Start-up – Analytical Industries GPR-1200 MS ATEX Portable PPB Oxygen Analyzer User Manual
Page 12
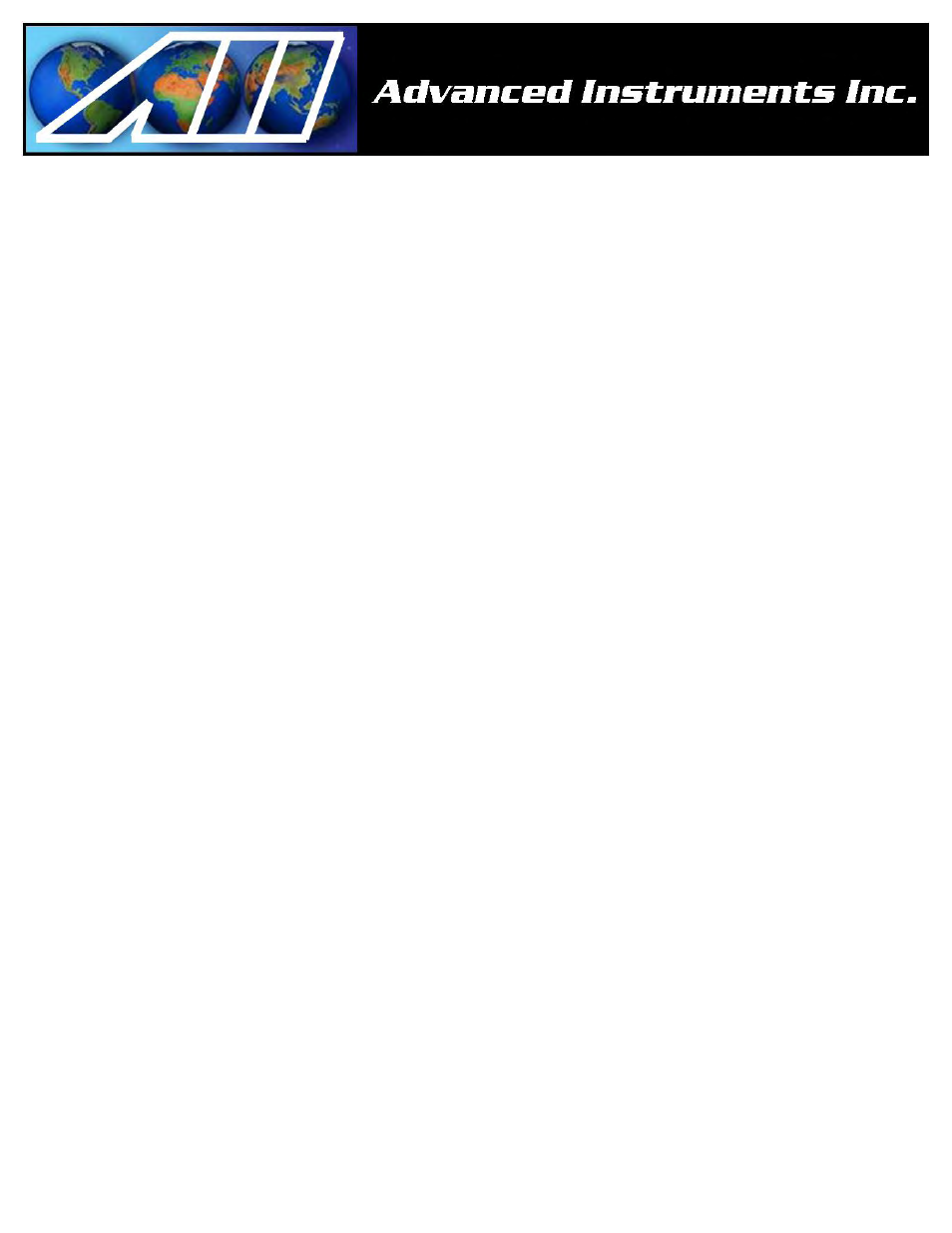
12
Example:
As illustrated by Graph A any error, play in the multi-turn span pot or the temperature compensation circuit, during
a span adjustment at 20.9% (air) of full scale range would be multiplied by a factor of 4.78 (100/20.9) if used for
measurements of 95-100% oxygen concentrations. Conversely, an error during a span adjustment at 100% of full
scale range is reduced proportionately for measurements of lower oxygen concentrations.
Recommendation: Calibrating with a span gas approximating 80% of the full scale range one or two ranges
higher than the full scale range of interest is recommended for 'optimum calibration accuracy'.
Start-up
The GPR-1200 MS Portable ppm Oxygen Analyzer is fully operational from the shipping container with the oxygen
sensor installed and calibrated at the factory prior to shipment. Once installed, we recommend the user allow the
analyzer to stabilize for 30 minutes and then recalibrate the device as instructed below.
Assemble the necessary hardware for optional components - such as coalescing or particulate filters and pumps,
1/8” metal or plastic tubing for interconnecting the analyzer and optional components.
Review the application conditions to ensure the sample is suitable for analysis.
¾ Temperature: The sample must be sufficiently cooled before it enters the analyzer and any optional
components. A coiled 10 foot length of ¼” stainless steel tubing is sufficient for cooling sample gases as high as
1,800ºF to ambient.
¾ Pressure & Flow: As described above.
¾ Moisture & Particulates: Prevent water and/or particulates from entering the sample system. They can clog the
tubing and damage the optional components such as pumps, scrubbers or sensors. Installation of a suitable
coalescing or particulate filter is required to remove condensation, moisture and/or particulates from the sample
gas to prevent erroneous analysis readings and damage to the sensor or optional components. Consult the
factory for recommendations concerning the proper selection and installation of components.
¾ Contaminants: A gas scrubber and flow indicator with integral metering valve are required upstream of the
analyzer to remove interfering gases such as oxides of sulfur and nitrogen or hydrogen sulfide that can produce
false readings and reduce the expected life of the sensor. Installation of a suitable scrubber is required to
remove the contaminant from the sample gas to prevent erroneous analysis readings and damage to the sensor
or optional components. Consult the factory for recommendations concerning the proper selection and
installation of components.
¾ Gas connections: Inlet and outlet vent gas lines require 1/8” diameter tubing preferably metal.
¾ Power connection: Locate a source of AC power to meet area classification and to plug in the charging adapter.
¾ Zero calibration (required only for very low percentage range measurements).
¾ Span calibration – Users are responsible for certified span gas cylinder, regulator and flow control valve.