Cla-Val 100-43 User Manual
Page 2
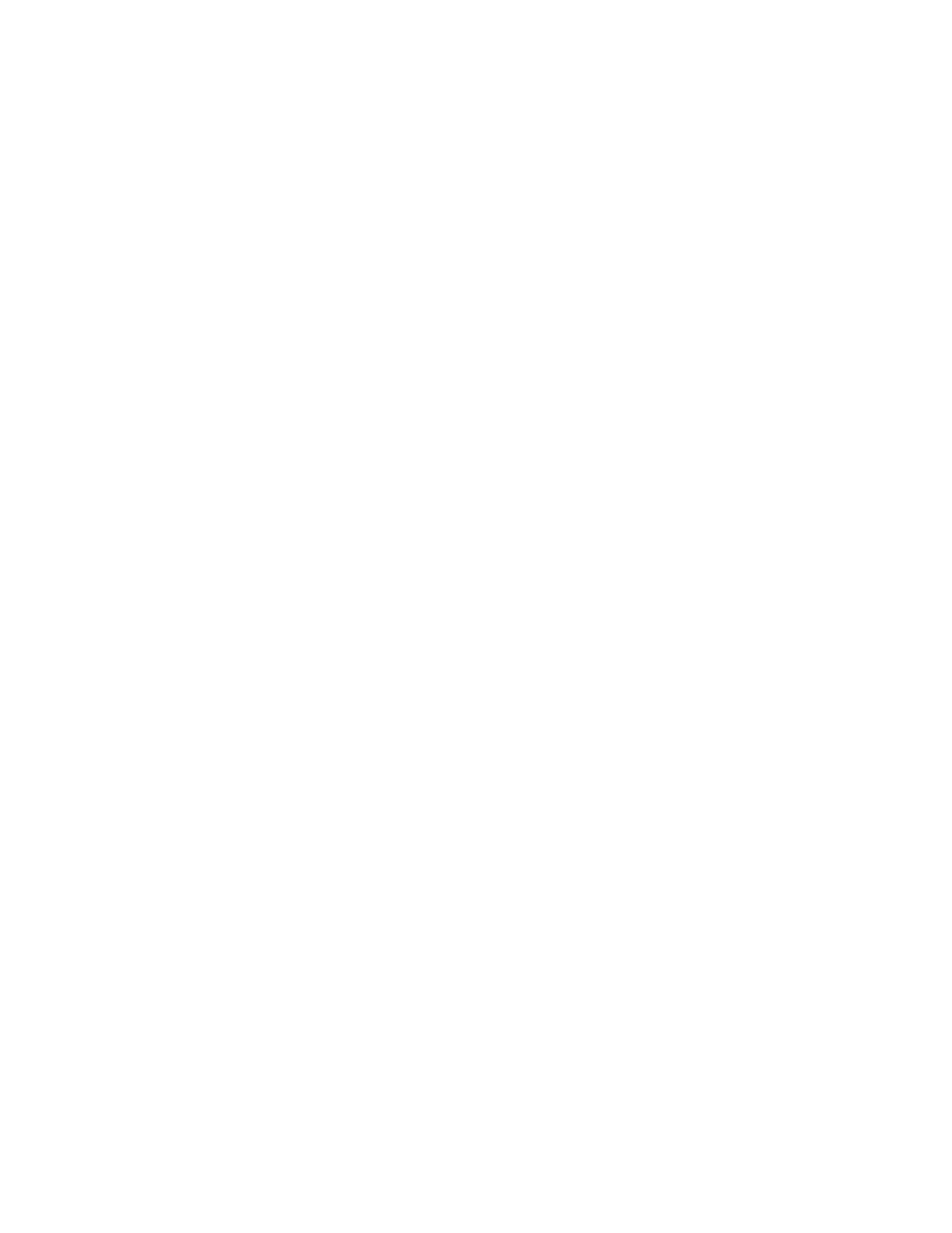
MAINTENANCE
The only maintenance normally required is periodic inspection of
the control system to insure there is no buildup of solids that might
cause poor performance. This is usually accomplished by cleaning
the strainer screen. Also, see pilot valve maintenance bulletin.
Established client fire and safety systems test guidelines must be
followed. NFPA 25 Standard for the Inspection, Testing and
Maintenance of Water-Based Fire Protection Systems must also
be followed.
