SPP Pumps Auto Prime - High Flow Range XF300 & 400 User Manual
Page 14
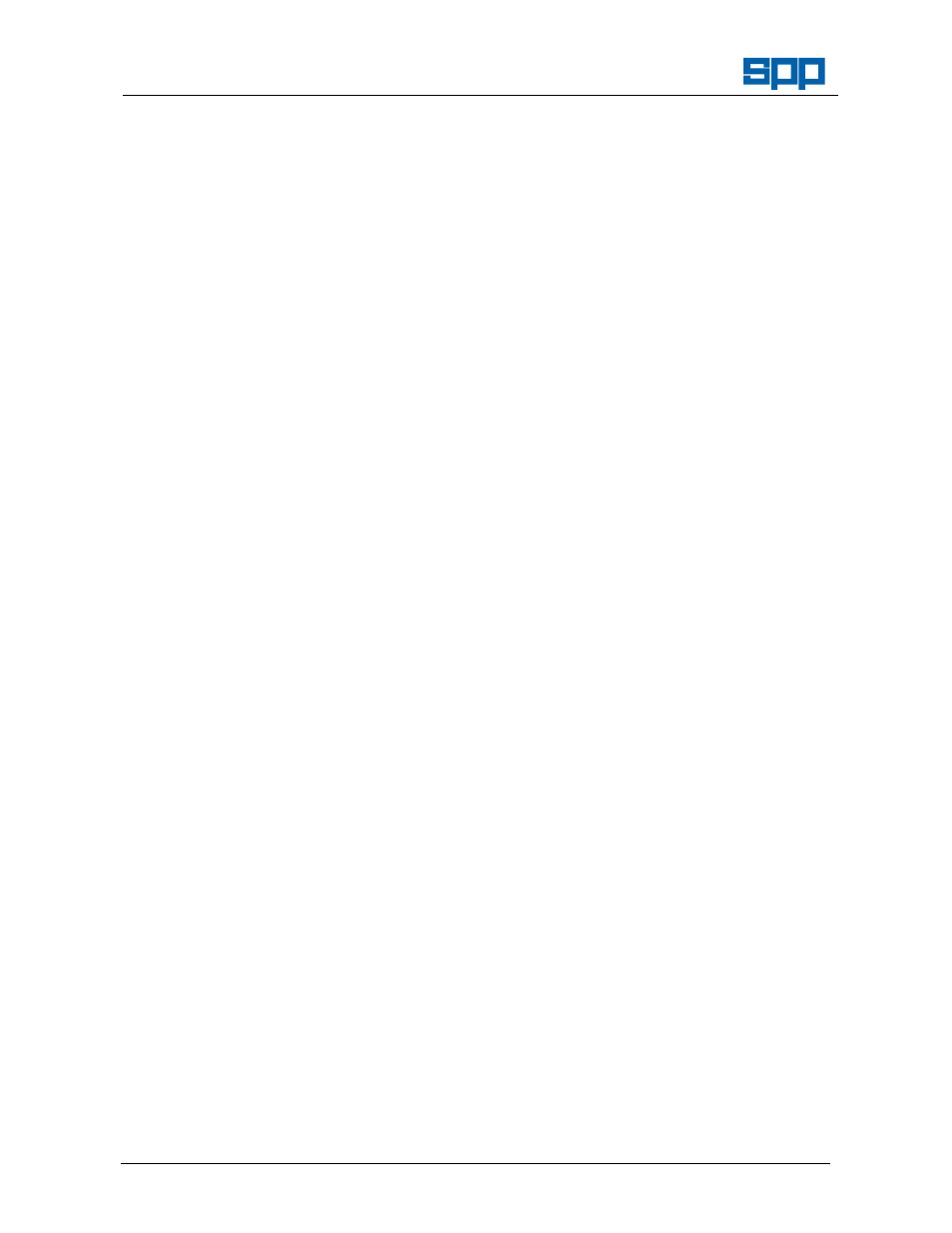
Manual No/Rev
W77-009E / 2
Operators Instructions for
XF300 & XF400 Range Centrifugal Pumps
Our policy is one of continuous improvement and we reserve the right to alter specifications at any time
Page 14 of 23
wrapped for storage.
Check the shaft F10 for straightness by
mounting between centres and measuring
the run-out with a dial gauge at the
coupling, bearings, centre, seal and impeller
positions. The run-out should not exceed
0.05 mm in any of the positions measured.
All parts should be cleaned, inspected for
damage and replaced. If pump efficiency
has reduced, the suction cover B50 wear
plate D10 and impeller C10 may be
replaced, contact the SPP Pumps Ltd.
Spares and Service Departments for supply
of new parts.
6.8 Re-assembly of the Pump
The pump unit may be re-assembled in the
reverse manner to disassembling. To
ensure correct and trouble free operation,
care should be taken on re-assembly and
the following precautions taken:
a) Precautions
Cleanliness is important ensure that all
pump components together with the
working areas, are completely free of
foreign matter, dirt and dust.
All ‘O’ ring grooves and mating surfaces for
shims are to be properly cleaned and new
‘O’ rings and gaskets or shims fitted. ‘O’
rings should be lubricated lightly to ease
assembly.
Check the locking washer F70 for wear or
damage and replace if necessary.
It is recommended that only spare parts
manufactured by and obtained from SPP
Pumps Ltd., are used during maintenance
re-assembly of any AUTOPRIME XF range
pump. The company cannot be held
responsible for any failure, which may
cause danger to property or health, arising
from the use of spare parts manufactured
and supplied by others, these will also
invalidate the pump warranty.
When ordering spare parts it is essential to
quote the pump serial number from the
identification plate and the required part
number(s) as shown in the parts list in
Section 8.
If new proprietary parts such as bearings
and O’ rings are to be fitted, ensure they are
the correct size, grade and quality.
b) Shaft & Bearing Assembly
Establish the correct direction of rotation of
the oil thrower F20, locate the key in its slot
and slide the thrower on from the drive end
of the shaft; Secure in place using the
130mm lock nut F30.
Heat up the first drive end bearing F40 to
110
o
C and slide into position repeat for the
second bearing. Ensure that they are
assembled back to back as show in the
drawing, in section 8. Fit the lock washer
F70 and secure with the 105mm locknut
F60, tighten to 300 Nm torque. Ensure that
they are tight when the bearings are cool.
Heat up the non drive end roller bearing
F50 to 110
o
C and slide onto the shaft.
Ensure that the bearing is fully seated on
the shoulder of the shaft.
c) Bearing Cover Assembly
Insert the lip seal A30 into the drive end
bearing cover A20. Place the cork gasket
A60 in position on the bearing housing.
Apply a bead of Loctite 641 around the face
of the shoulder on the outside of the shaft
seal A50 between the two O rings and using
a press and suitable plate, push it into place
in the pump end bearing cover A40. Place
the cork gasket A60 into position on the
bearing housing,
d) Bearing Housing assembly
Ensure that the inside of the bearing
housing is clean and free of dirt. Mount in a
vertical position and lower the shaft
assembly into position from the drive end.
Use a press push the shaft until the non-
drive end bearings begin to engage with the
housing.
Through the inspection port, check that the
outer race of this bearing is square before
pressing the shaft home to ensure that the
drive end bearings are fully seated in the
housing.
Fit and secure the drive end bearing cover
assembly.
Rotate the housing to the horizontal position
and fit and secure the pump end bearing
cover ensure it is square and ease the shaft
seal A50 into position, once in position
check the seal.