Fill-Rite TM Series Precision Meter User Manual
Page 7
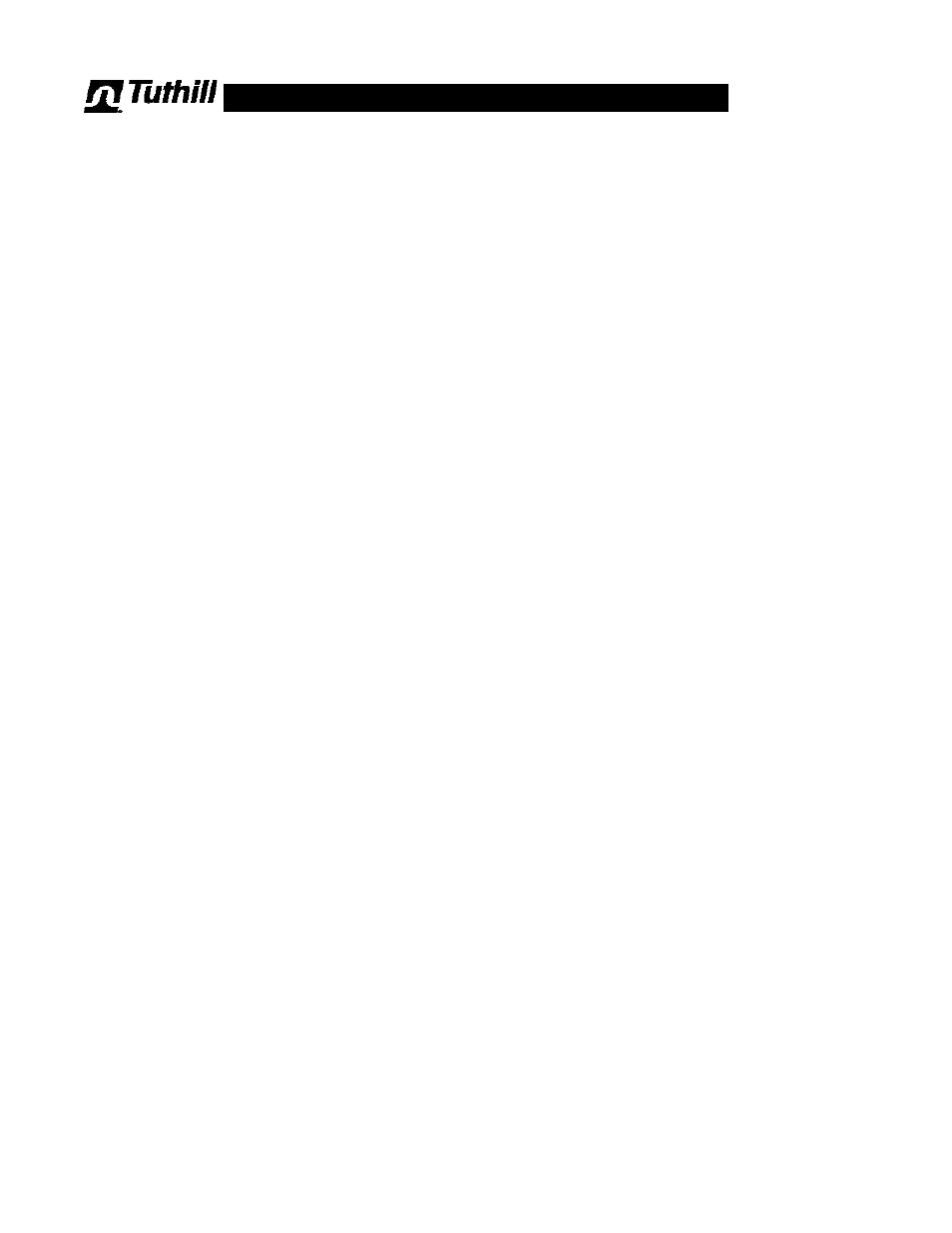
Breaking Teeth on Rotors (Oval Gears)
This is a sign of hydraulic shock conditions in the system.
