Labyrinth seal removal and replacement – Spencer Power Mizer Multistage Centrifugal Cast Blowers User Manual
Page 12
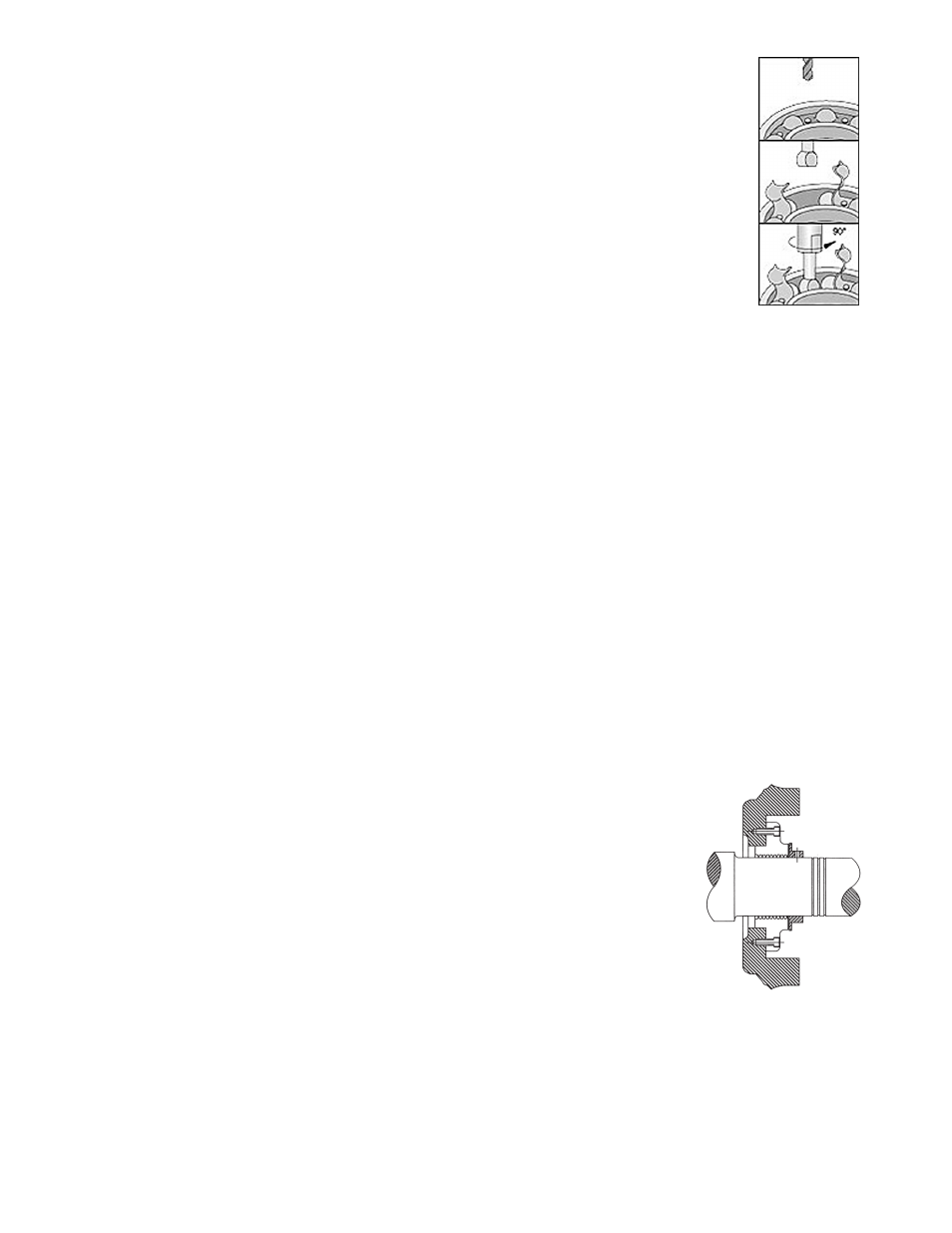
12
NOTE: No shaft support is needed; the shaft will be supported
by the labyrinth seals.
Bearing Replacement Procedure
CAuTIOn: Maintain extreme cleanliness to avoid bearing
contamination and damage. use new gaskets.
1. Install components in the reverse order of disassembly.
2. Press the bearing onto the shaft until seated against the
shoulder. Pusher kits are available from Spencer.
