Xylem A-C Fire Pump – Vertical Turbine Fire Pump AC8499 User Manual
Page 17
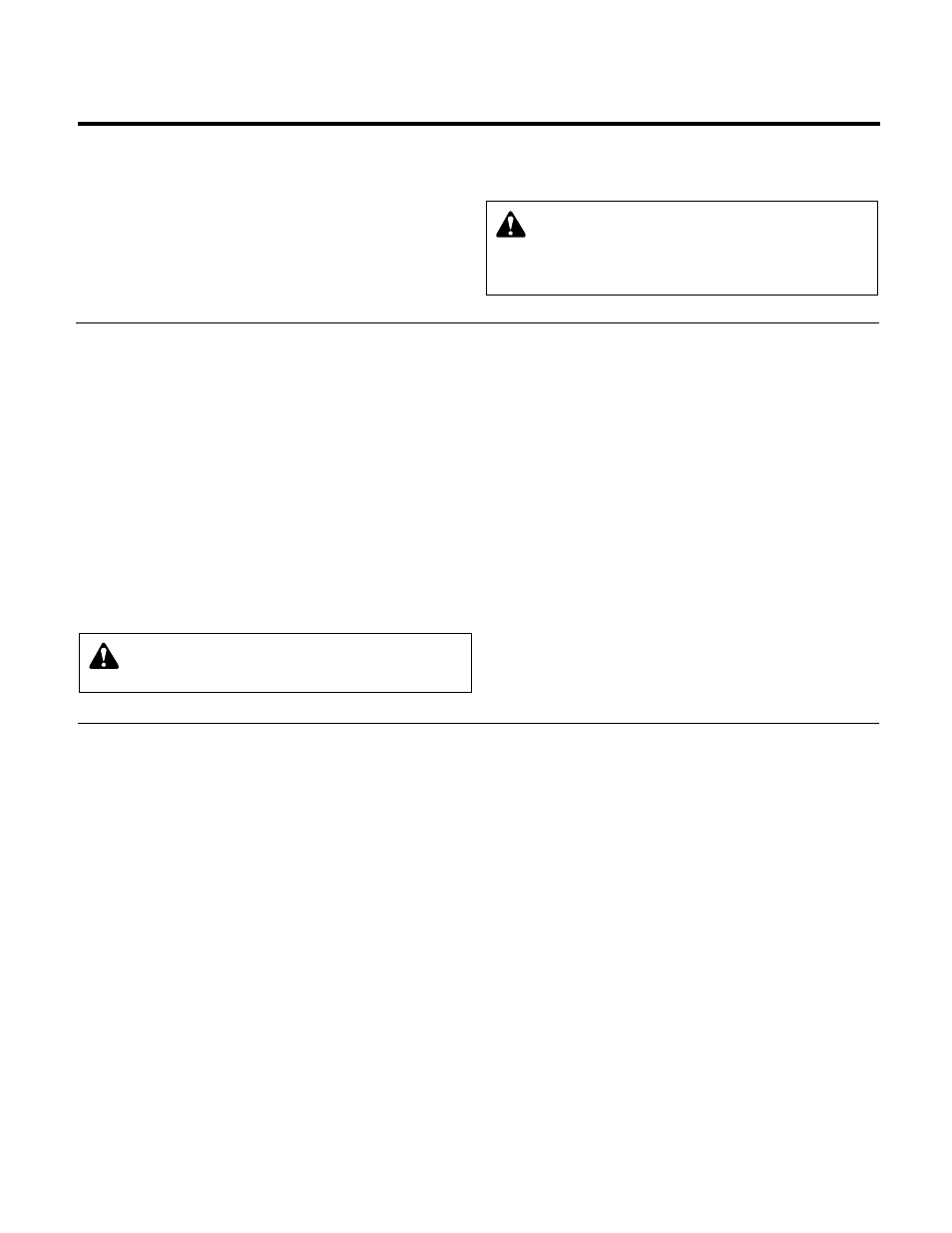
17
Pumps equipped with packing, shall be adjusted whenever
the leakage rate exceeds two drops per second. If there is no
leakage or the stuffing box overheats, stop the pump and
allow packing to cool. Back off gland nuts. This will allow the
entire set of rings to move away from the bottom of the box,
without relieving pressure of the packing on the shaft. Restart
the pump. It may be necessary to repeat this procedure sev-
eral times before proper amount of liquid comes through to
efficiently prevent overheating. If leakage is excessive, adjust
the stuffing box as follows:
1. With the pump in operation, tighten the gland nuts one-
quarter turn for each adjustment. Allow packing to equalize
against the increased pressure and leakage to grad-
ually decrease to a steady rate, before making another
adjustment.