CAUTION: BEFORE PROCEEDING WITH THE DISASSEMBLY
OF ANY CLA-VAL PRODUCT, STRICT COMPLIANCE WITH
YOUR FACILITIES ESTABLISHED SAFETY PROCEDURE FOR
ISOLATING, TESTING OR EXHAUSTING PRESSURE FROM A
CONTROL SYSTEM OR DEVICE IS REQUIRED.
MEDIA CONTROL SYSTEMS CONTAIN HIGH LEVELS OF
STORED ENERGY. DO NOT ATTEMPT TO CONNECT, DISCON-
NECT OR REPAIR THESE PRODUCTS WHENEVER A SYSTEM
IS PRESSURIZED.
NOTE: ALWAYS EXHAUST THE PRESSURE FROM THE SYS-
TEM BEFORE PERFORMING ANY SERVICE WORK. FAILURE
TO DO SO CAN RESULT IN SERIOUS PERSONAL INJURY.
TUBE DIAPHRAGM REPLACEMENT
If it becomes necessary to replace the tube diaphragm, use the fol-
lowing procedure:
A. TOOLS REQUIRED
1 - Nylon or rubber hammer
2 - 1" dia. x 3’ long wooden dowels
1 - 5/8" dia. x 3’ long wooden dowel (Used to get 1" dowel into position)
1 - Replacement tube diaphragm
2 - Replacement o-rings
B. REMOVAL (IMPORTANT: Protect all coated surfaces during this
operation.) (Note: The outlet end of the tube diaphragm is 1/8"
thicker than the inlet end.)
1. Follow depressurization and removal permit procedures in effect
at the site.
2. Remove valve from line.
3. Remove control tubing connecting end pieces and control
chamber. Mark inlet and center for reassembly, i.e. "line-up marks"
4. Remove control chamber assembly bolts.
5. Remove barrier by hitting on inlet end of barrier rod with rubber
hammer. Remove barrier, nuts and rod.
Install new O-rings.
6. Remove tube diaphragm from control chamber by forcing inlet
end of tube to center of control chamber using 1" dowel.
7. Once inlet end of tube is inside the control chamber, place 1"
wooden dowel between tube and control chamber on the inlet end
and push it all the way through. After the dowel is protruding from
both ends of the control chamber, push down on the tube
diaphragm and force it out of the control chamber.
This is best done with the control chamber in a vise.
Remember to protect the coated surfaces.
C. ASSEMBLY (IMPORTANT: Protect all coated surfaces during
this operation.)
1. Place tube diaphragm into control chamber as follows:
(Note: The outlet end of the tube diaphragm is 1/8" thicker than the
inlet end.)
a) Grease end of tube and the inside of control chamber.
(WD-40 is a satisfactory lubricant).
b) Fold inlet end of tube and push into control chamber to within 1"
of the opposite end.
This operation best done on the floor on top of a corrugated box or
piece of plywood.
c) Place the inlet end up on the floor.
(Be sure to protect all coated surfaces.)
d) Depress tube to center using large or small wooden dowel.
Small dowel is used on 3" & 4" tube diaphragms to make space for
the large dowel.
e) Insert wooden dowel between tube diaphragm and control
chamber and leave in place.
f) Force rubber open in another spot and insert another wooden
dowel.
g) Force solid rubber ends over lip of control chamber with wooden
dowels. (Similar to removing a tire from a rim).
h) Place the outlet end up on the floor.
2. Install new O-rings and barrier assembly rod, washers and nuts.
Make sure that the barrier is centered over the unthreaded portion
of the shaft. (Note: The end of the shaft with the threaded portion
is installed on the inlet side of the barrier.)
3. Install barrier into tube diaphragm. (Use grease, WD-40 or
soapy water for lubrication). (Note: The thicker end of the tube
diaphragm must be on the outlet end (white stripe). The barrier fins
must also be on the outlet end).
4. Center the barrier assembly inside of the tube diaphragm.
5. Assemble the end pieces to the control chamber.
6. The control chamber body assembly flange bolts only require 45
foot pounds of torque to seal the tube diaphragm. The flanges are
metal to metal externally.
The tube diaphragm is suspended from these flanges internally,
providing a seal. The sealing capability of this assembly is very
good due to the compression of the thick solid rubber ends of the
tube diaphragm.
7. Inlet End - Torque the bolts to maximum 45 foot pounds
maintaining an even space all the way around until flanges touch.
8. Outlet End "White Stripe" - Torque the bolts to maximum 45 foot
pounds maintaining an even space all the way around until flanges
touch.
(Note: The outlet end of the tube diaphragm is 1/8" thicker than the
inlet end.)
9. Reassemble control tubing.
10. Assembly is complete. Return valve to service.