Balancing accuracy of rigid rotors – CEMB USA N300 User Manual
Page 79
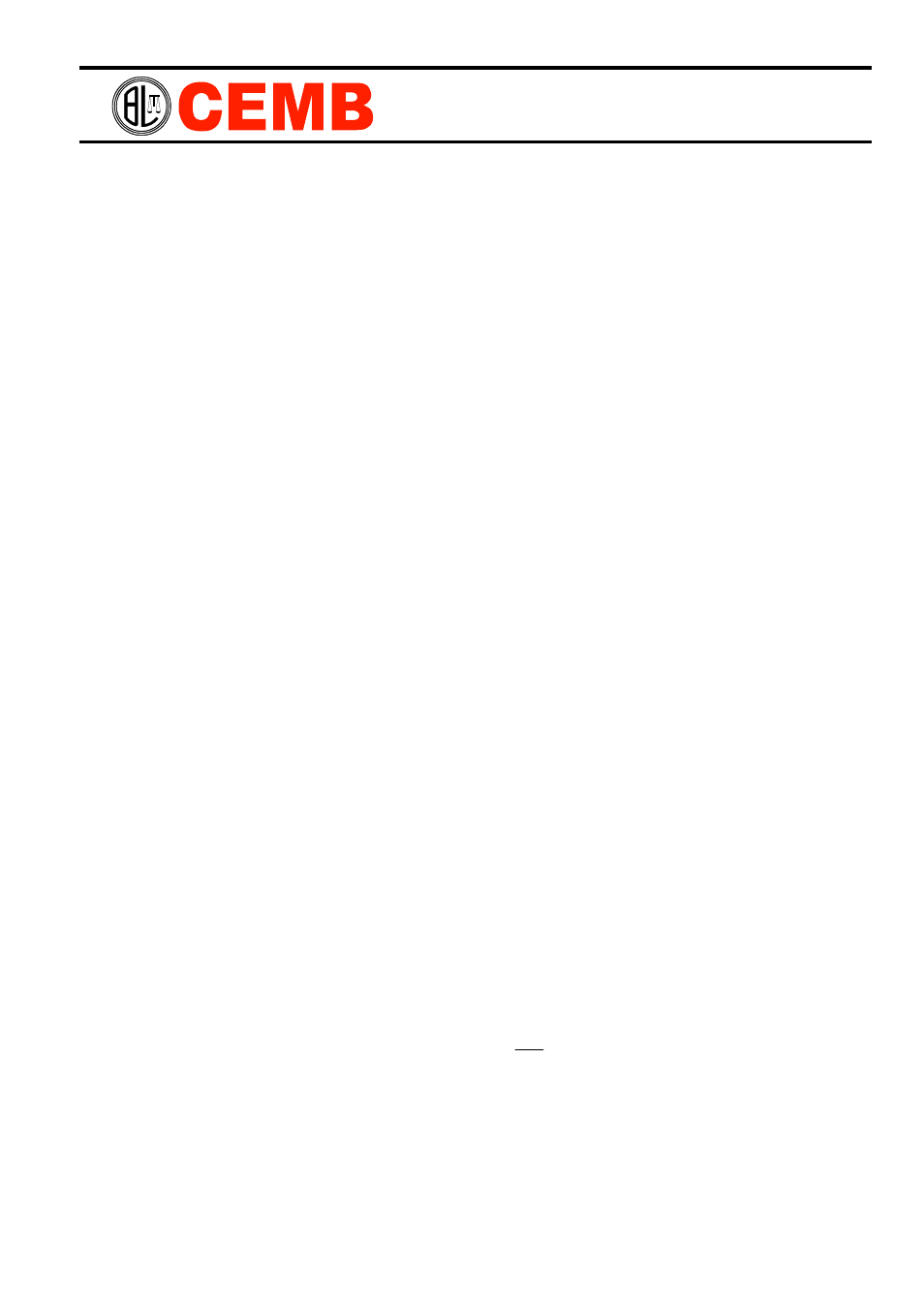
BALANCING ACCURACY OF RIGID ROTORS
are different according to whether the rotor may be considered
rigid or flexible, similarly, the balancing accuracy or tolerance
is different in the two cases. Suffice to say that in a flexible
rotor, the effect of unbalance is amplified by the elasticity in
such a way as to generate in the pedestals different forces than
those created by a rigid rotor with the same unbalance. We can
deduce, all other conditions being equal, that the balancing
tolerances of the two cases will be different in the presence of
equal forces or vibrations on the pedestals.
The contents of this pamphlet may be considered to be valid
only for rigid rotors, unless otherwise specified.
UNIT OF MEASUREMENT OF BALANCING
TOLERANCE
Balancing tolerance is given by the product of the maximum
permissible unbalance by its distance from the rotational axis.
If the balancing tolerance is divided by the weight of the rotor,
we obtain the “specific unbalance”. This is also called the
“residual permissible eccentricity” as, in the case of static
unbalance, it expresses the eccentricity of the rotor’s barycentre
from the rotational axis caused by the permissible unbalance.
The purpose of balancing is to improve the distribution of
the mass of a rotor so that it may rotate on its bearings
without creating unbalance centrifugal forces higher than
a predetermined permissible value.
This aim can and must be attained only to a certain degree as,
even after balancing, residual unbalance will inevitably persist.
Just as when machining a piece in a workshop it is never possible
to mach drawing sizes with perfect exactness and it is necessary
to predetermine a “machining tolerance”, which varies in
accordance to the requirements of each single piece, also when
balancing, the precision obtained has to suit the needs of each
single piece, which is achieved by fixing a “maximum
permissible residual unbalance” or “balancing tolerance”.
It is obvious that an insufficiently balanced piece will cause
intolerable vibrations with all consequent malfunctions or
damage. However, it would be clearly useless to balance a rotor
to a degree of quality greater than required for a regular and
normal operation of the machine incorporating that part, by using
a balancing machine to its peak precision. In fact, exaggerating
the quality requirements would only result in a waste of time
and a higher balancing cost, without improving the quality of
the rotor.
When fixing the balancing tolerance, the concept of
“reproducibility” should also be borne in mind, i.e. the minimum
value that can be certainly reproduced on repeated testing. For
example: if with the simple operation of disassembling and
reassembling a piece on the balancing machine or of balancing
it at different times on the machine itself there is a variation in
eccentricity of 5 microns, it is quite useless to balance that piece
with a much greater precision than 5 microns.
It is therefore necessary to calculate and prescribe the
technical and economically most effective levels of balancing
tolerance for each type of rotor.
The drawing should, therefore, always show:
- the value of the maximum permissible residual unbalance
for each of the correction planes, with precision;
- where and how compensating weights should be added; or
where material may be removed without damaging the piece;
- the journals that should support the rotor on the balancing
machine;
- the recommended speed range for balancing;
- all other useful data from case to case, that may help to
enable the user to carry out balancing operations quickly
and safely.
This applies to rigid rotors; for flexible rotors, other
specifications should be applied. Just as balancing operations
23826 MANDELLO DEL LARIO (LC) ITALY
SYMBOLS
p
(grams)
= maximum permissible unbalance
r
(mm)
= p ’s distance from the rotational axis
P
(kg)
= rotor weight
n
(rpm)= normal service rotational speed
p·r
(gr·mm)
= maximum permissible residual unbalance
e
=
P
r
p
⋅
= residual permissible eccentricity (micrometer)
G
(mm/s)
= balancing grade (see table)