Butterfly valve, Filters, silencers and filter silencers, Check valve – Spencer Power Mizer Multistage Centrifugal Cast Blowers User Manual
Page 6: Electrical, Coupling alignment
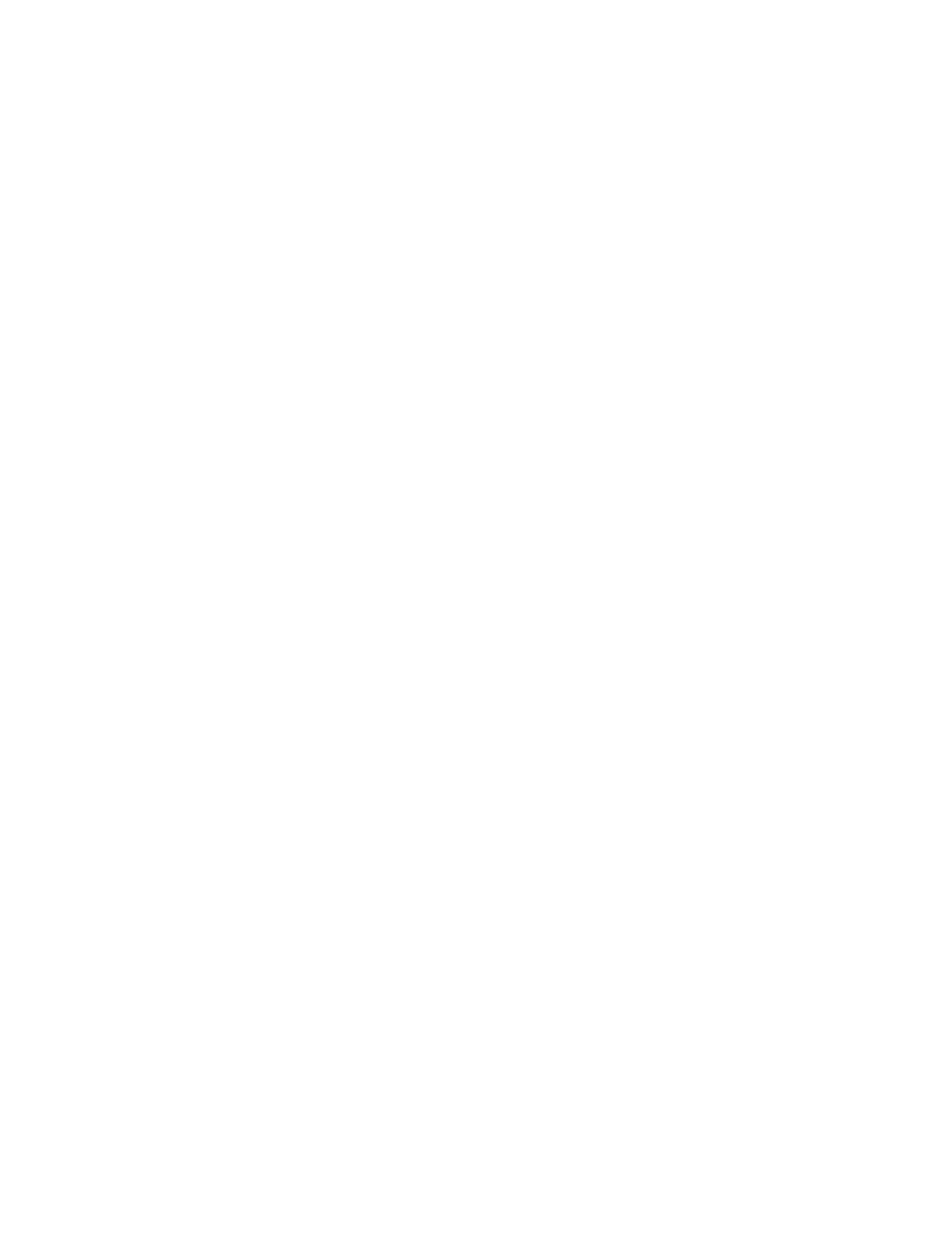
6
3. Butterfly Valve
To regulate (throttle) blower volume and/or pressure, a butterfly
valve may be installed–preferably on the inlet. A valve may also
be installed on the discharge as an isolation valve.
4. Filters, Silencers and Filter Silencers
Spencer blowers will accept a filter or filter silencer, typically
on the inlet, and a silencer, typically on the discharge. Inlet
filtration is recommended for pressure applications.
