Vii. lubrication, Blower startup, Motor bearings – Spencer Power Mizer Multistage Centrifugal Cast Blowers User Manual
Page 8: Blower bearings–grease lubricated
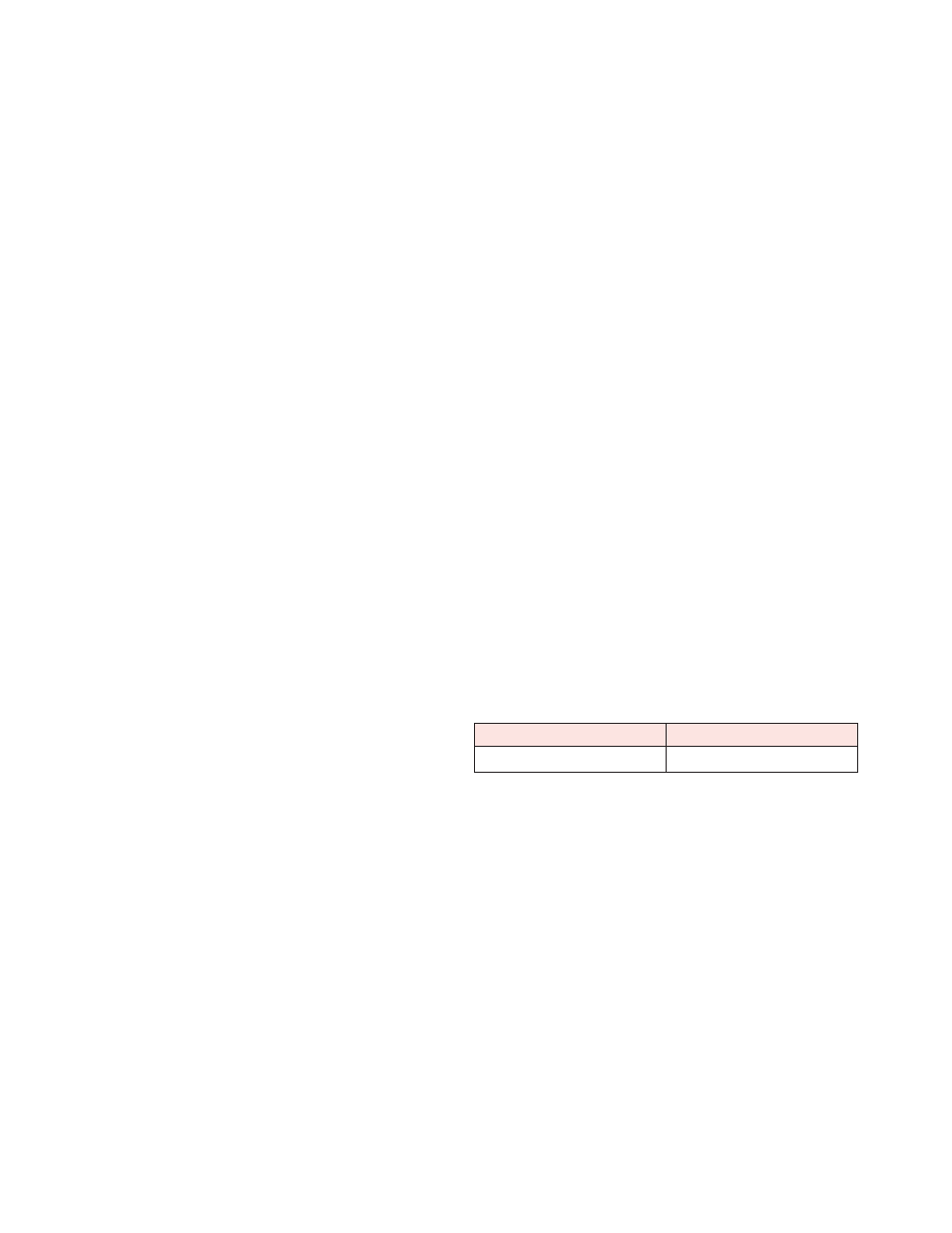
8
Blower Startup
With the system connected and the throttling valve closed, turn
the blower on. Quickly assess the current draw of the motor.
