Ix. troubleshooting guide, Field-replaceable parts, Equipment service – Spencer Power Mizer Multistage Centrifugal Cast Blowers User Manual
Page 13: Material safety data sheets, Emergency service, Service and operating assistance
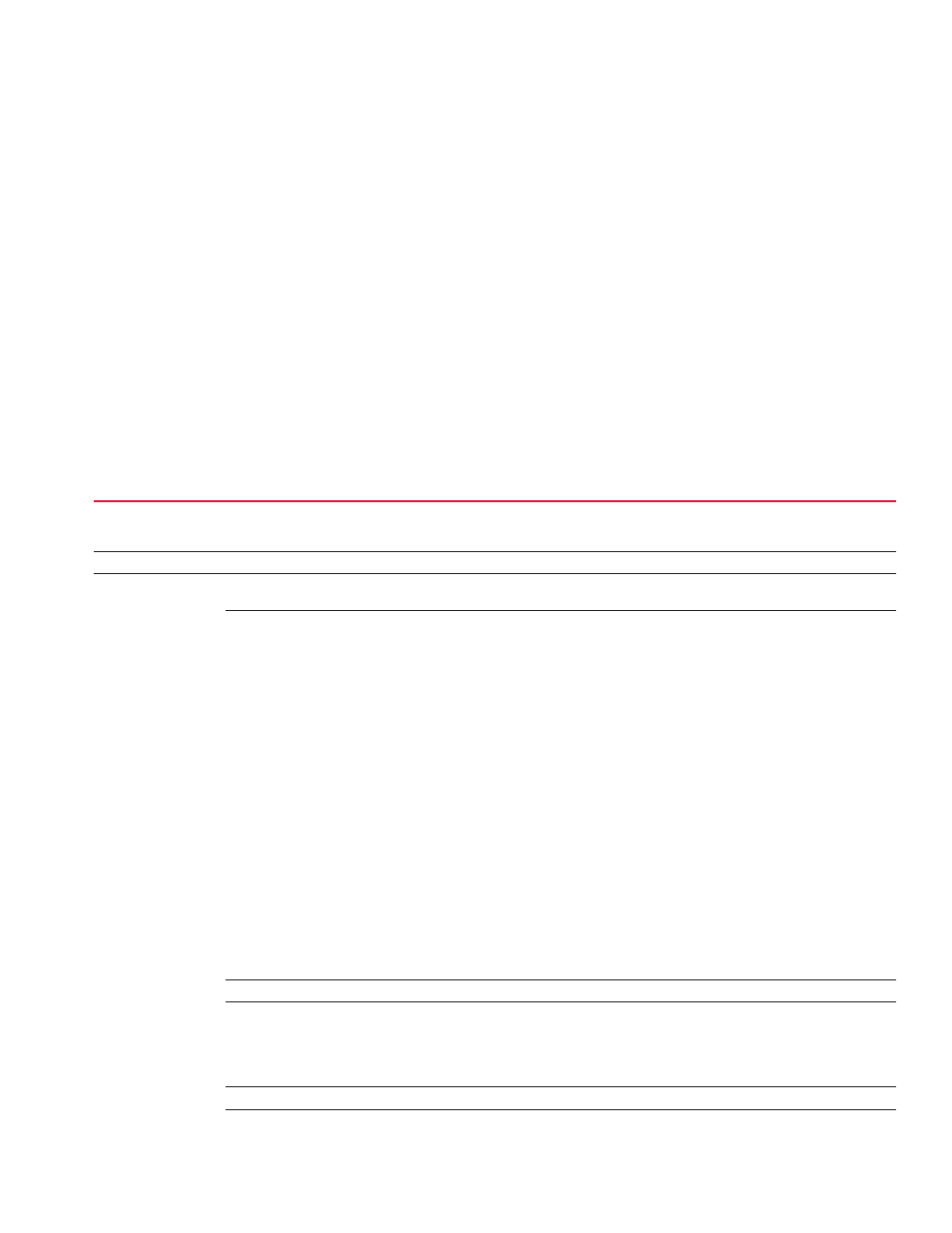
13
Field-Replaceable Parts
When ordering parts provide full information about your
Spencer equipment, including the serial number and model
number. Field-replaceable parts are restricted to the following:
• Drive end motor bearing
• Opposite drive end motor bearing
• Inlet bearings
• Discharge bearing
• Labyrinth seal or carbon ring
• Bearing cap gaskets
Equipment Service
Spencer provides prompt, courteous factory and field service
for all Power Mizer machines. To determine the nature of the
disorder and the best way to correct it, service personnel will
be dispatched to your location. We typically request a Purchase
Order prior to sending service personnel; however we will pro-
ceed on verbal orders in an emergency.
