Cla-val – Cla-Val X133 User Manual
Page 2
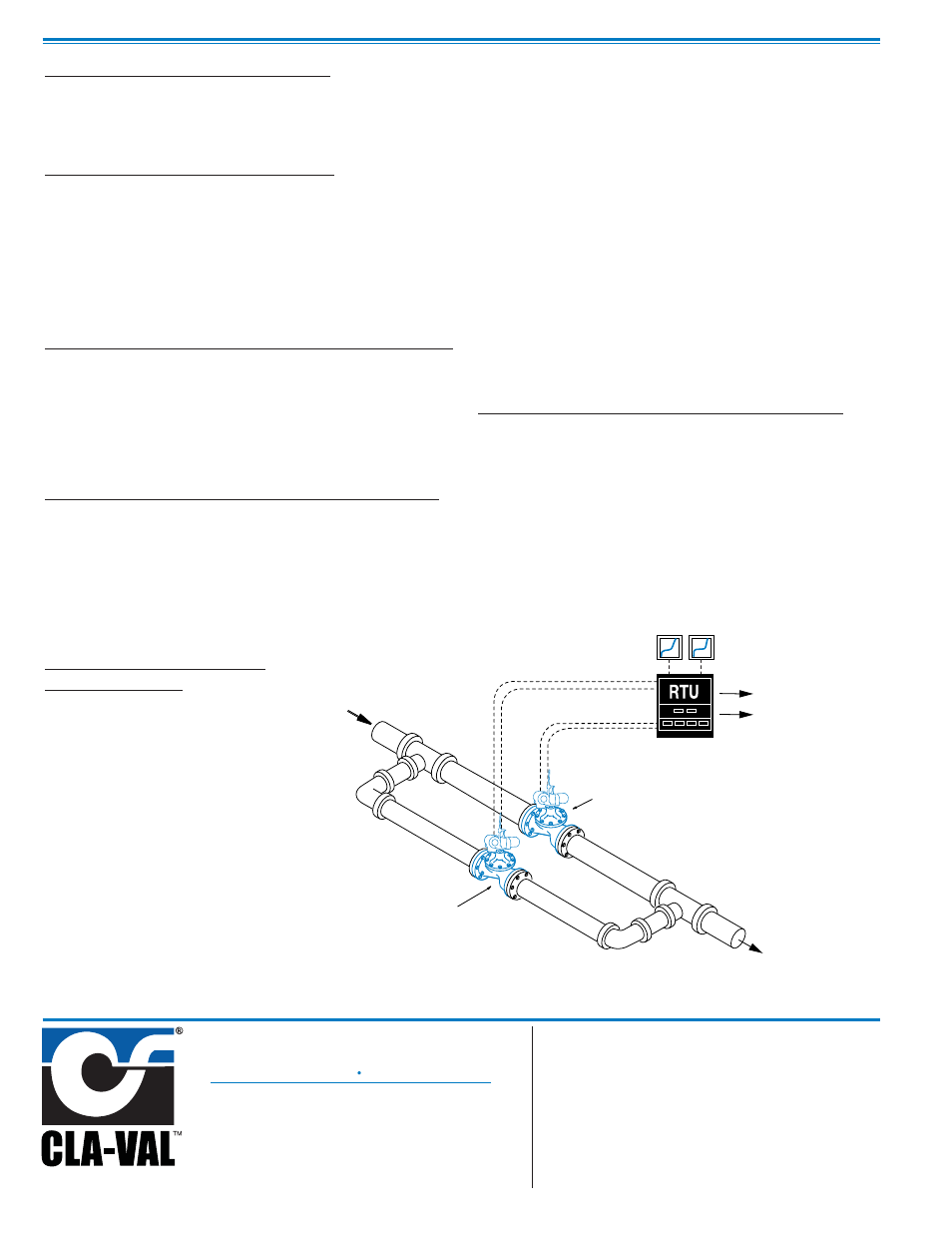
PO Box 1325 Newport Beach CA 92659-0325
Phone: 949-722-4800
Fax: 949-548-5441
CLA-VAL
CLA-VAL CANADA
CLA-VAL EUROPE
4687 Christie Drive
Beamsville, Ontario
Canada L0R 1B4
Phone: 905-563-4963
Fax: 905-563-4040
Chemin dés Mesanges 1
CH-1032 Romanel/
Lausanne, Switzerland
Phone: 41-21-643-15-55
Fax: 41-21-643-15-50
©
COPYRIGHT CLA-VAL 2011 Printed in USA
Specifications subject to change without notice.
www.cla-val.com
E-X133 (R-3/2011)
Represented By:
Using Cla-Val Valve Meter software
There are 4 ways to calculate flow from the software provid-
ed. These methods provide a wide variety of choices for
integration into your system.
Custom Curve Linearization in RTU
Many RTUs and PLCs have built-in custom curve capabili-
ty. The Cv values at each valve position can be entered
into the field equipment for direct flow calculation at the
valve site for monitoring and/or control purposes. Best accu-
racy is attained using values at each 1 or 2 % valve open-
ing. A lower number of values may be used with variable
spacing of data points.
Manual Calculations in Microsoft Excel (v. 97 or later)
This method is for applications where valve position and
differential pressure or upstream and downstream pressure
is monitored by the SCADA system. The current values are
manually entered in Excel and the flow is calculated and
displayed. The calculated flow can be copied into other
programs for monitoring purposes.
Remote Excel calculations from SCADA software
Some SCADA software programs include Visual Basic pro-
gramming capability for sending and receiving values to and
from Excel. The calculations in the above example are then
automated using this "remote automation" process.
Programming of the SCADA software is necessary to
accomplish this. Contact Cla-Val
for details.
Direct Flow Calculations in
SCADA Software
This method does not require
Excel if the SCADA software
includes Visual Basic program-
ming capability to call dll functions.
In this case the SCADA software
calls the function for any valve
position. The returned Cv value is
then used in the flow calculation
formula.
Q = Cv * sqrt(DP)
Where
Q = flow (gpm)
Cv = returned Cv at the current valve position
DP = difference between upstream and downstream
pressure (psi)
An example of using the function for a 6 inch 100-01
valve with
Upstream pressure = 100 psi
Downstream pressure = 50 psi
Valve position = 30 %
Q = cv_6(30) * sqrt(100-50) = 82.6 * sqrt (50) = 584 gpm
cv_6() is the function name used in Visual Basic
Accuracy and Calibration Recommendations
All sensors must be calibrated for best accuracy. In addi-
tion the differential pressure transmitter must be set to
the correct range. Typical accuracy is within 2 to 3% actu-
al flow. Accuracy may be less than this if:
• Valve position is less than 5%
• Sensors are not calibrated or zeroed
• Incorrect range of differential pressure transmitter
• Valve is corroded
• Inlet conditions are not full pipe flow
• Valve pressure differential less than one-half psid
High Pressure
Constant
Downstream
Pressure
3" 90-01
8" 90-01
To SCADA
3" Flow Rate
8" Flow Rate
3"
8"