5. Check Valve
CAuTIOn: A check valve must be installed in the dis-
charge line (downstream of any blow-off line) of each
blower operating in parallel, or in the inlet line (upstream
of any bleed line) of each vacuum producer operating in
parallel to prevent reverse flow through idle units.
Orient the check valve during installation to equalize loading
on the valve shutters. Usually, the hinge post of the check
valve should be installed perpendicular to the blower shaft. If
the check valve is installed in a horizontal piping line, position
the valve shaft vertically. Make sure the internal moving parts
can move freely.
6. Electrical
NOTE: All wiring and electrical adjustments or installations
must be done by a qualified electrician in accordance with the
National Electrical Code and local codes.
CAuTIOn: The electrical service at the installation site
must supply the voltage stamped on the motor name-
plate. Operation at an incorrect voltage may damage the
motor and void its warranty.
Electrical Accessories. The following optional safety acces-
sories are available from Spencer. For copies of the product
bulletins listed, contact your Spencer representative or
www.spencerturbine.com.
• Load Control Safety Switch (LCSS) –
Bult. No. TDS90058 (TDS-223)
• Electronic Modulating Bleed Control (EMBC) –
Bult. No. TDS90056 (TDS-224)
• Bearing Temperature Monitor Control (BTMC) –
Bult. No. TDS90057 (TDS-222)
• Standard Blower Safety Control Panels (LCSS, BTMC and
VM, Vibration Monitor) – Bulletin No. TDS-237 and TDS-236
NOTE: Use of a BTMC, vibration monitor and an LCSS or
EMBC may be advisable in crucial or unattended applications,
anywhere there are wide load fluctuations, or where machines
are operating at high pressure or vacuum.
Both the LCSS and EMBC are designed to prevent a blower or
vacuum producer from operating in a low load (surge) condition.
7. Coupling Alignment
Good coupling alignment is critical for smooth machine opera-
tion.
Pre-startup alignment is necessary and is a customer
responsibility. Spencer recommends that each blower be field
aligned using a laser alignment system. Only qualified personnel,
following the laser equipment manufacturer’s instructions,
should attempt coupling alignment.
WARnInG: DISCOnnECT AnD LOCk OuT ELECTRICAL
POWER BEFORE PERFORMInG ALIGnMEnT.
Machinery Soft Foot
Imperfections or unevenness between the machine base and
any foot of the motor or blower creates a condition known as soft
foot, which may be parallel or angular. If uncorrected, soft foot
leads to increased stress and high vibration. Although both the
motor and blower feet were preset at the factory, each foot must
be checked for soft foot prior to alignment. Any vertical or angular
soft foot that exceeds .003" is excessive and must be corrected.
Laser Alignment Technique
Laser alignment is the only method Spencer uses and the only
one it recommends. Laser aligned systems have significant
advantages such as reduced maintenance costs and energy
consumption; prolonged life for bearings, seals and couplings;
decreased bearing temperatures and lower vibration levels. Many
laser systems also identify and measure soft foot conditions.
NOTE: Consult an alignment specialist if laser equipment is
not available.
Coupling Gap Adjustment
Use of a laser system eliminates the need to “break” the cou-
pling halves. The coupling gap may be left at the factory setting.
(Kop-Flex model “B” coupling gaps are 1/8" up to size 2-1/2"
and 3/16" for sizes over 2-1/2".)
Alignment should be performed at normal operating tempera-
tures. Recommended factory tolerance is ±.004" parallel and
1/4° angular at operating conditions.
Alignment Tips
• Make sure the blower is level before alignment.
• Mark the axial location of the motor before alignment as a
reference point to be sure it does not move.
• Avoid disturbing any factory-installed shims unless they are
to be replaced.
• Do soft foot corrections first; loosen all mounting bolts
before correcting any foot.
• During the final vertical adjustment of the motor, work on
one side at a time, loosening the jack bolts first so the motor
does not move laterally as mounting bolts are loosened.
• Use the smallest shim that will slide over the mounting bolts.
• Minimize the number of shims. One thick shim and 2–3 thin
shims are usually satisfactory.
• Remove all traces of dirt or contaminants from shims and
machine parts.
• Use stainless steel shims only.
• Never reuse shims.
CAuTIOn: After each alignment check, add coupling
lubricant if required.
Coupling Lubrication (grease lubricated)
Two coupling lubrication ports are located 180° apart.
Remove the setscrew lube plugs from both ports. Install
grease fitting in one port and rotate the coupling until the
grease fitting is angled down at 45°. Pump lubricant in until it
appears at the upper port. Remove the grease fitting; replace
and tighten the lube plugs.