Commissioning and operation – SPP Pumps Instream User Manual
Page 6
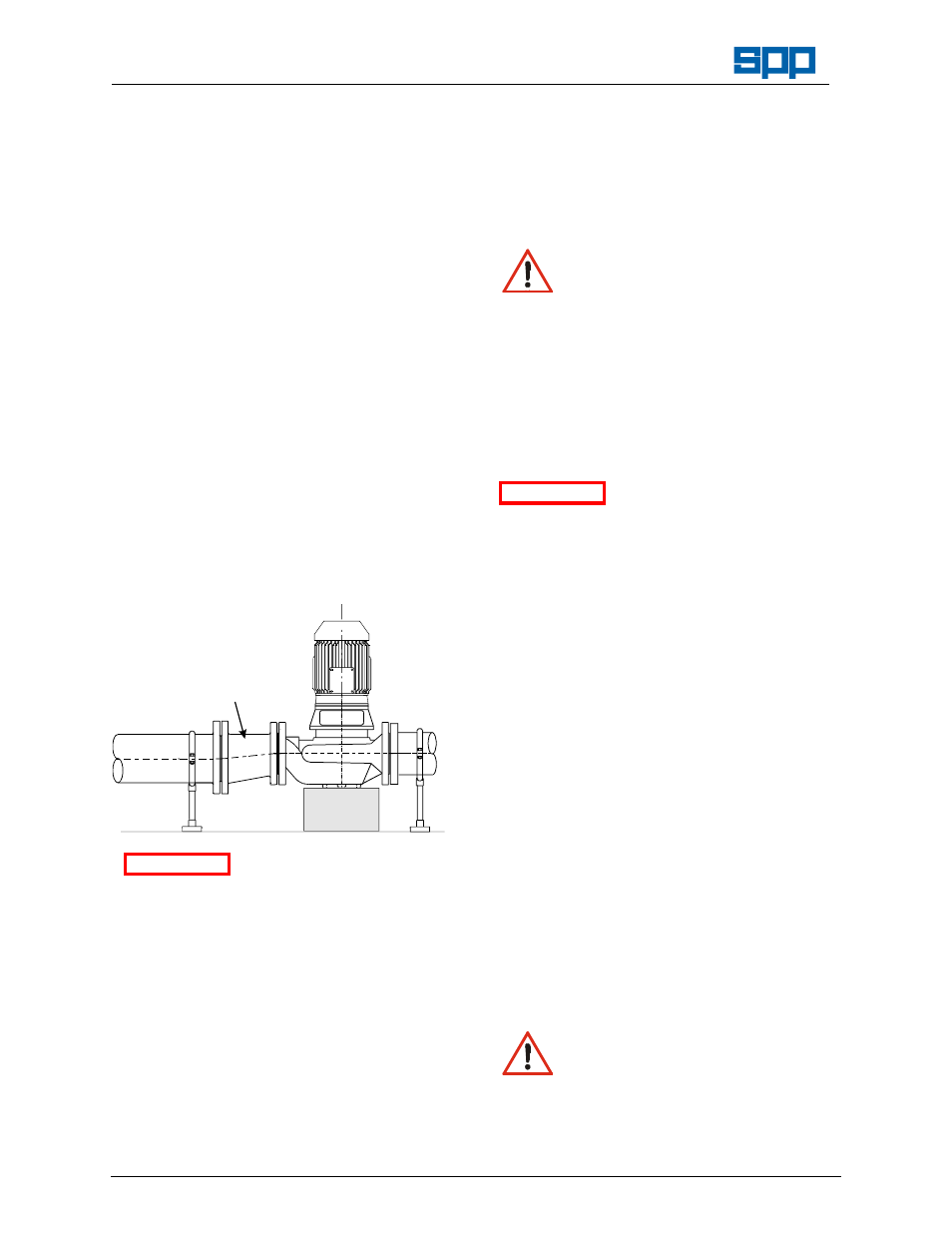
Manual No/Rev
W23-001E / 8
Operators Instructions for
Instream Centrifugal Pumps
Our policy is one of continuous improvement and we reserve the right to alter specifications at any time
Page 6 of 16
to prevent foreign matter from being drawn
into the pump. A screen or basket strainer
may also be required to hold back larger
items. These should be sized to maintain the
flow through them to below 0.6 m/s.
The suction pipe work must be flushed clean
to ensure that site debris is not drawn into the
pump when it is commissioned.
4.6
Discharge Pipework
The bore of the discharge pipe should be
sized to ensure a flow velocity of 2.5 to 3 m/s
is not exceeded. This is usually one size larger
than the discharge branch. Pipework should
be as short and straight as possible to reduce
friction head loss.
A non-return valve is usually fitted to prevent
the pump from excessive back pressure and
reverse rotation and a discharge valve is
usually fitted to regulate the flow and allow for
inspection and maintenance on the pump.
The suction and discharge pipework must be
independently supported and positioned such
that no excessive forces and moments are
exerted on the pump flanges.
Preferred Pipework
INSTPIP1.WMF
Eccentric Reducer
Failure to support suction
and
delivery
pipework
may result in distortion of the pump casing,
with the possibility of early pump failure.
4.7
Foundations
The pump must be secured to substantial
foundations to minimise vibrations. After the
pump has run for about 200 hours, the
foundation bolt should be checked for
tightness.
The pump must be secured to substantial
foundations to minimise vibrations. After the
pump has run for about 200 hours, the
foundation bolt should be checked for
tightness.
5. Commissioning and Operation
5.1
Commissioning Checks
These checks must be done after first
installation and after pump maintenance that
required removal of the rotating assembly.
Abrasion and Entrapment Hazard
Do NOT touch any moving or
rotating parts. Guards are provided
to prevent access to these parts, where they
have been removed for maintenance they
MUST be replaced before operating the
equipment.
Check that the rotating assembly is free to
rotate by hand before connecting the power
supply. Also check that the piping system has
been properly connected with all joints
tightened and instrumentation is in position.
Check that the pump is
primed.
Pumps
should
never be run dry as the pumped liquid acts as
a lubricant for the close running fits
surrounding the impeller and damage will be
incurred.
Prime the pump using an ejector, exhauster or
vacuum pump. If a foot valve is used in the
suction line the pump may be primed by
venting and filling the casing with liquid. Open
the air release valve to bleed any air trapped
in the sea housing, as the seal must be
lubricated and dry running may contribute to
premature seal failure.
Connect the electrical supply to the pump unit.
Momentarily switch on motor and check
direction of rotation. This should be such that
the pump assembly turns clockwise when
viewed on the driven end. For three phase
electric motors, if direction of rotation is
incorrect, disconnect the supply and change
over two of three supply wires.
5.2
Starting Procedure
BEFORE AN INSTREAM PUMP IS STARTED
ALWAYS ENSURE THAT THE SUMP IS FILLED
TO THE CORRECT LEVEL WITH LIQUID, AND
THAT
ANY
LEVEL
CONTROLS
ARE
FUNCTIONING CORRECTLY.
Abrasion and Entrapment Hazard
Do NOT touch any moving or
rotating parts. Guards are provided
to prevent access to these parts, where they
have been removed for maintenance they
MUST be replaced before operating the
equipment.
ATTENTION
ATTENTION