Hoffman pump, Hoffman, Dealer ser vice – Bell & Gossett DN0153D HS Vacuum Heating Units Series HV User Manual
Page 9
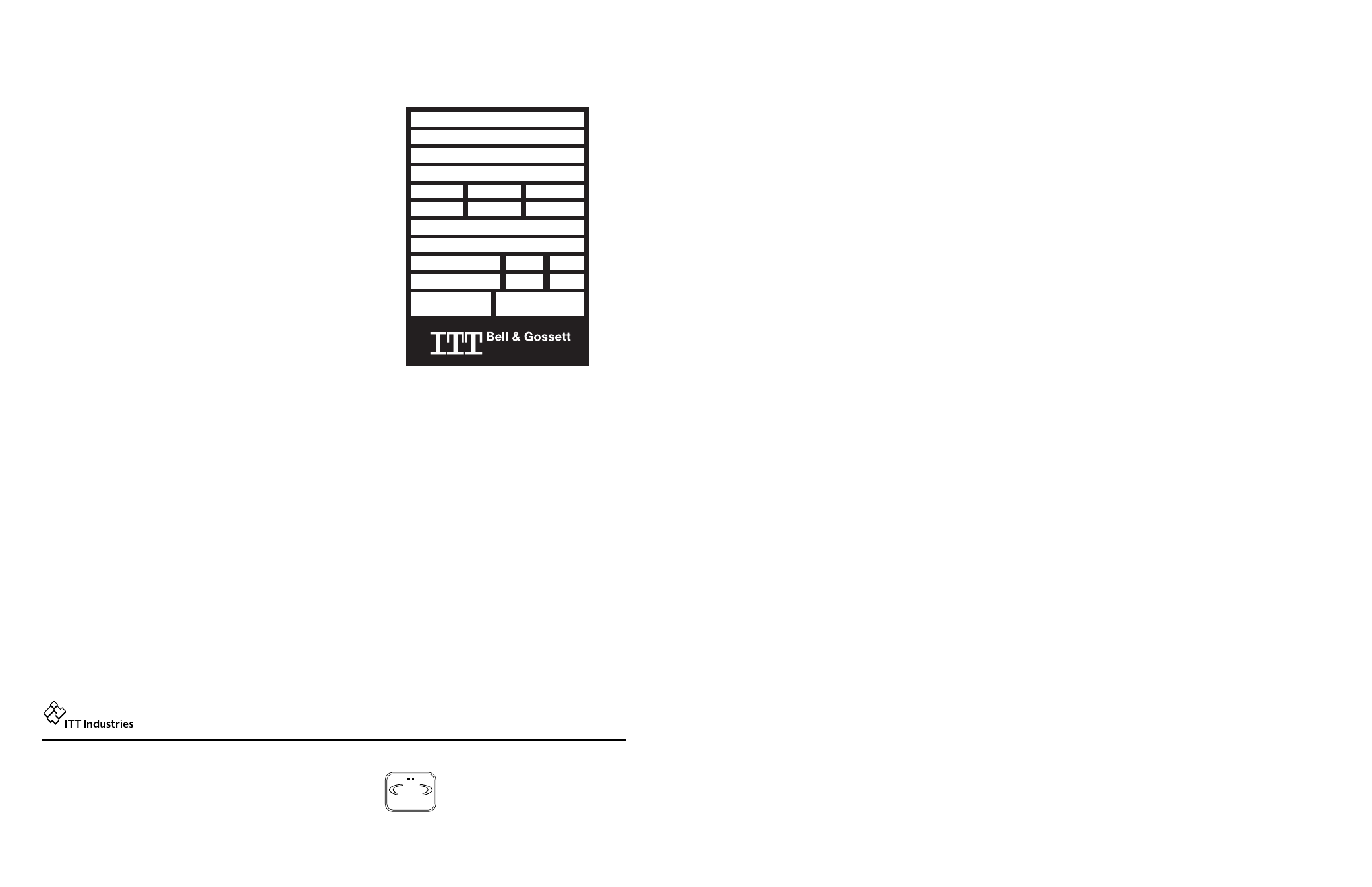
Hoffman Pump
© COPYRIGHT 1985, 2005 BY ITT INDUSTRIES, INC.
PRINTED
IN U.S.A. 3-05
USA
Bell &
Gossett
8200 N. Austin Avenue
Morton Grove, IL 60053
Phone: (847) 966-3700
Facsimile: (847) 966-9052
http://www.domesticpump.com
DIN ISO 9001
TUV
CERT
ISO 9001
Certified
DEALER SER
VICE
If trouble occurs that cannot be rectified, contact your local
B&G representative. He will need the following information in
order to give you assistance.
1. Complete nameplate data of pump and motor.
SEE RATING NAMEPLATE at right.
2. Vacuum readings.
3. Ampere draw of the motor.
4. A sketch of system piping.
ITT Fluid Technology Corporation
Morton Grove, Illinois 60053
TM
TM
SERIES HV
MODEL
SERIAL
GPM
PSI
PUMP
CFM
IN HG.
PUMP
DWGS
POWER V.
PH.
HZ 60
CONTROL V.
PH. 1
HZ 60
TOTAL
LARGEST MOTOR
F.L. AMP
F.L. AMP
DN0016
HOFFMAN
VACUUM PUMP RUNS CONTINUOUSLY OR FAILS TO
PRODUCE SUFFICIENT VACUUM*
1.