NOTE: If present, oil slinger ‘dimples’ should face the
bearing.
3. Lubricate according to instructions on pages 8 and 9.
Series 3000, 4000, 5000, 6000
Bearing Removal Procedure
1. Remove coupling guard.
2. Split the coupling halves, recording the relative position of
the motor and blower shafts (not the coupling shells).
3. Unbolt and move motor.
4. Use puller to remove blower coupling half. Apply heat if
necessary.
5. For oil-lubricated bearing, drain all oil by removing drain
plug from the bottom of the bearing sump.
6. For oil-lubricated bearing, disconnect oiler tubing and oiler
if necessary.
7. Remove bearing cap.
8. Remove shaft locknut and lockwasher.
9. Remove bearing housing bolts.
10. Using a two-arm puller and the two tapped puller holes
(5/8") in the bearing housing, remove housing, bearing(s)
and bronze seal, if present, as a unit.
11. ‘Drift’ the bearing(s) out of the housing.
NOTE: No shaft support is needed; the shaft will be sup-
ported by the labyrinth seals.
Bearing Replacement Procedure
CAuTIOn: Maintain extreme cleanliness to avoid bearing
contamination and damage. use new gaskets.
1. Install components in the reverse order of disassembly.
NOTE: If the assembly is equipped with a bronze rotation
shaft seal, start the seal on the shaft, but do not seat.
2. Press the bearing(s) onto the shaft until seated against
the shoulder. Pusher kits are available from Spencer.
NOTE: Double bearings must be installed back-to-back.
3. Lubricate according to instructions on page 9.
Series 7000, 8000
Bearing Removal Procedure
1. Remove coupling guard.
2. Split the coupling halves, recording the relative position of
the motor and blower shafts (not the coupling shells).
3. Unbolt and move motor.
4. Use puller to remove blower coupling half. Apply heat if
necessary.
5. Drain all oil by removing drain plug from the bottom of the
bearing sump.
6. Remove bearing cap.
7. Remove slinger cover, shaft locknut,
lockwasher, spacer, oil slinger, and
bearing retainer.
8. Open a section of the ball cage on the
bearing and cut the swarf out.
9. Using a blind housing puller kit (avail-
able from Spencer), insert the appro-
priate bearing adapter and rotate it
90 degrees to achieve a positive grip
within the bearing race.
10. Prepare the opposite cage area in the
same manner and insert the second
adapter.
11. Connect both adapters to the main rod.
Assemble beam and spindle.
12. Pull out bearing.
NOTE: No shaft support is needed; the shaft will be supported
by the labyrinth seals.
Bearing Replacement Procedure
CAuTIOn: Maintain extreme cleanliness to avoid bearing
contamination and damage. use new gaskets.
1. Install components in the reverse order of disassembly.
2. Heat the bearing. Normally a bearing temperature of 80 to
90 °C (144 to 162 °F) above that of the shaft is sufficient for
mounting.
CAuTIOn: never heat a bearing to a temperature
greater than 125 °C (257 °F), never heat a bearing
using an open flame.
3. Press the bearing onto the shaft until seated against the
shoulder. Pusher kits are available from Spencer.
NOTE: Oil slinger ‘dimples’ should face the bearing.
4. Lubricate according to instructions on page 7.
Labyrinth Seal Removal and
Replacement
NOTE: Labyrinth seals are non-contacting and do not wear,
but if a seal is damaged during bearing replacement, leakage
will increase and the seal should be replaced.
1. Remove the bearing housing,
following the appropriate bear-
ing removal instructions in this
manual.
2. Remove the heat fan if pres-
ent. Disk-type heat fans are
secured by two setscrews;
bladed heat fans are clamped
to the shaft.
3. Support the shaft and slide the
seal clear. Gently lower the
shaft.
4. Slide the new seal onto the
shaft, raise and recenter the
shaft, then seat the seal and
fasten securely.
CAuTIOn: use care; the seal material is soft and
easily damaged.
5. Disk-type heat fan: Use a feeler gage to position the fan
.050" from the seal face and tighten.
Bladed heat fan: Center the fan between the seal face and
the bearing journal and tighten.
6. Replace bearing(s) following the appropriate bearing
replacement instructions in this manual.
Labyrinth Seal