Adjust the system load or throttling valve until the desired
flow is reached, being careful not to exceed the full-rated
motor capacity. Initially, blowers will temporarily develop more
differential pressure and take more power. Check final settings
after operating temperature is achieved, typically after one-half
hour. If the throttling valve is not fully open when the motor
capacity has been reached, it should be fixed at this point to
prevent further opening and possible overloading of the motor.
1. Surge
CAuTIOn: Do not operate blower in surge (unstable low
flow range). Damage to blower caused by operating in
surge is not covered by Spencer warranty.
A blower in surge produces a rush or pulsating rhythmic air
sound caused when airflow into or out of the blower is restricted.
In addition to its characteristic noise, surge may be detected
by power or pressure fluctuations. Surge is potentially destruc-
tive because it is accompanied by excessive temperatures and
aerodynamic forces that will ultimately cause mechanical failure.
A surge condition is simply eliminated by increasing the airflow
either into the system or to a bypass or vent. Various surge con-
trol devices are also available from Spencer–see page 6.
NOTE: If a blower surges violently at startup, avoid recurrences
by leaving the throttling valve open at or near its normal oper-
ating position.
2. normal Operating Limits
NOTE: Use of a Spencer bearing temperature monitor and
vibration monitor is recommended to alert personnel to blower
operation outside the following limits.
• Vibration should not exceed 0.23 in/sec (5.8 mm/sec) at the
bearing housing.
• Bearing temperatures should not exceed 220 °F (104 °C) at
the bearing housing surface.
If abnormal operation is detected, shut the blower down and
refer to the Troubleshooting Guide on page 14 or contact
Spencer.
3. Periodic Operation
CAuTIOn: All blowers should be operated periodically.
In multiple blower installations, periodically rotate each blower
from standby to operating status.
4. Parallel Installation
CAuTIOn: A check valve must be installed in the discharge
line of each blower or inlet of each vacuum producer
operating in parallel to prevent reverse flow through idle
units.
CAuTIOn: Do not operate centrifugal blowers in parallel
with positive displacement blowers. Such operation may
damage the centrifugal blowers and will void the warranty.
When operating two or more blowers in parallel (typically iden-
tical blowers), each must carry its share of the load. The
current readings of all motors should be approximately the
same. It may be necessary to readjust the individual throttling
valve stops to attain similar readings.
VII. Lubrication
WARnInG: DISCOnnECT AnD LOCk OuT ELECTRICAL
POWER BEFORE PERFORMInG LuBRICATIOn.
CAuTIOn: Maintain extreme cleanliness to avoid bearing
contamination and damage.
Motor Bearings
Follow the motor manufacturer’s recommendations. Some
motors are equipped with sealed bearings not intended for
relubrication; these motors have no grease or drain plugs.
Blower Bearings–Grease Lubricated
Use Chevron SRI #2 grease. Intermixing incompatible greases
or using any other type may result in bearing failure which is
not covered under the Spencer warranty.
Chevron SRI #2 Grease Specifications
Grade or consistency ........................................................... #2
Thickener ................................................................... polyurea
ASTM Dropping Point .................................................... 480 °F
Work Penetration ............................................................... 270
Base Oil Viscosity ...................................... 600 SUS @ 100 °F
Color ......................................................................Blue-Green
Relubricate approximately every six months, according to the
following table.
Recommended Lubrication Intervals
Normal Conditions
Extreme Conditions*
4000–5000 hours
2000–3000 hours
*Excessive heat, moisture, dust or corrosive conditions.
NOTE: More bearing failures are caused by overgreasing than
lack of lubricant. Add grease sparingly and only when the bot-
tom drain plug is open.
CAuTIOn: keep the grease clean; any dirt or contami-
nants will damage the bearings.
1. Remove the bottom drain plug.
2. Probe the drain with a clean rod to free hardened grease.
3. Inject new grease only until old grease appears at the
drain. NOTE: Some housings have two grease fittings.
4. Restart the blower with the drain plug still removed to allow
excess grease to escape.
5. After normal operating temperature is reached, replace the
drain plug.
Lubrication of replacement bearings. Before installing, “but-
ter” both sides of replacement bearings by forcing grease into
each side until the grease is flush with the race.