FEC AFC1200 User Manual
Page 6
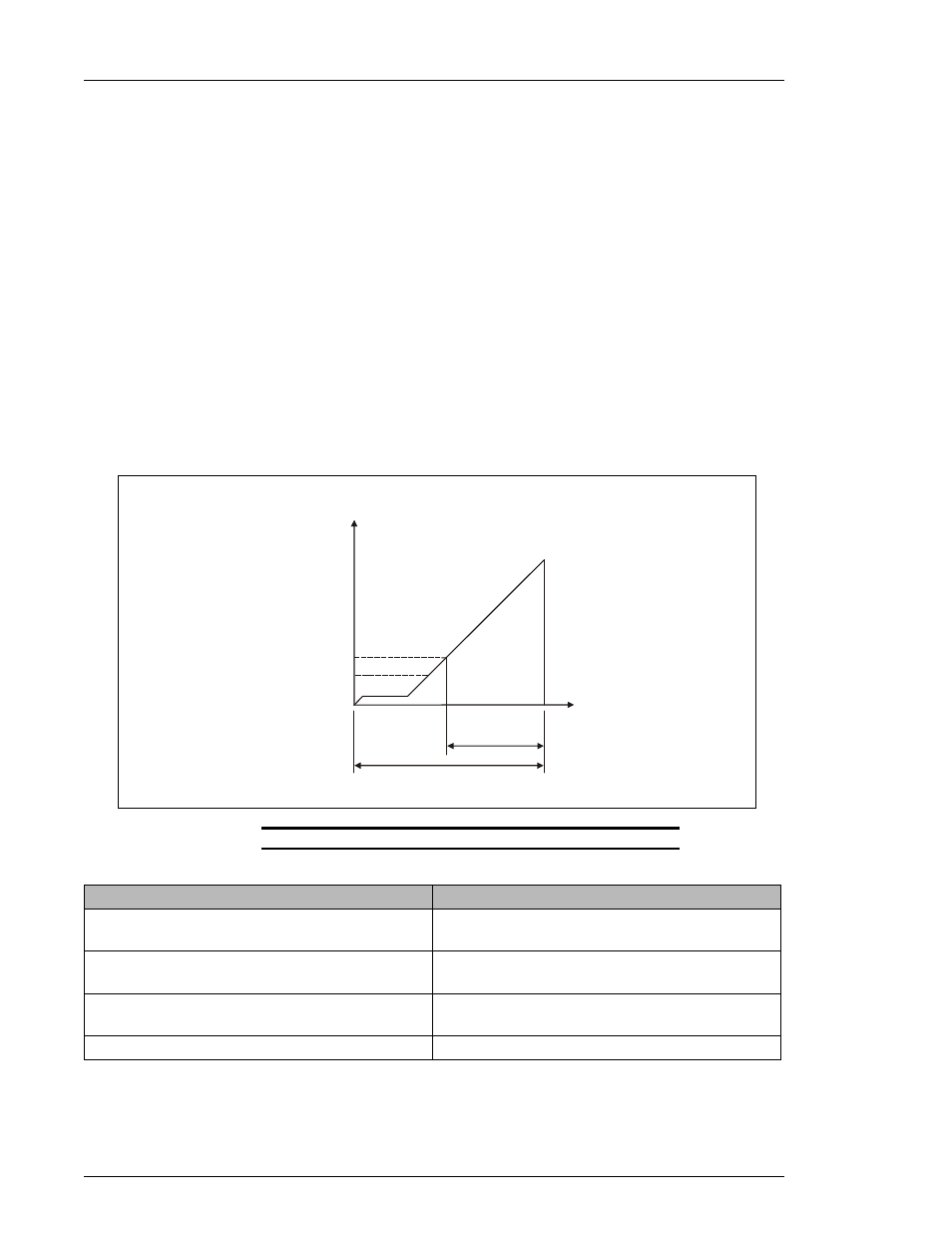
)(& ,QF
4 incremental steps that will successively secure the fastener to a specified torque or angle
value before attaining the final number of degrees of rotation. Angle Control is used primarily
when greater control of clamp load is required (connecting rods, main bearing caps and
cylinder heads, for example).
w One-Step Fastening
P After presetting the fastening sequence (Section 7.5 SET SEQUENCE) to perform
a single-step fastening, the System fastening parameters (Section 7.1
PARAMETER SET ) must be configured according to the Engineered fastening
specification.
P One-step fastening will be used primarily for joints that have no requirement to
synchronize with another spindle during the final stage of the rundown (pipe plugs
and other single-spindle applications, for example.)
P The System will fasten to the FINAL ANGLE value during the specified 1ST STEP
time. Once SPEED CHANGE TORQUE is reached, the System will switch to the
specified TORQUE SPEED (Section 6.3). Once THRESHOLD 2 TORQUE is
reached, the System will rotate the fastener the number of degrees specified by
FINAL ANGLE.
TORQUE
FINAL
ANGLE
1ST
STEP
ANGLE
THRESHOLD 2 TORQUE
SPEED CHANGE
FIG. 6-1-2a Angle Control Functions for One-Step Fastening
Maximum allowable fastening cycle time
1ST STEP (TIME)
Engineered fastening specification for rotation
angle
FINAL ANGLE
30 ~ 50% of STD for Hard joints
50 ~ 90% of STD for Soft joints
SPEED CHANGE (TORQUE)
Engineered fastening specification at which Angle
Control begins
THRESHOLD 2 (TORQUE)
RECOMMENDATION
FUNCTION
w Two-Step Fastening
P After presetting the fastening sequence (Section 7.5 SET SEQUENCE ) to perform
a two-step fastening, the System fastening parameters (Section 7.1 PARAMETER
SET) must be configured according to the Engineered fastening specification.
Chapter 6: Fastening Instructions
Page 6-6