Once a full evaluation of the equipment has been performed
by our service personnel, you will be advised if the service
work is covered by the Spencer warranty. For out-of-warranty
services, please note that we accept Visa and MasterCard
charges as well as other forms of payment.
NOTE: Spencer products returned to the factory must be sent
freight prepaid and accompanied by a Return Service Order
(RSO) issued by the Spencer Service Department after we
receive your Purchase Order. Service costs will be quoted after
inspection and the work will be performed upon written accep-
tance of the quotation.
Material Safety Data Sheets
Spencer is committed to ensuring the safety of its employees. If
Spencer equipment has been exposed to potentially hazardous
contaminants or if Spencer service personnel could be exposed
to a potentially hazardous field environment, a Material Safety
Data Sheet (MSDS) is required (a) prior to dispatching Spencer
service personnel or (b) before receipt of any equipment for fac-
tory service. If special precautions are necessary to work on the
equipment, contact the Spencer Service Manager.
Emergency Service
Emergency service calls after normal working hours can be
routed through our voice mail system at 1-800-232-4321 and a
Spencer service representative will return your call promptly.
Service and Operating Assistance
Spencer Representatives are always available to help customers
achieve maximum equipment performance and reliability. Likewise,
Spencer service personnel will provide on-site instruction during
field service calls in the proper procedures to avoid a recurrence of
the problem encountered.
Indication: machine design capacity too small for the system
InSuFFICIEnT
AIR OR GAS
THROuGH
SYSTEM
Indication: low pressure/vacuum or volume as determined by gage measurement or process
• Incorrect rotation.
• Air or gas lines too small, causing
excessive friction loss.
• Valves in line not fully open or check
valve improperly installed.
• Inlet, discharge or piping system
partially blocked.
• High inlet temperature.
• Low inlet pressure.
• Machine not running at design speed.
• Low gas density or specific gravity.
• Machine air passages clogged.
• Impellers damaged by explosion, abra-
sion or vibration.
• Pressure or vacuum gage inaccurate.
Change motor leads to correct rotation.
Increase line sizes or install machine with higher output
pressure.
Open valves or inspect check valve.
Remove obstructions, clean filter.
Position inlet in a cooler area.
Check inlet for obstructions or install machine with higher dis-
charge pressure.
Refer to motor manufacturer’s instructions; check motor
speed; check voltage connections.
Check gas analysis and increase density or install machine
designed for prevailing conditions.
Consult Spencer Service Department.
Consult Spencer Service Department.
Calibrate gage; always use a “U” tube manometer for checking
pressure and/or vacuum.
• System requirements incorrectly
calculated by customer.
• System leaks or too many openings.
Install larger volume or lower pressure machine to handle sys-
tem requirements.
Locate and repair leaks, reduce number of openings.
Indication: measuring gas or air flow incorrectly
• Flowmeters calibrated incorrectly.
• No means of measurement available.
Calibrate flowmeters; use proper orifice for meter (check with
flowmeter manufacturer).
Obtain and install flowmeter.
IX. Troubleshooting Guide
PROBLEM
Possible Cause
Corrective Action