A series – HOMA A Series User Manual
Page 6
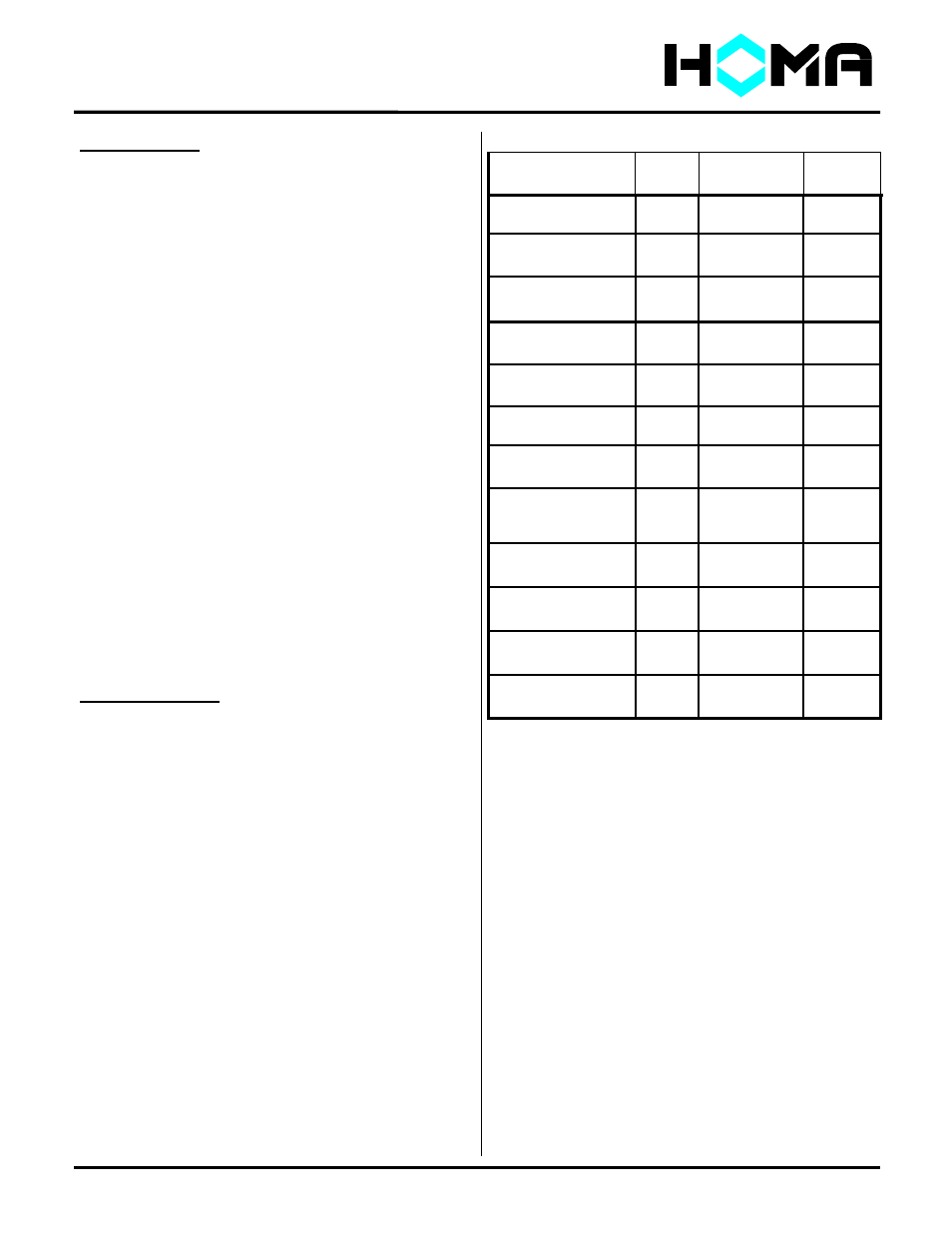
A Series
Installation, Operation & Maintenance Manual
Suction Piping
Suction piping should be at least as large as the
pump inlet elbow suction. If reducers are utilized
they should be of the eccentric, conical type and
must be installed with the level side up. Suction
piping should be run as straight as possible with
a recommended 10 suction diameter distance
before pump inlet. Rough sections in pipe suction
line can cause turbulence and result in severe
vibration of the pump. Pipe reducers should not
be installed adjacent to pump inlet
All pipe flange joints should be gasketed to
prevent air from entering the pipe. High points
that may collect vapor are to be avoided.
Isolation valves such as gate valves can be
installed in order to facilitate the removal of the
pump for maintenance. Any valve installed in the
suction line should be installed with the stems
horizontal.
The location of the suction piping termination
point inside of the wet pit must be installed such
that sufficient submergence is obtained to
prevent vortexing. Invert location and multiple
suction points can cause hydraulic instability to
an operating pump. Avoid high velocity or
turbulence at suction pipe inlet.
Discharge Piping
A check valve and isolation valve shall be
installed in the discharge line. The check valve
should be installed between the pump discharge
flange and the isolation valve. If pipe increasers
are used on the discharge line, they should be
placed between the check valve and the pump.
The inlet elbow stand allows the pump to be
installed in a stationary position in a dry pit. Place
the inlet stand in position and tighten the anchor
nuts.
Lower the pump onto the top flange of the
inlet stand. DO NOT ALLOW SLACK ON THE
LIFTING CABLE UNTIL THE PUMP IS
BOLTED DOWN. Make sure the flange bolt
holes align with the mounting holes on the
underside of the volute. Secure the pump to the
mounting flange with the fasteners that are
specified in the accessory fastener selection
table below.
Bolts
PUMP MODEL
Anchors
SIZE
TORQUE
3” A SERIES
8
M16X60mm
108 ft/ #
AUTOCOUPLING
4
M16
74 ft/ #
4” A-SERIES
8
M16X60mm
108 ft/ #
AUTOCOUPLING
4
M16
74 ft/ #
3” & 4” A-SERIES
4
M16x25mm
108 ft/#
RING STAND
3” & 4” A- SERIES
8
M16x40mm
108 ft/#
DRY SUMP
4
M16
74 ft/#
6” A-SERIES
8
M20x70mm
150 ft/#
AUTOCOUPLING
4
M16
74 ft/#
6" A-SERIES
4
M20x40mm
150 ft/#
RING STAND
6" A-SERIES
8
M20x45mm
150 ft/#
DRY SUMP (1 Piece)
4
M16
74 ft/#
6" A-SERIES
8
M20x65mm
150 ft/#
DRY SUMP
(N/PMotor)
4
M16
74 ft/#
6" A-SERIES
8
M20x70mm
150 ft/#
DRY SUMP (F Motor)
4
M16
74 ft/#
8” A-SERIES
8
M20x70mm
150 ft/#
AUTOCOUPLING
4
M20
150 ft/#
8" A-SERIES
4
M20x30mm
150 ft/#
RING STAND
8" A-SERIES
8
M20x75mm
150 ft/#
DRY SUMP (2 Piece)
4
M20
150 ft/#
Notes:
1. For pumps larger than 8” please consult
factory.
2. Flange bolts must be tightened in cross
pattern to avoid damage to the raise face
flanges.
3. Standard Flange Bolts are 316SS
4. Standard Anchors are Plated Steel
5. Autocoupling systems include qty 4 M12
anchors for the upper bracket. Torque to 38
ft#.
6. Anchor bolt holes should be drilled to the
actual diameter of the anchor (M12 anchor
requires 12mm diameter hole).
Pg. 6