
responsibility for the design of a customer’s high
pressure system.
TYPICAL OPERATION AND
REQUIREMENTS
PRESSURE
The pressure produced in a pressure washer
system is the result of forcing a known volume
(or flow) of water through a known size orifice
(spray tip). Pressure is measured in pounds per
square inch (PSI).
FLOW
The flow or volume produced in a pressure washer
system is determined by the speed that the pump
shaft is rotated (RPM). The faster the shaft is
rotated, the higher the output volume. Flow or
volume is measured in gallons per minute (GPM).
The pump, which is driven by an electric motor or a gas
engine, draws or accepts filtered water in through a se-
ries of inlet check valves as the plungers move back. As
the plungers move forward, the inlet valves close, forcing
the water to travel through a series of outlet check valves,
and to the outbound side of the pump.
After the water exits the pump, its flow direction must be
controlled with an unloading or regulating valve. A
positive displacement pump is always delivering a
certain volume of water whether the spray gun is open
or closed, therefore a device is needed to control the di-
rection of flow, either allowing the flow to go through the
open spray gun, or redirecting (by-passing) the flow back to
the inbound side of the pump when the spray gun is closed.
Without an unloading or regulating valve, dangerously high
pressures will be produced when the spray gun is closed
because the water being forced out of the pump has no
place to go. Serious bodily injury or property damage could
be caused by failure to properly utilize an appropriate un-
loader or regulator valve in your pressure washer system.
As a safety device, at least one pressure relief valve should
be installed in the outbound side of the pump to guard
against failure of component parts, and the development of
dangerously high pressures.
Cleaning chemicals or detergents may be introduced into
the flow of water either inbound or outbound of the pump.
An inbound or upstream type of chemical injector simply
uses the pump’s ability to draw or suck fluid in to introduce
a chemical into the stream of water. Care must be taken to
avoid introducing any chemicals which are not compatible
with the materials in the pump and downstream compo-
nents. An upstream injector does allow chemicals to be ap-
plied to the work surface at the normal high working
pressure of the system. An outbound or downstream type of
chemical injector uses a venturi (very similar to that used in
an automotive carburetor) to draw a chemical into the water
stream. A downstream injector requires low pressure to ac-
tivate chemical flow. Low pressure is achieved by chang-
ing to a large sized spray tip, or opening up a large orifice
at the outlet end of the spray gun using an adjustable noz-
zle or a double lance. There are several advantages to
using a downstream injector over using an upstream type.
1. Fewer component parts are exposed to the cleaning
chemicals, extending system life.
2. The operator can control the flow of chemical (on and
off) by changing the system pressure at the nozzle.
3. Applying chemical at low pressure is more
economical because less chemical bounces off the
work surface.
Heated pressure washers and steam cleaners increase
the ability of a high pressure flow of water to break down
dirt and grease. They also increase the action of most
cleaning chemicals. These systems are very comples,
and add more potential personal injury and property
damage hazards. Design of these systems requires many
more additional components as well as experienced de-
sign personnel with knowledge of fuels, heat transfers,
electronics, etc.
2