FEC AFC1200 User Manual
Page 7
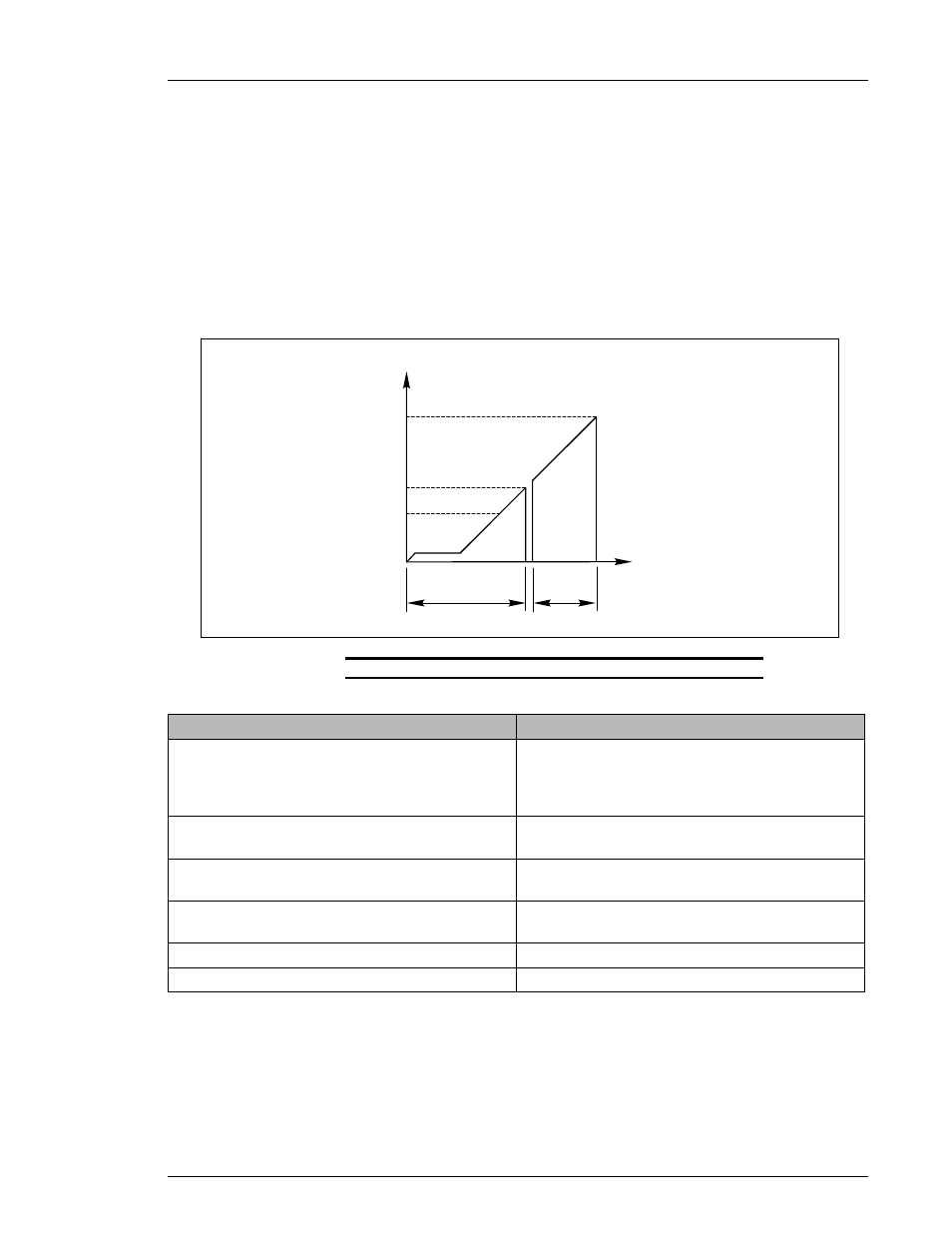
)(& ,QF
Maximum allowable Final Step time
FINAL STEP (TIME)
Maximum allowable fastening cycle time
1ST STEP (TIME)
Engineered fastening specification for rotation
angle
FINAL ANGLE
30 ~ 50% of resultant torque for Hard joints
50 ~ 90% of resultant torque for Soft joints
SPEED CHANGE (TORQUE)
Engineered fastening specification at which Angle
Control begins
THRESHOLD 2 (TORQUE)
30 ~ 50% of FINAL ANGLE or resultant torque for
Hard joints
50 ~ 90% of FINAL ANGLE or resultant torque for
Soft joints
1ST TORQUE/ANGLE
RECOMMENDATION
FUNCTION
P Two-step fastening will be used primarily for joints that have a requirement to
synchronize with another spindle during the final stage of the rundown (connecting
rod, main bearing cap and any other multiple-spindle unit, for example).
P The System will fasten to the 1ST TORQUE/ANGLE during the specified 1ST
STEP time. Once either SPEED CHANGE TORQUE or 1ST TORQUE/ANGLE is
reached, the System will switch to the specified TORQUE SPEED (Section 6.3).
When all fasteners have reached 1ST TORQUE/ANGLE, the spindles will
synchronize and then rotate simultaneously the specified number of degrees from
THRESHOLD 2 TORQUE to FINAL ANGLE within the specified FINAL STEP time.
STD.
TORQUE
1ST STEP
FINAL
STEP
ANGLE
SPEED CHANGE
1st TORQUE
FIG. 6-1-2b Angle Control Functions for Two-Step Fastening
Chapter 6: Fastening Instructions
Page 6-7