Burkert Type 0404 User Manual
Operating instructions type 0404
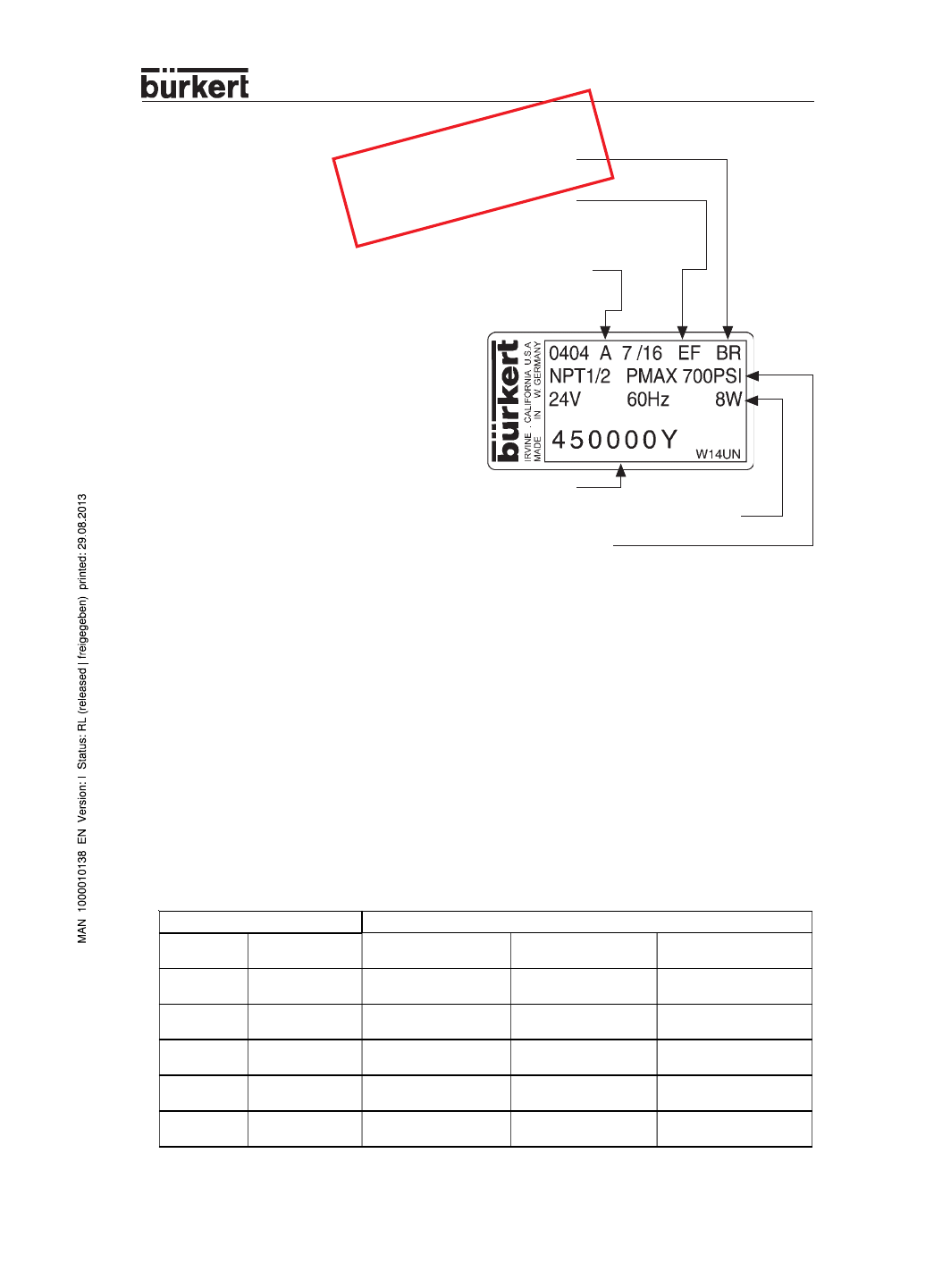
Operating Instructions
Type 0404
Marking (example):
Body Material
BR
=
Brass
Seal Material
NBR
=
NBR
EB
=
PTFE seat and NBR =-ring
EF
=
PTFE seat and FKM O-ring
Circuit Function
A =
Normally Closed
B =
Normally Open
Recorder No.
Voltage / Frequency / Power Consumption
Maximum Pressure
Approvals
The valve is either approved as
General Purpose valve for Hazardous Locations
Class I, Division 1, Group A, B, C, D
Class II, Division 1, Group E, F, G
Class III, Division 1 and 2
Operating Temperature T 4
or
General Purpose valve for Hazardous Locations
Class I, Division 1, Group A, B, C, D
Class II, Division 1, Group E, F, G
Class III, Division 1 and 2
Operating Temperature T 6
or
FM approved as
Nonincendive for Hazardous Locations
Class I, Division 2, Group A, B, C, D
Class II, Division 2, Group F, G
Class III, Division 1 and 2
Operating Temperature T 4A
UL listed for Ordinary locations
CSA approved for Ordinary locations
See label on the valve.
Operating Instructions 0605/08_EU-EN_00893136
Design:
2-way solenoid valve, internally piloted, normally closed
(Circuit function A) or normally open (Circuit function B).
Seal Materials and Fluids handled:
See Table1.
Fluid and Ambient Temperature:
For Hazardous Locations Div. 1 (T4 rated)
Max. Ambient Temperature
104 °F (40 °C)
Max. Fluid Temperature
194 °F (90 °C)
For Hazardous Locations Div. 1 (T6 rated)
Max. Ambient Temperature
104 °F (40 °C)
Max. Fluid Temperature
140 °F (60 °C)
For Hazardous Locations Div. 2 and Ordinary Locations:
See Table1.
Pressure Range:
Minimum pressure differential between inlet and outlet port is
15 PSI.
Maximum inlet pressure see label on valve.
Installation:
Before installing valve ensure that piping etc. is free of foreign
matter (metal fillings, seal material, welding scale etc.). PTFE
tape is recommended for sealing ports. Arrow on valve body
gives flow direction. Installation as required but preferable
with coil uppermost. Installation in this position tends to
prevent foreign matter remaining in pilot valve (increased
life). A strainer upstream of valve, protects against effects of
foreign matter. Do not put any loads on coil unit. Pipework
should be supported such that valve body is not under strain.
Do not allow a pipe-end or sealing material to block the pilot
bore within the valve outlet. Inlet and outlet of valve must be
fullbore and pipework unrestricted.
Table 1
Seal materials
Fluid
Temperatures [°F]
Buna "N" (B)
PTFE/ (K)
Buna "N"
PTFE/ (F)
FKM
Air
Fluid T.
Ambient
+ 14 to + 194
+ 14 to + 130
+ 32 to + 212
+ 32 to + 130
+ 32 to + 212
+ 32 to + 130
Water
Fluid T.
Ambient
+ 32 to + 194
+ 32 to + 130
+ 32 to + 212
+ 32 to + 130
+ 32 to + 212
+ 32 to + 130
Neutral gas
Fluid T.
Ambient
+ 14 to + 194
+ 14 to + 130
+ 32 to + 212
+ 32 to + 130
+ 32 to + 212
+ 32 to + 130
Light oil
Fluid T.
Ambient
+ 14 to + 194
+ 14 to + 130
+ 32 to + 212
+ 32 to + 130
LP-gas
Fluid T.
Ambient
+ 14 to + 140
+ 14 to + 130
+ 32 to + 140
+ 32 to + 130
+ 32 to + 140
+ 32 to + 130
Voltage 12V or 24V
UL / UR valid with
class 2 power supply only