Common sources:
Starting or stopping flow too rapidly. Replace dam-
aged components and correct operational practices.
Pump by-pass not adjusted properly. Re-adjust as
necessary.
Leakage from Cover
The seals (and possibly end covers) have been damaged
due to excessive pressure. There are two possible sources:
Starting or stopping flow too rapidly. Replace dam-
aged components and correct operational practices.
The flow meter is in a system, where it can be isolated
between two valves. Add a Thermal Relief Valve to
bleed off excess pressure when the temperature rises.
Installation, Maintenance & Service must be performed
by personnel:
A. Qualified to work on this type of equipment.
B. Familiar with all applicable local codes and ordi-
nances covering the type of service, where the flow
meter is used (gasoline, LPG, etc.).
Avoid pipe strain and stress when making flow meter re-
pairs. The weight of the pipe and the flow meter must be
supported independently. This allows the flow meter to be
serviced without affecting the alignment of piping.
Avoid prying or exerting heavy pressure on precision parts,
as this can affect the performance of the flow meter. Assure
that all machined parts are free of burrs and nicks. Stone all
machined surfaces if necessary to remove burrs.
Always coat bolt threads with an anti-seize or an appropriate
lubricant. This prevents thread damage, and assures that
proper torque values are applied during re-assembly. If
threads are damaged, repair using inserts.
Relieve All Internal Pressure Prior to Opening
Drain Liquid prior to Working on Flow Meter
Rinse with Neutral Liquid
prior to Seasonal Storage
Triple Rinse with Neutral Liquid
prior to Shipment for any reason.
1 . 7
No Flow
Blocked strainer basket. Clean the basket.
Faulty or non-functioning pump. Repair pump.
Valve stuck in closed position. Check and repair valves.
Flow meter ‘frozen’ due to build-up of chemical salts (or
frozen water) inside the measuring chamber. Clean the
flow meter (see page 1.8), and inspect for damage.
Meter jammed on a particle that has passed through a
damaged strainer basket. Remove particle and replace
rotors if necessary, replace strainer basket.
Reduced Flow Rate
Strainer basket partially blocked. Clean the basket.
Pump not functioning correctly. Repair pump.
Valve stuck in partially closed position. Check valves and
repair.
Meter rotors (oval gears) partially ‘salted’ with chemical
deposits, slowing the movement. Clean the meter (see
page).
Product Flows, but the register does not record
Check power supply to the register.
Check the connection between the pulser and the elec-
tronic register.
Check pulser output (see page 1.8). Replace if needed.
If product is flowing, and the flow meter is generating a
pulse signal, the problem is in the electronic register.
Please refer to the manual for the electronic register.
Product Flows, register does not record correctly
If error factor is constant, the flow meter is fine. The likely
cause is either:
Incorrect K Factor in the electronic register. Re-
calibrate the meter and correct the K Factor.
A constant problem with air getting into the system.
Review system design and control valves.
If the error is random, the likely cause is either:
Poor cable connections (insulation not trimmed, or
stray strands getting close to incorrect contacts). This
can be signal conditioner (if included) or where pulse
signal is connected to the register. Inspect and correct
connections as necessary.
Valve leaking, allowing a portion of the system to drain.
Check & repair valves.
An intermittent problem with air in the system, com-
bined with inadequate air elimination. Review system
design and control valves.
Interference from other electrical equipment nearby.,
possibly combined with sub-standard cables.
Prior to opening or disassembly of any flow meter, all internal pressure must be relieved and all liquid must be
drained. This must be done in accordance with applicable company and local codes & ordinances.
Make sure that all necessary safety precautions have been taken, including proper clothing, personal safety equip-
ment and fire safety equipment if required.
Trouble Shooting & Service