2. With the pump shut down and when packing has been
compressed to the point that the gland is about to contact
the upper face of stuffing box, remove the split gland, add
one extra packing ring and readjust. If this fails to reduce
leakage to two drops per second, remove all packing rings
and replace with new rings.
3. Remove the packing with the aid of a packing hook. If a
lantern ring is provided, remove it by inserting a wire hook
in the slots of the ring and pull it from the packing box.
Thoroughly clean the stuffing box of all foreign matter.
4. If the replacement packing is in the form of a continuous
coil or rope, it must be cut into rings before installing.
Tightly wrap one end of the packing material around the
top shaft like one coil spring, and cut through the coil with
a sharp knife. For re-packing sequence, refer to "Stuffing
Box Installation" (page 13).
Packing Adjustment & Replacement
Thrust Pot Lubrication & Maintenance
It is a good practice to flush the oil reservoir before first time
operation, and at the time of oil changes, to remove all grit
particles in the oil reservoir container. Use the same type of
oil to flush reservoir as specified for lubrication. Because of
the special nature of the TURBINE OIL recommended, it is
wise to keep a supply on hand. Remove drain plug before
flushing. Flushing oil may be poured through oil fill opening in
cover after removing oil fill plug. The proper oil level when the
unit is not running shall not be more than 1/8" to 1/4" from the
top of the oil sight gauge. Overfilling may result in overheating
of the unit. During operation the oil level in the sight gauge
may be higher than the recommended range mentioned
above. Under no circumstances is it allowed to rotate the unit
when the oil in the sight gauge is not at the required level. To
avoid oxidation of the anti-friction bearings during shut-down
periods lasting longer than one week, it is recommended to fill
up the oil reservoir until the oil runs over the oil retainer tube
and down the shaft so that the bearings remain completely
immersed in the oil. Before startup, do not forget to drain the
excess oil to its required level. Oil change depends on the
severity of the environment. Generally speaking, when the oil
in the sight gauge changes to a darkish brown color, it is time
for an oil change. However, for a longer bearing life, it is
recommended that the oil be changed every six months. Be
sure to flush the oil reservoir, as noted above, with each oil
change.
CAUTION
: Do not overtighten the stuffing box. Ex-
cessive pressure can wear out packing prematurely
and seriously damage the shaft.
Section 5 - Preventive Maintenance
Preventive maintenance includes periodic inspection of oil
level in thrust pots, re-lubrication of electric motors, gear dri-
ves and prime mover. Systematic inspection of the pump and
its components shall be made at regular intervals. The fre-
quency required depends upon the operating conditions of
the pump and its environment. See Page 17 for Preventive
Maintenance Procedures. Consult the applicable manufac-
turer’s instructions for detailed information on maintenance
for the prime mover, driveshaft, electric motors and gear
drives. Any deviation in performance or operations from what
is expected can be traced to some specific cause. Variances
from initial performance will indicate changing system condi-
tions, wear, or impending breakdown of the unit.
WARNING:
Before initiating maintenance procedures,
disconnect all power sources to the equipment and
accessories and compleyely discharge all parts and acces-
sories which retain electric charge. Failure to comply may
result in severe personnel injury or death.