Selector switch is set on “continuous” or “hand”.
2. The temperature of the condensate is too high. Normal
operating condensate temperature should not exceed
160°F for rated capacities. Correct the cause for high tem-
perature condensate.
3. There are excessive leaks in the system piping preventing
the pump from producing sufficient vacuum to satisfy the
vacuum switch setting. To confirm this, make sure pump is
primed, close inlet valve, close equalizing line valve, plug
other check valve on this line, replace vacuum breaker with
plug and observe shut-off vacuum while pump is running.
4. The vacuum or float switch electrical contacts remain in
closed position. Adjust controls.
5. The nozzle, strainer, or impeller passageways are clogged
with foreign matter. Refer to instructions for cleaning.
6. A vacuum breaker is set too low. It should not admit air at
a vacuum within the range of the vacuum switch setting.
7. The pump has lost its hurling water. There should never be
less water than shown on float adjustment sketch. Loss of
hurling water may be caused by:
(1) Discharge valve leaks due to dirt or worn seat.
(2) Orifice in guide screw in discharge valve is closed.
(3) Discharge valve bellows is ruptured.
(4) Solenoid pilot valve remains in open position.
(5) Float switch failure.
Replace the bellows discharge valve with the solenoid
operated discharge valve. If the valve has already been
replaced with the solenoid operated discharge valve the
loss of hurling water may be caused by:
(1) Solenoid discharge valve leaks due to dirt or worn seat.
(2) Solenoid discharge valve stuck in open position.
(3) Check valve in nozzle body is leaking.
(4) Float switch failure.
8. Check valve in equalizer line or air vent line from receive or
accumulator tank leaks, or is installed backwards.
9. One nozzle body check valve, Figure 2, page 2, on duplex
pump remains open, permitting air to recirculate.
10. Pump is too small for the system.
11. Lower float switch does not turn off. Float rests on receiver
bottom and should be raised.
PUMP STARTS AND STOPS IN RAPID SUCCESSION
1.
A check valve in return line. Remove.
2. A partially closed inlet valve. Valve should be a gate valve
rather than globe.
3. A lift in return line at or near the pump. Low return lines will
fill with condensate between pump operations. The inertia
of the collected water may be quite great, and before the
vacuum suddenly produced by starting of the pump can
set the water in motion, the vacuum at the pump may
reach the cut-off point of the vacuum switch, thus stop-
ping the pump. The vacuum quickly recedes as the con-
densate moves into the receiver and the pump “trips in” on
vacuum control again, thus repeating this “hunting action”.
There are two ways to correct this difficulty:
(1) If the vacuum sensing line can be drained away from
the vacuum switch(es), connect this sensing line into
the nearest “dry” point in the return main so that the
operation of the unit may be governed by the vacuum in
the system.
(2) If the nearest “dry” point on the return main is more
than 2 ft. above the vacuum switch, relocate and recon-
nect the switches to sense the vacuum at this point. If a
separate selector switch for “Fl-Vac, “Float”, “Hand”
operation is not already furnished with the unit, one
must be provided for each vacuum switch for installa-
tion in control panel.
4. Elbow in return line too close to unit inlet. Correct as
described in item 3, or if there is no lift in the return line at
or near the pump, extend the
3
/
4
" equalizing line to top of
“dry” point on return main.
5. Equalizer line is improperly connected.
6. Strainer clogged with dirt. Clean strainer.
PUMP MAKES NOISE
1.
The pump is working against a lower pressure than
designed for. While pump is discharging, adjust square
headed steam cock in discharge line until pressure at
pump approaches pump rated pressure. Secure adjust-
ment of steam cock by tightening lock nut.
2. Excessive condensate temperature. Correct system
conditions.
3. Magnetic hum or bearing noise in motor. Consult motor
manufacturer’s authorized service station nearest pump
location.
4. Starter chatters. Trouble is caused by low line voltage,
poor connections, defective starter coil, or burned contacts.
5. Pump is running backward.
6. Water hammer when discharge valve closes:
(1) Adjust steam cock to reduce discharge velocity or
(2) Install surge chamber on boiler side of discharge check
valve or
(3) Install additional check valve near boiler or
(4) Install discharge piping 1 or 2 sizes larger.
THE SYSTEM IS NOISY
1.
Banging in the steam main is usually caused by “implod-
ing” in condensate lying in low points in lines. These
pockets can be eliminated by “dripping” low points,
properly supporting the pipe, or by increasing the pitch of
the lines.
2. Improper dripping of the steam mains and risers. Were
there is a rise in the steam main, or where it branches off
into a riser, a drip trap must be installed to the drain line.
3. The piping is too small to drain properly.
4. A defective trap is holding condensate in radiation.
5. A priming boiler is permitting a carry-over of water with the
steam. A priming boiler is caused by:
(1) Oil or other foreign matter. Clean boiler thoroughly.
(2) A reduction of the steam liberating area due to too high
water level in the boiler. Reduce water line.
(3) Overloading. Reduce firing rate.
(4) Undersized steam outlet area, resulting in velocities in
excess of 15 to 25 ft. per second.
*Product life and product efficiency are greatly affected by system maintenance.
A tight (leak-free) system with properly functioning traps is essential for efficient
operation.
9